Today, tool steel heat treatment is based on a simple premise, that to obtain the optimum performance from any given grade, every step of the heat-treating process— including stress relief, preheating, austenitizing, quenching, deep freeze/cryogenic treatment and multiple tempers—must be done exactly correct. Absolute control of both process and equipment variability is one of many reasons why vacuum processing (Fig. 1) is popular in tool steel heat treatment [1].
The selection of any tool steel depends on a combination of factors including component design, application end-use and performance expectation. For any given application (Fig. 2) the goal of heat-treating is to develop the ideal microstructure to help achieve the proper balance of desired properties (Table 1) namely hot (red) hardness, wear resistance, deep hardening and/or toughness.
![Table 1 [2] Effect of Tool Steel Alloying Elements on Properties.](https://vacaero.com/wp-content/uploads/2012/03/table-1_lg.gif)
Notes:
[a] Distortion is best managed by additions of Mo (with Cr), Cr, and Mn;
[b] Tool must be austenitized at a high enough temperature to dissolve the vanadium carbide;
[c] Toughness is achieved via grain refinement.
Carbide Influence [3]
As we know, tool steels are alloyed with different types of carbide forming elements (e.g. vanadium, tungsten, molybdenum, and chromium) and in some alloys, cobalt. The addition of alloying elements serves two basic purposes: (a) to improve hardenability and (b) to provide harder and thermally stable carbides.
Carbides contribute to the strengthening of tool steels in two different ways:
- Carbides provide resistance to (abrasive) wear given that alloy carbides are significantly harder than the matrix material;
- Carbides contribute to higher yield strengths by impeding the mobility of matrix dislocations.
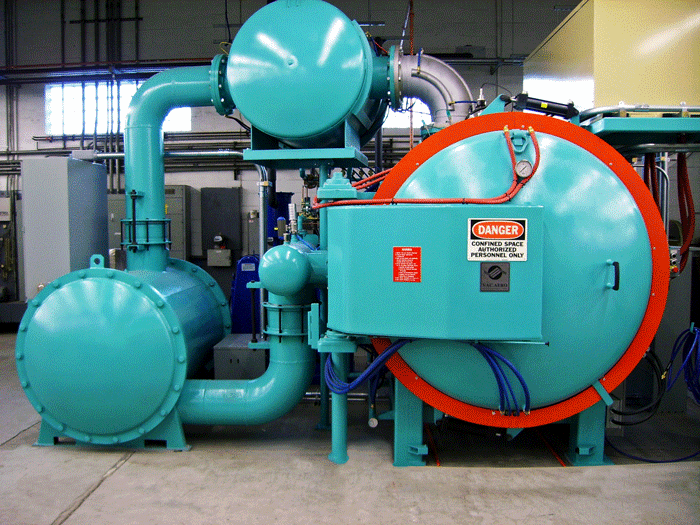
Carbide-forming elements are, in general, substitutionally dissolved in the crystal lattice (i.e. ferrite or austenite). In other words, when atoms are relatively similar in size, the atom exchange method is by direct exchange (i.e. substitution). Thus these elements tend to cause local lattice distortions (since their atomic radii are different from that of iron). However, the total strain is minimized so that less total lattice distortion results. Hence, there is a driving force for diffusion of alloying elements to these sites [4].
The diffusion of substitutionally dissolved elements is temperature-dependent. At temperatures above approximately 500°C (930°F), which is lower than the typical tempering temperatures for most tool steels, the diffusion of alloying elements becomes significant, and they will start to develop carbides [5]. The effect of precipitation of alloy-carbides is evident, especially in high-speed steels, where precipitation of fine and ultra-fine alloy carbides starting at approximately 550°C (1020°F) is responsible for the secondary hardening effect giving these steels excellent red hardness [6].
However, even in alloys that contain a relatively large amount of strong carbide forming elements, MC type carbides do not form below approximately 300°C (570°F) [5].
It is also noteworthy that alloy carbide grows at the expense of cementite (Fe3C→alloy carbide) either in-situ by nucleation at cementite/ferrite interfaces followed by growth or, from the dissolution of cementite, by separate nucleation and growth at favorable lattice locations.
Finally, caution should be observed in that although carbides are beneficial in tool steels for a number of reasons (e.g. strength and wear resistance) they are also likely crack initiation sites in instances where high application stress is involved.
Carbide Characteristics
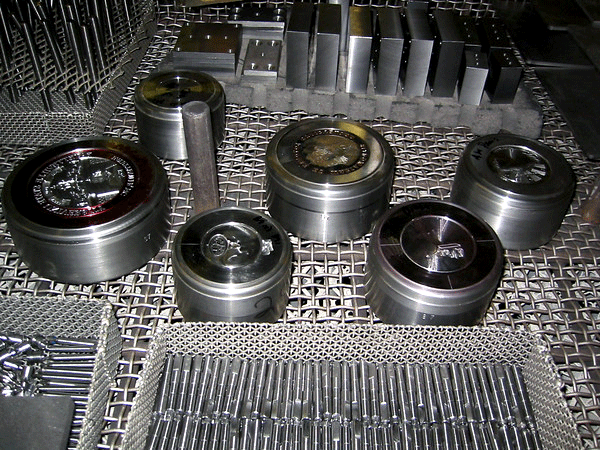
Tungsten and Molybdenum Carbides
Tungsten (W) promotes the formation of M6C type carbides [7] where the metal (M) is tungsten, iron (Fe), molybdenum (Mo) or a combination. These carbides dissolve in the austenite matrix at temperatures ranging from approximately 1150°C (2100°F) to the solidus temperature. However, in practice they do not dissolve completely since the time at austenitizing temperature is typically only a matter of a few minutes.
Molybdenum (Mo) promotes the formation of M2C type carbides [7]. These carbides become unstable at elevated temperatures, and at approximately 750°C (1380°F) they transform to M6C type carbides by reaction with iron [7], [8].
The addition of both tungsten and molybdenum typically results in grain refinement [9]. The fraction of Mo and W bounded as carbides tie up carbon and improve hardenability (by raising Ms and Mf temperatures). The fraction of tungsten and molybdenum in solid solution slows down pearlite and bainite nucleation and growth.
Vanadium Carbides
Vanadium (V) forms very hard and thermally stable MC type carbides (typically M2C) as isolated particles. These carbides improve resistance to abrasive wear and excellent cutting performance [7], [9], [10].
Vanadium carbides have highly limited solubility in the lattice matrix, hence the addition of vanadium will not delay the rate of diffusional decomposition of austenite but raises the Ms and Mf temperature by binding carbon (i.e. forming carbides), thereby improving the hardenability. Adding vanadium also results in grain refinement of the matrix [9].
Chromium Carbides
In tool steels chromium will form carbides typically type Cr23C6 and in some instances Cr7C3 during annealing depending on the chromium content. These carbides dissolve during austenization at temperatures exceeding approximately 900°C (1650°F) and are totally dissolved at approximately 1100°C (2012°F) [10].
Cobalt Carbides
Cobalt raises the temperature at which martensite transformation begins and is complete. Cobalt is the only alloying element in high-speed steels, for example, which can appreciably increase the thermal stability up to approximately 650°C (1200°F) and secondary hardness up to 67- 70 HRC [8], at the expense of toughness and wear resistance [9].
The addition of cobalt also causes the solidus temperature to rise. During austenization it is possible to dissolve a larger percentage of cobalt carbides thus enhancing hardenability. The high austenization temperature results in a relatively large amount of retained austenite after quenching, but this effect is somewhat compensated for by a lower stability of the austenite owing to the presence of cobalt [10], [11].
Tempering of High-Speed Steels [12]
During the heating portion of the tempering cycle plain, medium and high carbon steels experience three (3) principal transformation stages (Table 2), namely precipitation of eta (η) carbides, transformation of retained austenite into lower bainite, and precipitation of cementite. In tool steels containing secondary alloying elements (e.g. V, Mo, W), a fourth transformation is said to occur, namely precipitation of MC and MC type alloy carbides, that nucleate independently [15 – 18].
During this first transformation stage metastable carbide (Fe2,4C) having a hexagonal crystal structure, precipitates from the supersaturated martensite [19, 20].
![Table 2 [13] Stages of Tempering](https://vacaero.com/wp-content/uploads/2012/03/table-2-2_lg.gif)
Notes:
[a] The precipitation of finely dispersed alloy carbides responsible for secondary hardening (in highly alloyed steels) is sometimes referred to as the fourth stage of tempering.
Precipitation of these highly dispersed carbides is reported to enhance strengthening in these steels. However, low carbon martensite causes only a modest drop in strength and hardness of steel tempered in that temperature range [16, 18].
During the second stage, a non-homogeneous mixture of supersaturated ferrite and cementite (i.e. lower bainite) forms. It should be noted that this transformation occurs only in steels containing more than 0.3% C (because the amount of the austenite remaining in the steel after quenching strongly depends on carbon content [15, 16, 18]).
Cementite is formed during the third stage resulting in further lowering of the carbon content of the matrix and dissolution of metastable carbides allowing for recovery to occur [18, 19].
Above approximately 400°C (750°F), diffusion of alloying elements (e.g. V, Mo, W) begins and the cementite gradually dissolves and nucleation of MC and M2C carbides is possible. This leads to an increase of hardness of tempered steel and is referred to as secondary hardening.
Concluding Thoughts
Understanding the role of carbides and carbide dissolution in tool steels is important to ensure that optimal metallurgical characteristics are achieved so that optimum tool performance results.
Daniel H. Herring / Tel: (630) 834-3017) /E-mail: dherring (at) heat-treat-doctor.com
Dan Herring is president of THE HERRING GROUP Inc., which specializes in consulting services (heat treatment and metallurgy) and technical services (industrial education/training and process/equipment assistance. He is also a research associate professor at the Illinois Institute of Technology/Thermal Processing Technology Center.
References
- Herring, Daniel H., Frequently Asked Questions About Tool Steel Heat Treating, Industrial Heating, July 2010.
- Herring Daniel and Patrick McKenna, Vacuum Heat Treating of Tool Steels, Moldmaking Technology, May 2011.
- Hojerslev, Christain, Tool Steels, Riso National Laboratory, 2001.
- Porter, D. et al. Phase Transformations in Metals and Alloys, 2nd Edition, Chapman & Hall, 1992.
- Zackery, V. Decomposition of Austenite by Diffusional Processes, John Wiley and Sons, 1962.
- Wilson, R. Metallurgy and Heat Treatment of Tool Steels, McGraw-Hill Book Company (UK) Limited, 1975.
- Pippels, E. et al. Microstructure and Nanochemistry of Carbide Precipitates in High-Speed Steel S 6-5-2-5, Materials Characterization 43:41-55 (99).
- Geller, Y. Tool Steels, Mir Publishers Moscow, 1978.
- Vogel, C. et al. Metallurgi for Ingeniører 6th Edition. 1993.
- Hoyle, G. High Speed Steels, Butterworths, 1988.
- Roberts, G. et al. Tool steels 5th edit, ASM International, 1998.
- Bala, P., and J. Pacyna, The Kinetics of Phase Transformations During Tempering in High-Speed Steels, Journal of Achievements in Materials and Manufacturing Engineering, Volume 23, Issue 2, August 2007.
- Krause, G., Steels: Heat Treatment and Processing Principles, ASM International, 1990.
- Herring, What Do We Really Know About Tempering?, Industrial Heating, July 2007.
- Honeycombe, R. W. K. and H. K. D. H. Bhadeshia, Steels. Microstructure and properties, 2nd ed. London, Edward Arnold, 1995.
- Sinha, A. K., Physical Metallurgy Handbook, The McGraw- Hill Companies Inc., 2003.
- Dobrzaski, L. A., W. Kasprzak, J. Mazurkiewicz, The Structure and Properties W-Mo-V-Co High-Speed Steel of the Type 11-2-2-5 After Heat Treatment, Proceedings of the 4th International Scientific Conference “Achivements in Mechanical and Materials Engineering” AMME’95, Gliwice-Wisa, 1995, 83-86 (in Polish).
- Blicharski, M., Steels, WNT, Warsaw, 2004 (in Polish).
- Taylor, K.A., G.B. Olson, M. Cohen and J.B. Vander Sande, Carbide Precipitation During Stage I Tempering of Fe-Ni-C Martensites, Metallurgical Transactions 20A/12 (1989) 2749-2766.