Highly distortion prone gearing (Fig. 1) was the subject of an investigation into the dimensional changes which result from utilizing either oil or high pressure gas quenching following a low pressure vacuum carburizing process. For comparative purposes, the gears in question were also atmosphere gas carburized and plug quenched, which is standard practice for these geometries.
![]() |
![]() |
Figure 1 – SAE 8620 Test Gears | Figure 2 – Typical Furnace Load Weighing 385 kg (850 lb.) |
Full production loads (Fig. 2) were run using two (2) different carburizing methods (atmosphere, vacuum) in combination with free quenching in either oil at 75°C (165°F) or high pressure gas (nitrogen) at 11 bar.
Sampling Method
Gears were taken from multiple locations throughout each load for analysis. Parts for metallurgical evaluation were selected from the center of each load. Multiple areas on each part were then analyzed for microstructure, case depth, and hardness (surface, profile, core). Dimensional checks (out of round, gear tooth profiles) were conducted on the gears before and after heat treatment. For brevity, only a portion of the complete test program is presented here (see Reference 4 for more detail).
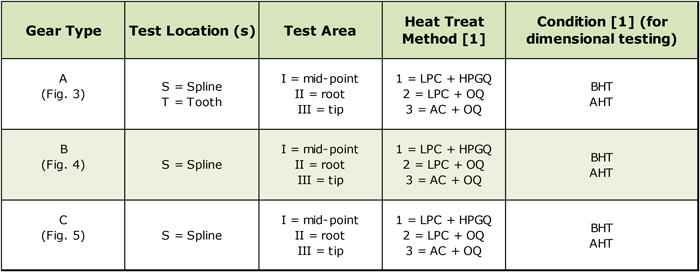
Notes:
1. Abbreviations used: low pressure carburizing (LPC), high pressure gas quenching (HPGQ), atmosphere carburizing (AC) and oil quench (OQ); before heat treatment (BHT); and after heat treatment (AHT)
2. Existing heat treatment method is atmosphere carburizing (AC) and plug quenching.
![]() |
![]() |
![]() |
Figure 3 – Clutch Gear Test Gear Type “A” | Figure 4 – 4” Clutch Hub Test Gear Type “B” | Figure 5 – 6” Clutch Hub Test Gear Type “C” |
Process Parameters
Carburizing was performed at 960°C (1760°F) for 3.34 hours followed by either oil quenching (variable agitator speed) or high pressure gas quenching. Targeted surface carbon content was 0.72%C (vacuum) and 0.80 -0.90%C (atmosphere). Gas quenching utilized four (4) changes in speed and pressure made through the critical transformation range of the material while the oil quench utilized two (2) changes in speed (70% and 40%). Tempering was performed at 150°C (300°F) for two (2) hours at temperature.
Test Results – Hardness
Surface hardness of all low-pressure vacuum carburized gears was in the 64 – 65 HRC range. Atmosphere carburized gears exhibited a slightly lower surface hardness, in the 62 – 63 HRC range (due to the presence of retained austenite). The depth of high hardness (> 58 HRC) was 0.05 – 0.13 mm (0.002” – 0.005”) deeper for the low-pressure vacuum carburized gears than for the atmosphere-carburized gears. The root-to-pitch line case depth ratio was 92 – 94% (vacuum carburizing) versus 63% (atmosphere carburizing).
Test Results – Distortion
Dimensional variation was determined by measuring both out of round (Table 1) and by coordinate measuring machine (CMM) measurement of the gear tooth profiles (Figs. 6 -13). With respect to the gear charts, the lead was measured across the tooth or spline from side to side at the pitch diameter. This method was checked for excessive taper. The involute measurement was taken on the tooth form (active profile), starting from the root diameter to the tip of the tooth. Indexing (index error) measured the tooth spacing from tooth to tooth around the gear. Gear or spline run-out measured variation of concentricity of the centerline (datum) of the gear.
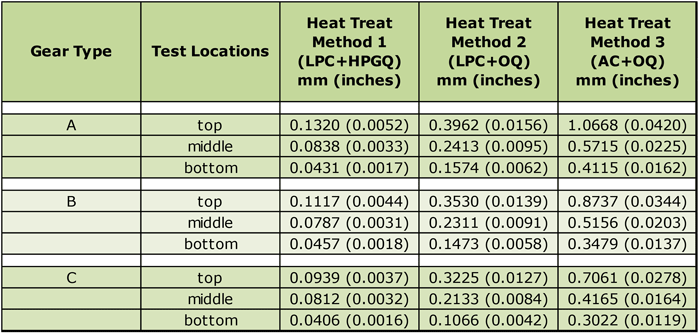
Notes:
1. The existing heat-treating method (atmosphere carburizing and plug quenching) results in out of round values typically in the range of 0.0508 – 0.0762 mm (0.002” – 0.003”).
![]() |
![]() |
![]() |
Figure 6 – Sample C Before HT | Figure 7 – Sample C Before HT | Figure 8 – Sample C Before HT |
Test Results – Microstructure
Analysis of part microstructures was taken from all areas (tip, mid-radius, root) and in the case of vacuum carburizing (Fig. 14) revealed a tempered martensite structure with small amounts of retained austenite. Atmosphere carburized gears (Fig. 15) revealed the presence of large amounts of retained austenite (tip, mid-radius).
![]() |
![]() |
![]() |
Figure 9 – Sample C Before HT | Figure 10 – Sample C After HT (LPC + HPGQ) | Figure 11 – Sample C After HT (LPC + HPGQ) |
Test Conclusions
The following are the principle results of these trials:
1. High pressure gas quenching produced more consistent dimensional repeatability than oil quenching on the gear geometries in this study.
a. This degree of predictable movement could be anticipated in the pre-heat treatment manufacturing process thus avoiding significant post heat treatment grinding.
2. Gear charts indicated an average movement of 0.08 mm (0.003”).
a. The involute form remained intact after high pressure gas quenching as did the lead on the gear teeth and splines.
![]() |
![]() |
Figure 12 – Sample C After HT (LPC + HPGQ) | Figure 13 – Sample C After HT (LPC + HPGQ) |
3. Low pressure vacuum carburizing in combination with high pressure gas quenching allowed for the replacement of atmosphere carburizing and plug quenching on the gears investigated in this study.
a. The depth of high hardness (> 58 HRC) was greatest in the low-pressure vacuum carburized samples.
b. The root-to-pitch line case depth ratio in vacuum carburizing (93%) exceeded that of atmosphere carburizing 63%).
c. Levels of retained austenite were higher in the atmosphere-carburized samples.
![]() |
![]() |
Figure No. 14 – Clutch Gear “C”, Gear Tooth Mid-Radius LPC + HPGQ (1250X, 2% Nital) | Figure No. 15f – Clutch Gear “C”, Gear Tooth Mid-Radius AC + OQ (1250X, 2% Nital) |
References
1. Herring, Daniel H., Vacuum Heat Treatment, BNP Media, 2012.
2. Herring, Daniel H., A Comparison of Atmosphere and Vacuum Carburizing Technology, Industrial Heating, January 2002.
3. Herring, Daniel H. and David J. Breuer, Gerald D. Lindell, Selecting the Best Carburizing Method for the Heat Treatment of Gears, AGMA Technical Conference Proceedings, 2002.
4. Otto, Frederick J. and Daniel H. Herring, Improvements in Dimensional Control of Heat Treated Gears, Gear Solutions, June 2008.
Daniel H. Herring / Tel: (630) 834-3017) /E-mail: dherring@heat-treat-doctor.com
Dan Herring is president of THE HERRING GROUP Inc., which specializes in consulting services (heat treatment and metallurgy) and technical services (industrial education/training and process/equipment assistance. He is also a research associate professor at the Illinois Institute of Technology/Thermal Processing Technology Center.