Intergranular Oxidation
IGO is a surface phenomenon that is most often associated with atmosphere gas carburizing (Fig. 1). The consequence of IGO (and the concentration gradients that develop during oxide formation) is that the material adjacent to the oxides has modified transformational behavior. Instead of forming martensite on quenching, steels with this condition develop non-martensitic transformation products (e.g. bainite, pearlite), which adversely affect mechanical properties (e.g. hardness, residual stress, bending fatigue).
The rate of diffusion of oxygen into a steel surface is dependent on the oxygen potential of the furnace atmosphere and the process variables (i.e. the depth of oxide penetration is influenced by case depth, time at carburizing temperature, carbon potential and the chemical composition of the steel).
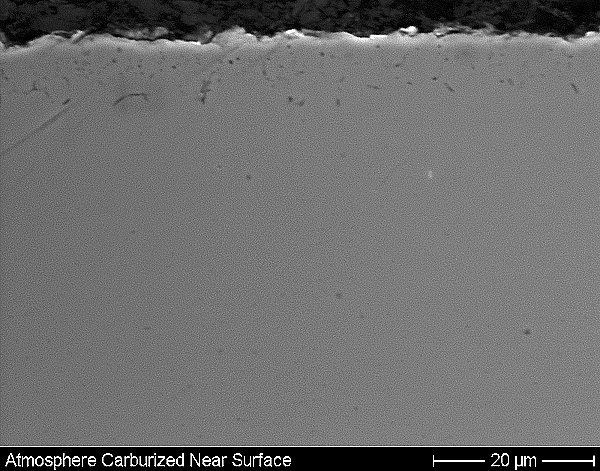
During the carburization process, the oxygen atoms (which are about 35% smaller than the iron atoms) are released as a direct result of the presence of water vapor and carbon dioxide in the furnace atmosphere. Oxygen diffuses slowly into the steel surface (as does carbon and hydrogen, albeit more quickly) and migrates to the grain boundaries. Once in the steel, oxygen combines chemically with the elements already present (e.g. chromium, titanium, manganese) that have an affinity for oxygen.
The depth of the IGO layer can vary. For neutral hardening in an Endothermic gas atmosphere, an IGO layer of 0.0075 mm (0.0003”) to 0.0127 mm (0.0005”) can be expected. For carburizing, an IGO layer of 0.025 mm (0.001”) or greater can be expected for case depths under 2 mm (0.078”). Heavier case depths will produce deeper IGO layers. IGO appears microscopically in the form of grain boundary penetration from the surface inward (Fig. 2).
Preventing IGO
The use of vacuum carburizing (a.k.a. low pressure carburizing or lpc) is known to eliminate IGO (Fig. 3), provided there are no oxygen bearing products carried into the process chamber (see Reference 2). In atmosphere gas carburizing, IGO will always be present to some extent (because of the process gas chemistry) but can be reduced if an oxygen-free atmosphere is used. If IGO is present, removal of the surface layer is the only way to eliminate it.
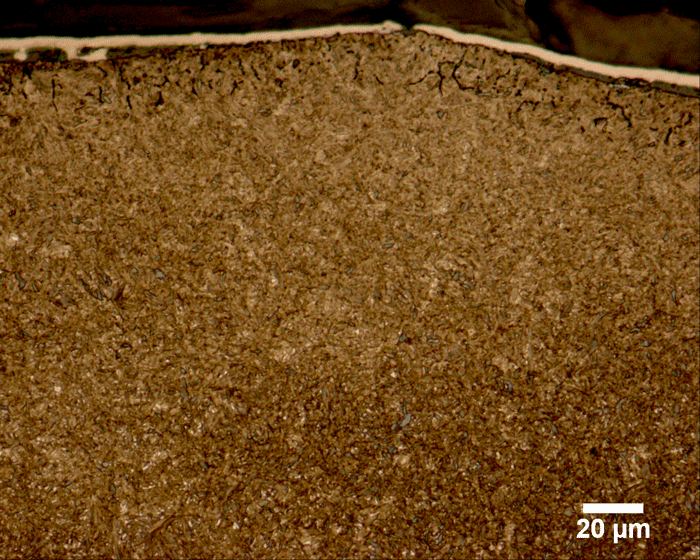
Intergranular Attack (a.k.a. Intergranular Corrosion)
An intergranular attack is caused by the segregation of impurities at the grain boundaries or by enrichment or depletion of one of the alloying elements in the grain boundary areas.
During heat treatment certain conditions can cause a material to become susceptible to intergranular attack (a.k.a. intergranular corrosion or intergranular stress corrosion cracking). This phenomenon is characterized by a localized attack at the grain boundaries, leaving the grains themselves relatively untouched. The component can experience loss of corrosion resistance, strength, and loss of other mechanical properties.
In austenitic stainless steels and nickel alloys (e.g. Inconel 600 and Incoloy 800) for example, where chromium is added for corrosion resistance, the mechanism involves the precipitation of chromium carbides at the grain boundaries (Fig. 4). The result is the formation of chromium-depleted zones adjacent to the grain boundaries setting up, in essence, a galvanic cell causing localized corrosion. In the case of austenitic stainless steels, this results from either heating and soaking in, or slow cooling through the temperature range of about 520°C – 800°C (970°F – 1475°F), as often happens during welding or (improper) heat treatment.
Anisotropic alloys, where extrusion or heavy cold work leads to the formation of long, flat grains, are especially prone to intergranular corrosion. An example is high strength aluminum alloys that can undergo exfoliation corrosion (where the corrosion products build up between the flat, elongated grains and separate them). A consequence of this type of processing is a lifting of the surface (a.k.a. leaf effect) and often propagates from the edges of the material through its entire structure.
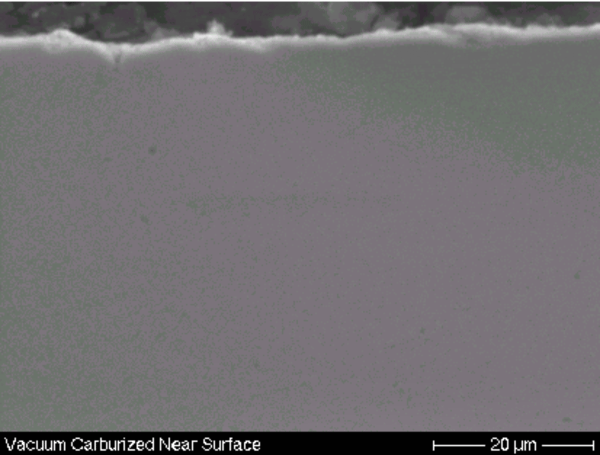
Other aluminum-based alloys are sensitive if there are layers of materials acting as anodes between the aluminum-rich areas. Intergranular corrosion is a concern especially for aluminum alloys with a high percentage of copper. In other aluminum alloys, small amounts of iron are known to segregate in the grain boundaries and cause intergranular corrosion. High-strength aluminum alloys such as the Duralumin alloys (Al-Cu) which depend upon precipitated phases for strengthening are susceptible to intergranular corrosion following sensitization at temperatures of about 120°C (250°F).
Knifeline attack (KLA) is yet another related kind of intergranular attack, which occurs in stainless steels, stabilized by niobium (e.g. 347). This material contains titanium and niobium and their carbides dissolve into the steel at very high temperatures. At some cooling rates, however, niobium carbide does not precipitate, and the steel then behaves like an unstabilized grade, forming chromium carbide instead. This affects only a thin zone several millimeters wide often making it difficult to spot and increasing the corrosion speed. Structures made from these steels must be heated to approximately 1065°C (1950°F), where the chromium carbides can re-dissolve and niobium carbides reform. The cooling rate after this treatment is not important, as the carbon that would otherwise pose a risk of formation of chromium carbide is already combined with niobium.
Certain Cr-Mn and Cr-Mn-Ni steels are also susceptible to intergranular corrosion following sensitization in the temperature range of 420°C – 850°C (790°F – 1560°F).
Copper-based alloys become sensitive when depletion of copper in the grain boundaries occurs. It has been shown that the zinc content of brass is higher at the grain boundaries and subject to such corrosion.
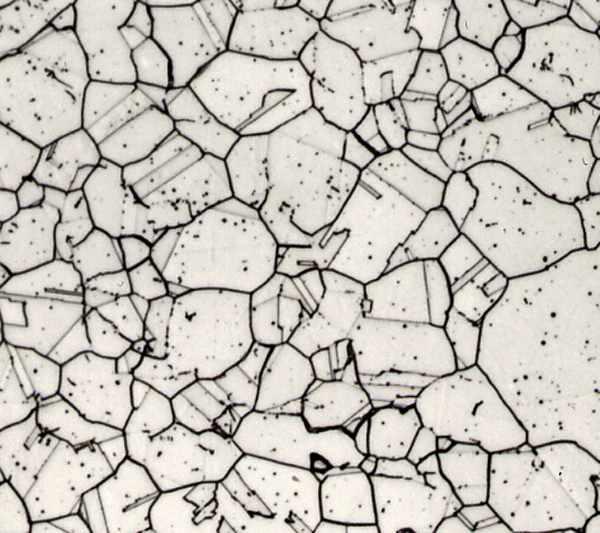
Finally, other kinds of alloys can also undergo exfoliation (i.e. lamellar corrosion), for example, the sensitization of cupronickel with increasing nickel content. Alloys of iron can also be susceptible to lamellar corrosion (since the volume of iron oxides is about seven times higher than the volume of original metal) leading to the formation of internal tensile stresses tearing the material apart. Similar effects lead to the formation of lamellae in stainless steels, due to the difference of thermal expansion of the oxides and the metal.
Preventing IGA
Several methods have been used to control or minimize the intergranular corrosion of susceptible alloys, particularly of the austenitic stainless steels. For example, a high-temperature solution heat treatment (a.k.a. solution annealing, quench annealing or solution quenching) can be used. The stainless steel alloy is heated into the temperature range of about 1060°C – 1120°C (1940°F – 2050°F) and then rapidly quenched (e.g. water or high-pressure gas). This method is generally unsuitable for treating large assemblies and can be ineffective where welding is subsequently used.
Another control technique for preventing intergranular corrosion involves the addition of strong carbide formers (a.k.a. stabilizing elements) to the alloy (e.g. niobium, titanium, or tantalum) into stainless steel. These elements have a much greater affinity for carbon than chromium and preferentially form carbides thus reducing the carbon available in the alloy.
The use of low carbon (“L” grades) of stainless steel where the carbon content is under 0.03% can be used so that there is insufficient carbon for chromium carbide formation. However, sensitization may still occur with time. It should also be noted that the low-carbon steels also frequently exhibit lower strengths at high temperatures.
Summary
Proper material selection and the avoidance of manufacturing practices or heat treatment conditions known to create IGO and IGA are the best way to negate their effect on mechanical properties. Metallurgical analysis of representative parts or test coupons is the most positive way to detect these types of phenomena before components are sent out into the field.
References
- Parrish, Geoffrey, Carburizing: Microstructure and Properties, ASM International, 1999.
- Herring, Daniel H., and Robert V. Peters Jr., Technical and Process Advantages of Low-Pressure Vacuum Carburizing Using Chemical Acetylene with DMF Solvent, Gear Technology, September 2013.
- Pye, David., What is Intergranular Oxidation?, The Experts Speak Blog, Industrial Heating, October 2009.
- Wikipedia (www.wikipedia.com).