Vacuum furnaces (Fig. 1) can use a variety of different gases during the processing cycle in partial pressure operation, for backfilling to atmospheric pressure at the end of the processing cycle and for cooling/quenching. The most common of these gases (in order of frequency of use) are nitrogen, argon, hydrogen, and helium (c.f. Table Nos. 1 – 4). Other common gases include various hydrocarbons and ammonia (for vacuum carburizing/carbonitriding) and specialty gases such as neon (for certain electronics applications).
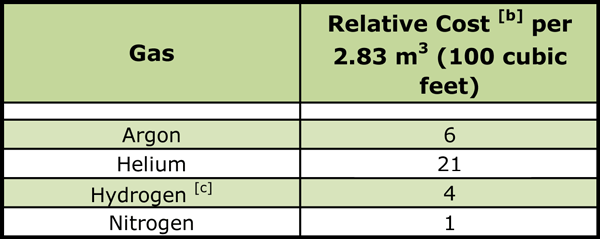
Notes:
[a] Based on a minimum usage of 2830 cubic meters (100,000 cubic feet) per month.
[b] All gases compared to nitrogen whose relative cost is unity.
[c] Based on liquid supply.
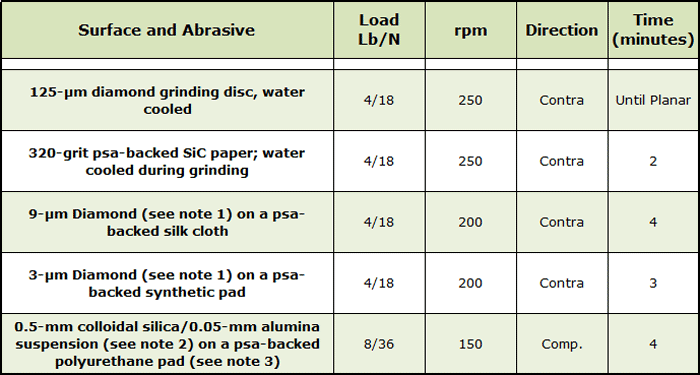
Notes:
1. Appropriate health and safety measures should be observed at all times. Contact your gas supplier for more details regarding safe handling and usage of any gases present in the plant.
2. Refer to the HAZARDS IDENTIFICATION section of the Material Safety Data Sheet (MSDS) for the gas in question.
3. The inert gases, for example, are all asphyxiants. Hydrogen is flammable and is also an asphyxiant. Gas pressure is also a potential concern.

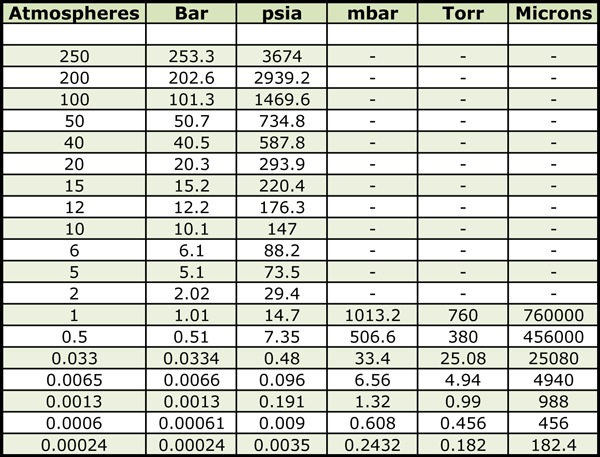
Nitrogen (N2)
In vacuum heat treatment nitrogen is used primarily for cooling/quenching, as a partial pressure gas and for backfilling to atmospheric pressure at the end of the heat treating cycle. A common misconception, however, is that nitrogen gas is a true inert gas. It is not and under the wrong circumstances, it can react with the surface of the material being heat treated with deleterious effects.
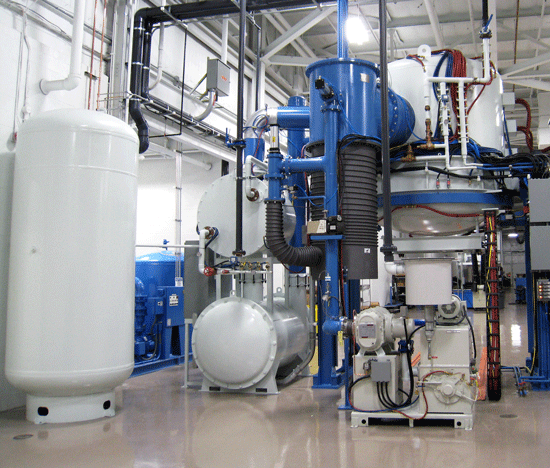
Nitrogen has a gaseous specific gravity of 0.967 and as such is slightly lighter than air (whose specific gravity is 1.0) and has a boiling point of -195°C (–320.5°F) at atmospheric pressure. It is colorless, odorless and tasteless. Commercially, nitrogen is produced by a variety of air separation processes, including cryogenic liquefaction and distillation, adsorption separation and membrane separation (Special note: membrane separation technology typically does not produce a gas with high enough purity for vacuum use).
Nitrogen used for most vacuum applications is supplied as industrial grade gas. The typical impurity levels are 10 ppm oxygen (maximum) and a minimum dewpoint of -68°C (-90°F) or lower (3.4 ppm by volume). The actual delivered values are typically in the 2 ppm range for both oxygen and water vapor. It is often the case that there is more “pick up” of impurities in the piping to the equipment than in the supply product itself, primarily from leaks. Other grades of nitrogen (including electronic grade) are also available.
Nitrogen is the most common backfill gas (Fig. 2) used in vacuum heat treatment due in large part to cost considerations and the fact that it is generally nonreactive nature with many materials. However, as a function of temperature, nitrogen is reactive to certain materials especially alloys containing chromium, molybdenum, and titanium. It is commonly used as a partial pressure gas in the range of 0.67 to 6.67 mbar (500 – 5000 microns) or in positive pressure convection heating where it has been found to be effective in reducing heat-up/cycle time. In most instances, it is not recycled.
Argon (Ar)
Argon is truly a chemically inert gas comprising slightly less than 1% of the air (by volume). Its specific gravity is 1.38 so it is heavier than air and its boiling point at atmospheric pressure is -185.9°C (–302.6°F). Argon is colorless, odorless, tasteless, noncorrosive, nonflammable and nontoxic. Commercial argon is the product of cryogenic air separation, where liquefaction and distillation processes are used to produce a low-purity crude argon product that is then purified to the commercial product.
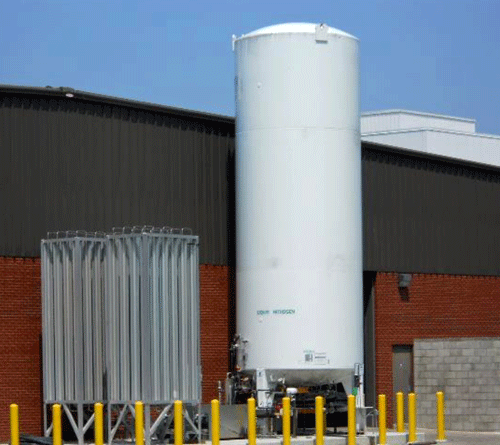
Argon is used primarily for its properties as an inert gas, especially where it is important to prevent hydrogen embrittlement in materials such as titanium, tantalum, niobium, and zirconium. Argon is used as a partial pressure gas in the range of 0.67 to 6.67 mbar (500 – 5000 microns) during brazing to minimize volatilization and as a purge or sweep gas (due to the large size of the argon molecule) such as double pump-down techniques used prior to the onset of heating.
Hydrogen (H)
Hydrogen is the lightest of all the gases having a specific gravity of 0.0695 and a boiling point of -252.8°C (–423°F) at atmospheric pressure. It’s a colorless, odorless, tasteless, flammable gas found at concentrations of about 0.0001% in air (by volume). Hydrogen is produced by several methods, including steam/methane reforming, dissociation of ammonia, electrolysis and recovery from by-product streams during chemical manufacturing and petroleum reforming. Hydrogen is stored and transported as either a gas or a cryogenic liquid.
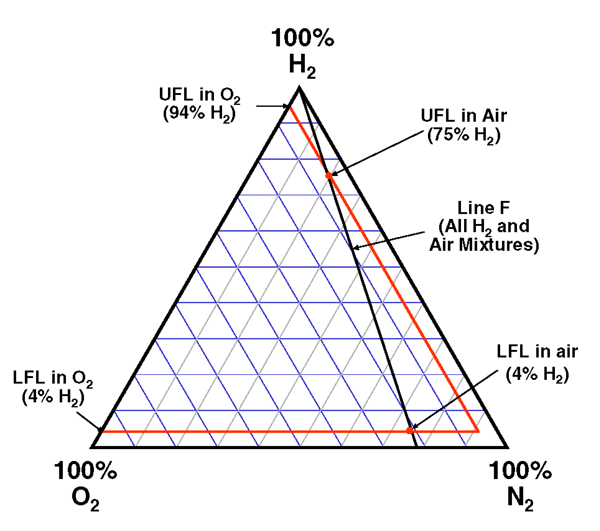
Hydrogen is used in heat-treating primarily for its properties as a reducing gas. Hydrogen is commonly used as a partial pressure gas in the range of 0.67 to 6.67 mbar (500 – 5000 microns) in many applications including brazing (e.g. oxide reduction), hydriding (e.g. titanium, tantalum), sintering and even during the heat-up portion of the cycle in low pressure vacuum carburizing where it acts as a scrubbing (reducing) agent and shortens heat up times. Another common use of hydrogen is for cleanup cycles, involving either the furnace or the baskets/grids/fixtures. Several companies report they are using hydrogen in overpressure (+0.5 psig) conditions for applications such as sintering of powder metal to aid in lubricant removal.
Hydrogen can also be used in high-pressure gas quenching systems due to its high heat transfer properties. However, there are safety concerns and special precautions must be observed (Special note: The use of hydrogen in any type of furnace can be extremely dangerous. The Original Equipment Manufacturer (OEM) should be consulted and the end user must comply with all appropriate federal, state, local and company codes, rules and regulations prior to attempting to do so (e.g. NFPA 86, latest edition). See Reference 1 for additional details on the use of hydrogen in vacuum heat treatment).
A full tertiary diagram (Fig. 3) for hydrogen, oxygen, and nitrogen includes the flammability envelope for ambient conditions. Mixtures inside the envelope are flammable. Temperature corrections (Fig. 4) have been determined, assuming oxygen is the contaminant. Finally, some metals (e.g. titanium, tantalum) have adverse embrittlement reactions in the presence of hydrogen.
Helium (He)
Helium is also chemically inert and is the second-lightest gas (behind hydrogen). Helium has a specific gravity of 0.138. It’s a colorless, odorless, tasteless gas with a boiling point is -268.9°C (–452.1°F) at atmospheric pressure. Helium is present in the air at a concentration of only 0.0005% (by volume). The principal supply source is natural gas deposits where the crude helium is extracted from the natural gas stream and then purified. Helium can be stored and shipped either as a compressed gas or cryogenic liquid.
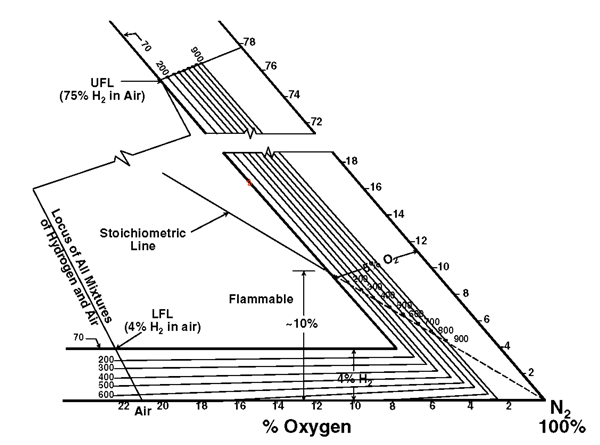
Helium is used primarily for its properties as an inert gas. Due to cost, helium must be recycled. The components of a helium gas recovery system include:
- Low-Pressure Blower
- Low-Pressure Storage
- Recompression
- High-Pressure Storage
- Filtration
- Purification
- Gas Analysis
- Interface with Vacuum Furnace Gas Supply
Helium is used in high-pressure gas quenching for its heat transfer properties in the range of 2 – 20 bar to increase the cooling rate of a load during quenching. In some steels this allows proper transformation to take place. In others, such as is the case of very large thick parts or very dense loads, it allows for shorter overall cycle times.
Hydrocarbons
Various hydrocarbon gases such as acetylene (C2H2), cyclohexane (C6H12), ethylene (C2H4), methane (CH4), propane C3H8) and propylene (C3H6) are used as a carbon source in processes such as low-pressure vacuum carburizing and carbonitriding (in combination with ammonia, NH3) or plasma carburizing/nitriding. All are flammable and most have a detectable odor.
Specialty Gases
Gas mixtures can be used for high gas pressure quenching. These include:
1. Nitrogen / Hydrogen
One of the methods used by the heat-treating industry to increase the cooling rate (i.e. heat transfer coefficient) of nitrogen is to add a small percentage of hydrogen into the gas. Typically 3% hydrogen is added to ensure that the mixture is noncombustible but up to 12% hydrogen has been reportedly used (with appropriate safety precautions) to enhance the results with marginal materials. For example, vacuum carburized SAE 8620 can be gas pressure quenched at lower pressures (depending on part section thickness) in nitrogen/hydrogen mixtures to achieve results equivalent to those produced by oil quenching or higher nitrogen gas pressures (e.g. case hardness, surface and core hardness, microstructure).
![Table 5 6 - Electrical Costs Using Different Backfill Gases Notes: [a] Based on a utility cost of $0.10 per KWH.](https://vacaero.com/wp-content/uploads/2013/12/table-5_lg.gif)
2. Argon/Helium or Argon/Hydrogen
The cooling properties of argon can be enhanced by the addition of either helium or hydrogen. Mixtures of argon and helium in the range from 50% helium /50% argon to 95% helium/5% argon have been used to enhance cooling rates as a function of pressure and material. Mixtures in the range of 10% hydrogen/90% argon to 40% hydrogen/60% argon have been reported to improve the hardness of marginal materials. Again, all appropriate safety precautions must be observed. An added benefit to using either helium or hydrogen gas mixtures is that less powerful quench fans are required (due to decreased gas density) and less power is consumed (Table 5).
Summing Up
The choice of backfill or partial pressure gas for a particular vacuum furnace system remain important considerations from a metallurgical as well as fiscal standpoint. Properly sized, installed and leak tested backfill gas piping and surge (accumulator) tanks are recommended for proper system integrity and performance.
References
- Herring, Daniel H., Vacuum Heat Treatment, BNP Media Group II, 2012.
- Mr. Don Bowe, Ask The Experts, Air Products and Chemicals, Inc. (www.airproducts.com), private correspondence.
- Linde (www.lindeus.com)
- Mr. Trevor Jones, Solar Atmospheres (www.solaratm.com), private correspondence.
- Dwyer Jr., John, James G. Hansel, and Tom Philips, Temperature Influence on the Flammability Limits of Heat Treating Atmospheres, Air Products and Chemicals, Inc., 2003.
- Mr. Robert Hill, Solar Atmospheres (www.solaratm.com)
- Airgas (www.airgas.com)