The movement of gases is an important and interesting subject but one often dismissed as a topic best left to scientists. However, the Heat Treater needs to know something about the basic nature (theory) of gases and in particular how they behave in vacuum. The main difficulty is that too much theory tends to become a distraction. Our focus here will be to better understand what goes on inside a vacuum furnace (Fig. 1).
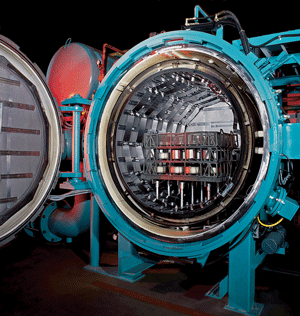
One definition of a gas is that it is simply a collection of molecules in constant motion (Fig. 2). The higher the temperature, the faster these molecules move, and as one might expect, the motion of gas molecules stops or dramatically slows down at or near absolute zero (0°K).
As molecules speed up with an increase in temperature, there is an increase in their kinetic energy (or energy of motion). Molecular collisions occur between molecules and if contained, these molecular collisions against the walls of their container result in a pressure rise (which always occurs in a closed container when a gas is heated). In other words, pressure is simply the force per unit area that a gas exerts on the walls of its container.
At atmospheric pressure, one cubic centimeter (1 cc) of air contains 2.69 x 1019 molecules all moving around in a random motion. This results in a fantastic number of collisions. The mean free path between molecules (or the average distance a molecule can travel before colliding with another molecule) is 2.6 x 10-6 inches. So if we pump a one cubic centimeter volume down to 1 x 10-3 Torr (one micron), which is a vacuum level commonly used in many heat treatment operations, we still have a whopping 4 x 1013 molecules remaining!
How then can this be an acceptable condition for heat-treating, especially when about 20% of the remaining molecules are oxygen? The answer is that the mean free path increases tremendously thus reducing the probability of molecular collision with each other and since the number of molecules (density) has been reduced, fewer collisions occur with the surface of the workpiece. This results in even fewer collisions of oxygen molecules with the work surface and no visible oxidation forms.
For example, if we pumped down to 1 x 10-9 Torr, or one millionth of a micron, the number of molecules per cubic centimeter is decreased to 4 x 107 and the mean free path is 5,000,000 cm (over 30 miles!). The path of the molecules is now limited by the walls of the vessel and not by the collisions between molecules. Flow, as we know it, doesn’t exist. This is the reason for the relatively large opening and piping used for diffusion pumping systems. If the opening to the diffusion pump weren’t that large, any molecules that migrated into the pump suction stream would rebound and move to other parts of the chamber.
An Brief Explanation of the Gas Laws
It turns out that any gas can be completely described in terms of the following basic values:
- Pressure (P)
- Volume (V)
- Temperature T)
- Number of molecules (n)
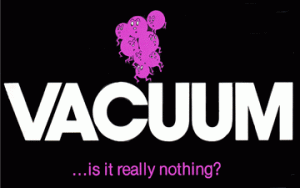
The Gas Laws, therefore, are formulas that simply allow us to relate (or calculate) the value of one of the basic quantities in terms of the others. Let’s review each of them briefly.
(1) Boyle’s Law: P1V1 = P2V2
This formula tells us that if the temperature is held constant, the increase in pressure is exactly proportional to the decrease in volume.
(2) Charles’ Law: P1/T1 = P2/T2
This formula tells us that an increase in pressure is directly proportional to the increase in the absolute temperature if the volume is held constant.
(3) Avogadro’s Law: P1/n1 = P2/n2
This formula tells us that equal volumes of any gas at the same temperature and pressure contain the same number of molecules.
A formula that relates all four of the quantities needed to completely describe the state of a gas is
(4) Ideal Gas Law: PV = nRT
Here R is a constant known as the universal gas constant and has a value of 62.4 Torr-liter/mole-°K.
Another useful gas law is the law of partial pressure known as
(5) Dalton’s Law: PTOTAL = P1 + P2 + … + Pn
This formula tells us that in a mixture of gases in which the gases do not react chemically, each gas exerts its own pressure independently as if no other gases were present.
Other characteristics that help describe the behavior of gases in a vacuum environment include:
- The Kinetic Theory of Gases
- Mean Free Path of Molecules
- Phase Change
- Evaporation
- Condensation
- (Dynamic) Equilibrium
- Vapor (Partial) Pressure
- Gas Flow
- Resistance to Gas Flow
- Gas Conductance
Let’s briefly talk about each.
The Kinetic Theory of Gases
This theory is used to explain the behavior of gases in terms of the behavior of the individual gas molecules. Gases are in constant motion, hence it makes sense to discuss their kinetic nature. Remember also that gases are free to wander throughout the space available to them. So, the temperature of a gas is simply a measure of this kinetic nature of the particles, that is their kinetic energy; the higher the temperature, the faster and faster the molecules move and the greater their kinetic energy. By comparison, pressure is related to the number of collisions of molecules against the walls of their container. An increase in temperature causes molecules to hit harder and more often, creating even higher pressure (in accordance with Charles’ Law). Similarly, a decrease in temperature causes molecules to hit less hard and less often, resulting in lower pressure.
If you were to remove some of the gas from the vacuum vessel, fewer molecules are left to make contact with the walls and the pressure is lower (in accordance with Avogadro’s Law and the Ideal Gas Law). Decreasing the volume of gas (at constant temperature) results in a reduced area which the original number of molecules strike thus causing the pressure to increase (in accordance with Boyle’s Law).
Mean Free Path
The mean free path, or distance between molecules can be calculated from the kinetic theory as follows:
where ? is the mean free path in centimeters, D is the diameter of the gas molecule in centimeters, an n is the number of gas molecules per cubic centimeter.
What is important is that this formula tells us that pressure, which is proportional to the number of molecules per unit volume (in accordance with the Ideal Gas Law) is inversely proportional to the mean free path, that is, as the pressure decreases the mean free path between molecules increases.
Phase Change
If we change the state of matter by changing the temperature or pressure (or both) we change the phase in which it exists. In vacuum, as we pump down we reduce the pressure and temperature and convert some of the moisture in the air to ice crystals.
Dynamic Equilibrium and Vapor Pressure
When the number of molecules leaving a part surface is equal to the number of molecules returning to it (that is, when the rate of evaporation equals the rate of condensation) the system is said to be in dynamic equilibrium. The partial pressure of the vapor at which it occurs is the vapor pressure of the material.
Gas Flow
The rate at which gas flows through the vacuum vessel into the pump is important in vacuum systems. This determines the time required to reach operating pressure and may ultimately determine the system’s tolerance to leaks and outgassing.
What Happens When We Pump Down A Vessel?
In the Range of 760 to 1 Torr
The initial pumpdown stage in any vacuum furnace is from atmospheric pressure to about 1 Torr. The air initially in the vessel at this point has a relatively high relative humidity and begins to be removed. As the pressure decreases, water vapor condenses (due to a cooling effect brought about by the sudden drop in pressure). Thus a “fog” develops, that is, a cloud of gas swirls around the interior with turbulence that is characteristic of gas flow at high pressure and high flow rate. The net result is a loss of pumping efficiency. This is one reason we should not keep a vacuum furnace open longer than absolutely necessary when loading and unloading and that the size of the mechanical pump and blower is important in mitigating this phenomenon.
Over time, a (slow) change in the composition of the gas remaining in the vessel takes place. Initially air is the major component of the gases. Certain oils, grease, and water exist, usually on the sides of the vessel. Eventually almost all the air is pumped out – the grease and water will continue to evaporate and their partial pressures will constitute a much larger proportion of the total pressure. The main concern during this phase is workload contamination due to impurities.
One of the added dangers of rapid pumpdown is the conversion of water vapor to ice crystals. Once in solid form, the water can no longer be removed. This is one of the reasons why the vacuum level rises at the onset of heating. One way to help mitigate this phenomenon is to perform a double pumpdown before heating, that is, pump the chamber down to around -28” Hg, isolate the pumps and backfill the chamber to around – 5” Hg and then pump down again. Often times, especially in extremely humid conditions, this technique actually finds the chamber pumping down to ultimate vacuum faster.
In the Range of 1 to 1 x 10-4 Torr
As we continue to reduce the vacuum level, from 1 Torr to 1 x 10-3 or 1 x 10-4 Torr, the ability of the gases remaining in the vessel to conduct heat begins to decrease rapidly. There is also a change in the electrical characteristics of the gas and the voltage necessary to start a (glow) discharge decreases as well.
In the Range of 1 x 10-4 to 1 x 10-6 Torr
As we continue to lower the vacuum level toward 1 x 10-6 Torr, we see a decrease in molecular density and an increase in sliding friction. In this vacuum range, molecules collide with the sides of the vessel as often as with each other.
In Summary
So there you have it! Enough theory to make sense of the various interactions taking place inside your vacuum furnace but not so much as to overwhelm or confuse. If you are interested to learn more, there are a number of textbooks available (see references) that advance the theory of gases far beyond this expose.
References
1. Herring, Daniel H., Vacuum Heat Treatment, BNP Media Group, 2012.
2. Kimball, William H., Vacuum…is it really nothing? C. I. Hayes Inc., 1977.
3. Brunner Jr., William F. and Batzer, Thomas H., Practical Vacuum Techniques, Robert E. Krieger Publishing Company, 1974.
4. Dushman, Sual, Scientific Foundations of Vacuum Technique, Second Edition, John Wiley & Sons, 1966.
5. Handbook of Vacuum Science and Technology, Dorothy M. Hoffman, Bawa Singe and John H. Thomas III (Eds.), Academic Press, 1998.
Daniel H. Herring / Tel: (630) 834-3017) /E-mail: dherring@heat-treat-doctor.com
Dan Herring is president of THE HERRING GROUP Inc., which specializes in consulting services (heat treatment and metallurgy) and technical services (industrial education/training and process/equipment assistance. He is also a research associate professor at the Illinois Institute of Technology/Thermal Processing Technology Center.