
Vacuum deposition is a generic term used to describe a type of surface engineering treatment used to deposit layers of material onto a substrate. The types of coatings include metals (e.g., cadmium, chromium, copper, nickel, titanium) and nonmetals (e.g., ceramic matrix composites of carbon/carbon, carbon/silicon carbide, etc.), deposited in thin layers (i.e. atom by atom or molecule by molecule) on the surface (Fig. 1).
Vapor deposition technologies include processes that put materials into a vapor state via condensation, chemical reaction, or conversion. When the vapor phase is produced by condensation from a liquid or solid source, the process is called physical vapor deposition (PVD). When produced from a chemical reaction, the process is known as chemical vapor deposition (CVD).
These processes are typically conducted in a vacuum environment with or without the use of plasma (i.e., ionized gas from which particles can be extracted), which adds kinetic energy to the surface (rather than thermal energy) and allows for reduced processing temperature. The vacuum environment has the following advantages:
- Reducing the particle density so that the mean free path for collision is long
- Reducing the particle density of undesirable atoms and molecules (contaminants)
- Providing a low pressure plasma environment
- Providing a means for controlling gas and vapor composition
- Providing a means for mass flow control into the processing chamber.
Vapor deposition processes add energy and material onto the surface only, keeping the bulk of the object relatively cool and unchanged. As a result, surface properties are modified typically without significant changes to the underlying microstructure of the substrate.
Physical Vapor Deposition 3,4
Physical vapor deposition (Fig. 2) is a thin film method in which a coating is deposited over the entire object rather than in certain areas. All reactive PVD hard coating processes combine:
- A method for depositing the metal
- An active gas such as nitrogen, oxygen, or methane
- Plasma bombardment of the substrate to ensure a dense, hard coating
The primary PVD methods are ion plating, ion implantation, sputtering, and laser surface alloying. The production of metals and plasma differs in each of these methods. The gasified material condenses on the substrate material to create the desired layer. As such, there are no chemical reactions that take place in the process.
Ion plating (via plasma)
Plasma-based ion plating is used to deposit metals such as titanium, aluminum, copper, gold, and palladium on the surface of a component part. The coatings typically range from 0.008 – 0.025 mm. Advantages include adhesion, surface finish, in-situ cleaning of the substrate prior to film deposition and the tailoring of film properties (e.g., morphology, density, and residual film stress). Disadvantages include the need for tightly controlled processing parameters, potential contamination activated in the plasma, and potential contamination of bombarded gas species into the substrate and coating.
Typical applications include X-ray tubes, piping threads used in chemical environments, aircraft engine turbine blades, steel drill bits, gear teeth, high-tolerance injection molds, aluminum vacuum-sealing flanges, decorative coatings and for corrosion protection in nuclear reactors. In addition, ion plating is widely used as an alternative to cadmium for applying corrosion-resistant aluminum coatings.
Ion implantation
Ion implantation does not produce a discrete coating; rather, the process alters the elemental chemical composition of the existing surface of the substrate by alloying. Nitrogen, for example is used to increase the wear resistance of metals. Cleaning is critical to the success of this technology. Pretreatment (e.g., degrease, rinse, and ultrasonically clean) of the substrate to remove any surface contaminants prior to implantation is critical to success. The process is performed at room temperature. Deposition time depends on the temperature resistance of the workpiece and the required dose.
Ion implantation can use any element that can be vaporized and ionized in a vacuum chamber. The benefits of this process include reproducibility, elimination of post-treatment, and minimal waste generation. Ion implantation does not produce a stable finish if the coating is exposed to high temperatures. The technology is limited by a lack of familiarity, scarcity of equipment, and the need for strict quality control.
Ion implantation is used primarily as an anti-wear treatment for components of high value such as biomedical devices (e.g., prostheses), tools (e.g., molds, dies, punches, cutting tools, and inserts), and gears and balls used in the aerospace industry. Other industrial applications include depositing gold, ceramics, and other materials into plastic, ceramic, and silicon and gallium arsenide substrates for the semiconductor industry.
Sputtering and Sputter Deposition
Sputtering is an etching process that alters the physical properties of a surface. In this process, a gas plasma discharge is set up between two electrodes: a cathode plating material and an anode substrate. The deposits are thin, ranging from 0.00005 – 0.01 mm. Chromium, titanium, aluminum, copper, molybdenum, tungsten, gold, and silver are typical deposits.
Sputter-deposited films are used routinely in decorative applications such as watchbands, eyeglasses, and jewelry. The electronics industry relies on heavily sputtered coatings and films (e.g., thin film wiring on chips and recording heads as well as magnetic and magneto-optic recording media). Companies also use sputter deposition to produce reflective films for large pieces of architectural glass and decorative films for plastic used in the automotive industry. The food packaging industry uses sputtering to produce thin plastic films for packaging. Compared to other deposition processes, sputter deposition is relatively inexpensive.
Cladding
Surface alloying (modification) by use of lasers promotes alloying by injecting another material into the melt pool that alloys into the melt layer. Surface characteristics of this technology include high-temperature performance, wear resistance, improved corrosion resistance, better mechanical properties, and enhanced appearance
One of many methods of laser surface alloying is laser cladding. The overall goal of laser cladding is to selectively coat a defined area. In laser cladding, a thin layer of metal (or powder metal) is bonded with a base metal via a combination of heat and pressure. Moving the substrate under the beam and overlapping deposition tracks can cover large areas. Pretreatment is not critical, although the surface might require roughening prior to deposition. After coating, grinding and/or polishing are typically performed.
Laser cladding can apply most of the same materials as thermal spraying technologies. Materials that are easily oxidized are difficult to deposit without using inert gas streams and envelopes. Deposition rates depend on laser power, power feed rates, and traverse speed. Coating thicknesses can range from several hundred microns to several millimeters. If the density is too high, however, cracking and delamination can occur as is the case with aluminum and some steels. This technology also is unable to coat areas that are out of the line of sight.
Chemical Vapor Deposition
In CVD processes, a chemical reactant gas mixture comes in contact with the substrate and is then deposited into it. The coating is delivered by what is known in the technology as a precursor which when heated creates a reactive vapor. The form of the precursor can be a gas, liquid, or solid form. Gases are fed to the chamber under normal pressures and temperatures while solids and liquids require high temperatures and/or low pressures.
The process of decomposition can be assisted or accelerated via the use of heat, plasma, or other processes. Chemical vapor deposition includes sputtering, ion plating, plasma-enhanced CVD, low-pressure CVD, laser-enhanced CVD, active reactive evaporation, ion beam, laser evaporation, and other variations. These processes generally differ in the means by which chemical reactions are initiated and are typically classified by operating pressure.
- Ultrahigh vacuum typically below 10−6 Pa (~10−8 Torr)
- Low-pressure at sub-atmospheric pressures. (Note: reduced pressures tend to reduce unwanted gas-phase reactions and improve film uniformity)
- Atmospheric pressure
Once in the chamber, energy is applied to the substrate to facilitate the coatings reaction with the carrier gas. The basic steps in the CVD processes are:
- Formation of the reactive gas mixture
- Mass transport of the reactant gas through a boundary layer to the substrate
- Adsorption of the reactants on the substrate
- Reaction of the adsorbents to form the deposit
Pretreatment of the substrate involves mechanical and/or chemical cleaning (e.g., ultrasonic cleaning and/or vapor degreasing) followed in some instances by vapor honing (to improve adhesion). In addition, the deposition reactor chamber must be clean, leak-tight, and free of dust and moisture.
CVD is used for corrosion and wear resistance and applied to materials to obtain specific properties that are difficult to obtain with other processes. The most commonly used metals in CVD coatings are nickel, tungsten, chromium, and titanium carbide.
The majority of applications are in electronics optical, opto-electrical, photovoltaic, and chemical industries. CVD is used to deposit coatings and to form foils, powders, composite materials, free-standing bodies, spherical particles, filaments, and whiskers.
Titanium Nitride and Titanium Carbonitride Coatings
Titanium nitride (TiN) and titanium carbonitride (TiCN) coatings are applied to a variety of cutting tools and other products to help extend their service life and to provide a wear resistant coating (Fig. 4)
Process Basics. Titanium nitride (TiN) coatings can be applied using either PVD or CVD methods. For high-speed steel applications, PVD processes are normally preferred. PVD processes, however, have certain limitations with respect to component geometry, the need for workpiece rotation to achieve uniformity and coating temperatures (for certain materials).
CVD processing temperatures are typically between 850 – 1100°C (1550 – 2000ºF). The basic chemical reaction (Equation 1) in the CVD coating to produce a layer of TiN is between titanium tetrachloride (TiCl4), nitrogen (N) and hydrogen (H):
(1) 2TiC14 + N2 + 4H2 → 2TiN + 8HC1
By contrast, PVD processes operate at much lower temperatures, in the range of between 400 – 600°C (750 – 1100ºF) or lower. PVD processes rely on ion bombardment instead of high temperatures (as is the case of CVD) as the driving force. The substrate to be coated is placed in a vacuum chamber and is heated to temperature. The Ti coating material is vaporized and a reactive gas such as N2 is introduced and ionized; the vaporized titanium atoms then react with the ionized nitrogen to form TiN compound that deposits on the substrate to form the coating. There are three major PVD processes for coating tools: evaporating, sputtering and reactive ion plating, differing primarily in the way the reacting metal is vaporized.
Titanium carbonitride (TiCN) coatings offer slightly higher hardness compared to TiN coatings and can show a slightly lower friction coefficient in many applications. They are primarily used to achieve enhanced abrasive wear resistance. TiCN coatings have a lower limit for service temperature.
PVD is widely used for high speed and tool steels since CVD process temperatures fall into the range where certain tool steels are hardened. Post-coating treatments (re-hardening and re-tempering) may be required. These treatments may affect coating adhesion and dimensions.
A key area of consideration for the selection process is the end use application temperature of the component that is to be coated. The higher the usage temperature, the more CVD coating methods may be desirable.
Properties
The mechanical and physical properties (Table 1) produced by TiN coatings are similar to those of other common coatings. The advantage of TiN coatings on high speed and other tool steels include:
- Appearance
- Adhesion to substrate
- High chemical inertness
- Resistance to elevated temperatures
- Hard (2400 HV) surfaces to reduce abrasive wear
- Low coefficient of friction
- Increased lubricity
- Surface roughness
- Low dimensional change
- High temperature stability
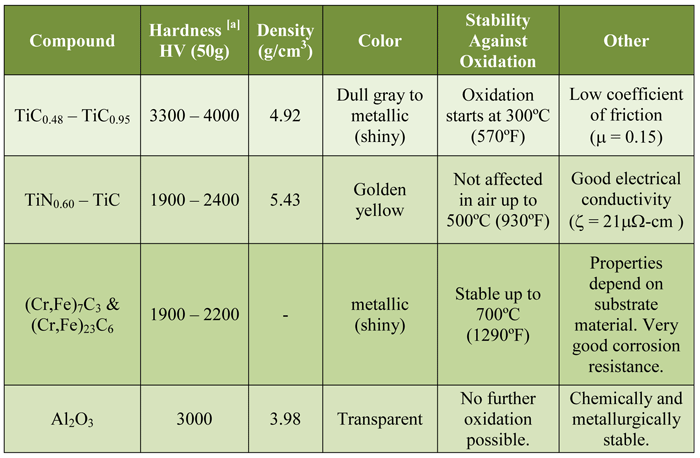
Notes: [a] 2500 HV (50g) ≈ 85 HRC
The benefits of TiCN coatings include:
- Harder than TiN
- Harder than carbide
- Harder than chromium (3 times)
- Abrasion resistance
- Strong adhesive molecular bond to substrate
- Broad range of substrates
- Thin film (typically 3μm)
- Uniform coating with no buildup on edges
- Follows surface texture of the part
- Grayish metal appearance
- Non-toxic (environmentally friendly)
Summary
Vacuum deposition methods such as PVD and CVD processes represent an important set of applications for vacuum technology. While often associated with niche markets, the technology has been found to enhance performance in a surprising number of applications and as such needs to be better understood by the heat treating community.
References
- Herring, Daniel H., Vacuum Heat Treatment, BNP Media Group, 2012.
- Herring, Daniel H., Atmosphere Heat Treatment, Volume I, BNP Media Group, 2014.
- “Alternative Methods for Metal Finishing”, Metal Finishing Industry, Illinois Sustainable Technology Center, University of Illinois (www.istc.illinois.edu)
- “Differences Between CVD and PVD”, Differences.com (www.differences.com)
- Bunshah, Rointan F., Handbook of Deposition Technologies for Films and Coatings, Noyes Publications, 1994.
- Wikipedia (https://en.wikipedia.org)
- Porat, R. and Y. Cassuto, “A Comparison Between CVD and PVD Coated Cemented Carbide Cutting Tools” Journal de Physique Colloques, 1989, 50 (C5), pp.C5-803-C5- 810.
Daniel H. Herring / Tel: (630) 834-3017) /E-mail: dherring@heat-treat-doctor.com
Dan Herring is president of THE HERRING GROUP Inc., which specializes in consulting services (heat treatment and metallurgy) and technical services (industrial education/training and process/equipment assistance. He is also a research associate professor at the Illinois Institute of Technology/Thermal Processing Technology Center.