The most important materials used in man’s history have lent their names to the periods concerned, namely the stone, copper, bronze and iron ages. Although it would be an exaggeration to call modern times the ‘graphite age’, graphite has become an indispensable and reliable material for the manufacture of modern high-performance products made from metal and ceramics. Graphite-based composites, in particular, are gaining constantly in importance. In the high-temperature applications field, these composites include carbon fiber-reinforced carbon (C/C for carbon composites) and carbon fiber-reinforced silicon carbide (C/SiC), as well as rigid and flexible felts based on pitch or viscose fiber (Figure 1).Carbon fiber-reinforced carbons (C/C for short) are used in modern vacuum or protective gas furnaces in the form of heating elements or charging systems. They are characterized by thermal shock resistance, the absence of distortion, low mass and strength increase with rising temperature. These features enable users to operate their plants more effectively, minimize reject rates and therefore reduce the cost of production. CIC is thus a key element in many process optimization steps and helps companies to improve their competitiveness.
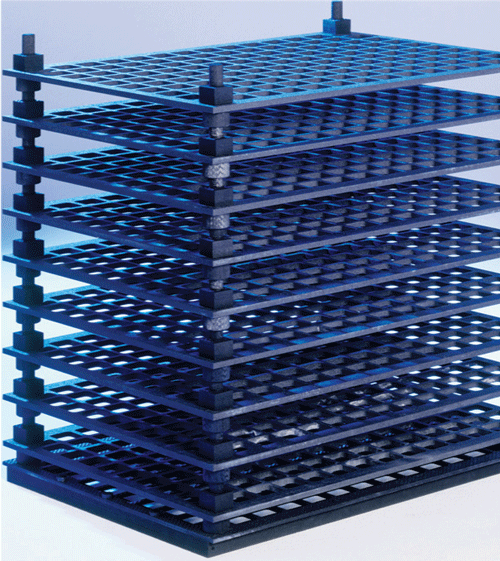
History and Manufacture Of C/C
Towards the end of the 19th century, carbon fibers based on pyrolyzed bamboo were used to manufacture incandescent filaments. In the 1950s, fibers with aligned crystalline structures were first produced in Great Britain. The starting materials now used for the production of carbon fibers are viscose (rayon), PAN (polyacrylonitrile) and pitch. Among these raw materials, the one with the poorest electrical and thermal conductivity is viscose. It is therefore often used as a thermal insulation material in the form of felts. Felts can be used up to a temperature of 2700°C. Pitch materials cost less than PAN, but the subsequent treatment required makes the pitch more expensive.
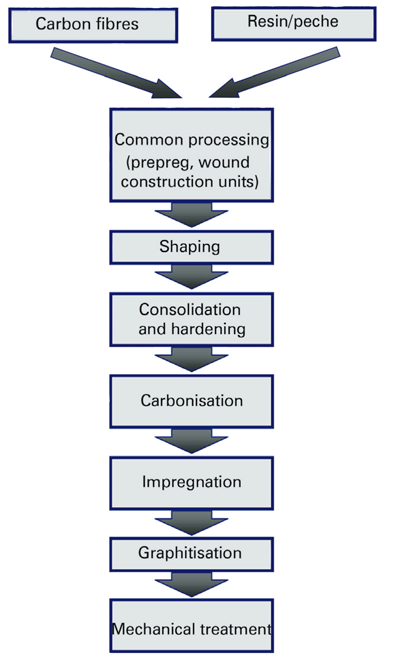
The starting material is first converted into a nonflammable intermediate product. The filament is then pyrolyzed, ie all elements except carbon are driven off by heat. The carbon content at 1000°C is around 94% by weight and depends on the preceding thermal treatment. In the process step performed above IS00°C and termed graphitization, the graphitized carbon layers are given their proper alignment.PAN fibers are distinguished by their tensile strength values. Typical examples are HT (High Tenacity) and UHM (Ultra-High Modulus) fibers. Another characteristic feature is the filament number, ie the number of individual fibers per fiber strand, otherwise known as a roving. A distinction is drawn between low filament fibers, which consist of up to 24000 filaments per roving, and heavy tow types, which include up to 400000 individual fibers.
Further processing into C/C requires the use of a carbon-containing matrix. Unlike carbon fiber-reinforced plastics (CFRP), C/C products are manufactured not with high-strength epoxy resins but with phenolic resins and various forms of the pitch to take advantage of their high carbon content. The range of possible C/C products includes not only filament-wound components such as tubes and crucibles but also plates and 3dimensionally shaped elements.
For plate manufacture, the fibers are processed into a woven fabric after graphitization and pre-impregnated with the resin to produce a so-called prepreg (Figure 2).
This prepreg is arranged in several layers in presses, where it is hardened at temperatures around 100°C. The polymer chains react with one another and bond the individual layers together to give a “green” material, whose plastic matrix is converted into carbon in a subsequent carbonization step (at around 1000°C). As this process has an adverse effect on the mechanical properties, such as mechanical strength and elongation at rupture, the coked material is subjected to several impregnation steps that are followed by carbonization until the desired parameters are obtained. A standard process includes three impregnation and three carbonization steps. Final graphitization at a standard temperature of 2000°C (to meet the customer’s service temperature requirements) yields the C/C end product with an ash content around 300-600ppm. The ash content can be cut to as low as 10ppm by working with a graphitization temperature of up to 2700°C. The highly graphitized composites obtained are typically used in semiconductor and nuclear applications.
Filament-wound components are produced by a similar process, in which the roving is impregnated with resin and wound around a mandrel, instead of being woven into a fabric. By varying the fiber angle, the mechanical and electrical properties of the component can be influenced as desired.
The filament-wound components are then hardened in hardening chambers. The subsequent carbonization, impregnation, and graphitization steps are analogous to those used in plate production.
‘Green’ production of hand-laminated shaped components differs from that of plates only in that prepreg strips are cut to size, laminated onto a negative mold, evacuated in a vacuum bag and then hardened in temperature-controlled pressure chambers known as autoclaves.
C/C to Enhance Furnace Productivity
As a general rule, graphite-containing components of any kind are designed only for vacuum or protective gas systems. Plates supplied to the sintering and hardening industries are used mainly as charging supports and heating elements (Figures 3 and 4). Tubes are employed chiefly as heating elements or matrices for hot isostatic presses. C/C strength values reach several hundred MPa at room temperature. C/C has what is known as hot flexural strength, ie other than with metal alloys, the material’s strength increases with rising temperature.
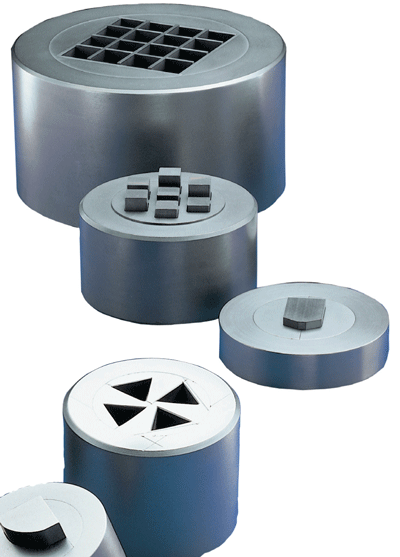
C/C materials are largely stress-free at high temperatures. As the materials cool down, stresses build up increasingly inside the materials and need to be considered as additional to the stresses acting on the materials from outside. The strength value at 2,000ºC may exceed that at room temperature by up to 40%. This beneficial property is particularly noticeable in charging systems. In temperature ranges where metal supports become soft and therefore need to be designed with greater thickness and solidity, the C/C material has higher flexural strength than at room temperature. This obviates the risk of charge support fracture. The higher strength values in the high-temperature range and the lower density of about 1.5g/cm2 bring six- to twelvefold weight savings compared with conventional heat-resistant steel systems. This means faster heating and quenching cycles with the same charge weights due to lower dead masses, or the option of treating a higher furnace charge at unchanged cycle times. Furnace productivity can be enhanced in either instance (Figure 5).
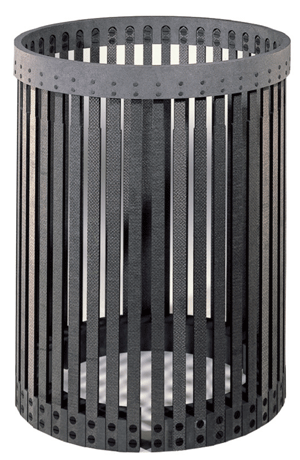
The superior resistance to temperature changes or thermal shock of up to 15,000 K is essential for the successful use of these materials in high-temperature applications. Thermal treatment operations which require the workpieces to be subsequently quenched with gas are no problem for C/C products. It is only oil quenching operations that cause the pores of the C/C material to fill with oil, which is then transferred to the furnace in the next furnace campaign. These pores account for some 15% of the component volume. Although the oil is coked in the furnace and increases the density of the charging tray as a result, it may contaminate the furnace atmosphere again. No hard and fast pronouncement can be made on whether or not this will adversely affect the process; a separate assessment is needed in each individual case.
The charging tray can be coated with silicon carbide to prevent it from absorbing the quenching oil. Although such components known as C/SiC components are still under development, they could become a useful alternative to steel structures in future oil-quenching operations. A simpler solution would be to coat the structure with SiC, but this would not be a permanent solution owing to the differences in the expansion coefficients of C/C and SiC.
Another general requirement is the material’s dynamic strength, which reflects the extent to which a material’s strength changes during its life cycle. C/C is very resistant in this respect because its initial strength declines only by some 5% after 1 million load alternations.
Another feature that deserves special mention is the C/C’s absence of distortion. Whereas metal structures need to be constructed from a solid material and reshaped with a hammer or similar tools after some months in operation, the C/C material has absolutely no tendency to distort. This makes the material highly suitable for use in automated processes, for instance. Robots programmed to return repeatedly to a particular position will always find the C/C charging system in its proper place (Figure 6).
The absence of any tendency to distort also has a favorable effect on the reproducibility of components, as these are always placed in the same furnace position and prevented from falling down. This helps to significantly reduce furnace downtimes and the costs associated with poor component quality.
Limits to the Use Of C/C
Despite its wide range of benefits offered, C/C is also subject to certain application-related restrictions. The main drawback – as with any other graphite-containing material- is its poor oxidation resistance. As mentioned above, the raw material fibers are converted into non-flammable intermediate products. However, the C/C material still wears away or oxidizes at temperatures from around 350°C to 450°C and above when exposed to oxygen. The oxidation rate depends mainly on the partial pressure of 02.
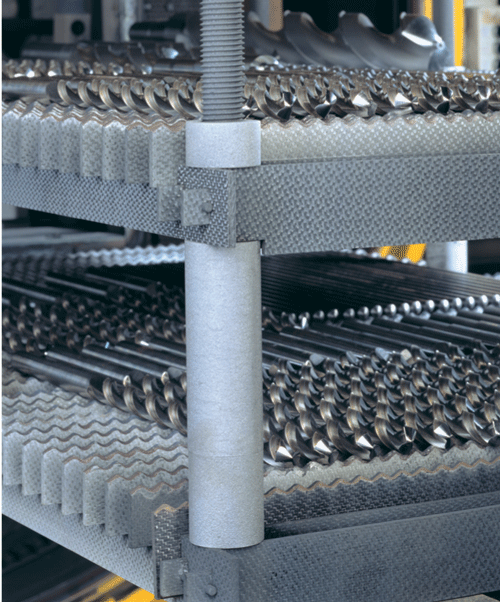
Other influencing parameters typically include the material’s porosity and the moisture level of the gas used. At around 700°C and above, the water reacts with the carbon to form carbon monoxide and hydrogen. This effect is further enhanced at higher temperatures, as hydrogen reacts with carbon to form methane at around 1200°C or above. This hydrogen-carbon reaction even occurs at as Iowa temperature as 500°C if materials with a nickel content are employed and act as catalyzers.
A familiar problem encountered is carburization, which occurs at around 1050°C or above when the metal component comes into contact with the graphite support. This reaction may be prevented by using a separating layer, typically containing aluminum oxide and supplied in the form of paper, felt, tiles or spray.
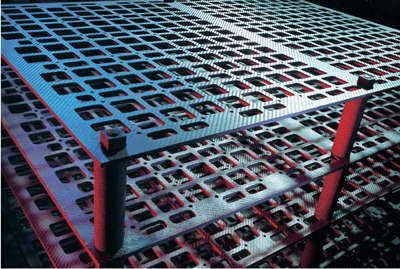
In Summary
The high global demand for carbon fibers and the products made from them, together with the shortage occurring on the world market, shows that this material is nowadays indispensable. Carbon fibers are used mainly in low-temperature applications such as aircraft construction, military equipment, and wind farms.
Global demand for C/C products used in high-temperature applications is also rising constantly. The reason is that investments in new furnaces are not being made until the existing equipment has been better utilized. This practice is being adopted in order to reduce production costs, improve product quality and hence safeguard workplaces over the medium term.