A manufacturer of quartz products for the lighting industry was curious as to the origin of black “flakes” (particles) found on the outside and inside surfaces of their quartz tubes after heat treatment. These flakes appeared to be “fluffy bits of carbon”. The thought process to investigate this phenomenon presents a unique learning experience for us all.
Background
One of the last steps of the quartz-production process is the heat treatment of the quartz tubes, which takes place in one of several vacuum furnaces at this manufacturer’s facility. The quartz tubes are heated under vacuum to 1050°C (1220°F) and held at temperature for several hours. This is followed by a quench with nitrogen.
The vacuum furnaces in question have graphite heating elements, a combination ceramic fiber/felt insulation pack with a molybdenum hot face and stainless steel cold face and a graphite hearth. The quartz tubes themselves are placed onto graphite fixtures (racks).
The black particle contamination varied in cross sectional area between 0.1 mm and 5 mm (0.004″ – 0.200″). The consistency of the contaminate is best described as “fluffy” and it tends to turn to powder when touched.
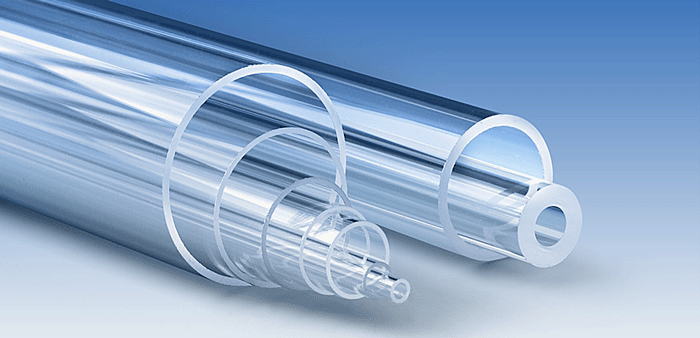
Investigation Questions & Answers
A series of questions were raised during the investigation (answers for which are shown in italics).
1. The source of the black (carbon) particles may likely be from one of the graphite sources present in the equipment or from the racks themselves. It would be worthwhile to investigate and determine the composition of each graphite source present as well as the condition of the graphite. The suggestion to “analyze” the graphite is not intended to determine the chemical composition, but rather to investigate the material properties (density, graphitization method, etc.) so as to determine if the materials of construction have a tendency to thermally decay or break down over time. It is important to pay particular attention to how these materials react with water as a function of temperature and time. There are numerous grades of graphite on the market and they do not all react the same, some may have a greater tendency to dust, react with contaminants in the vacuum environment and/or deteriorate faster over time.
The condition of the heating elements and internals show no signs of wear or decomposition. The beams and pins, which comprise the racks are subject to wear due to handling during load makeup and load disassembly. Some beams and pins may be 10 years old or even older. Some graphite will come off when the surface of the beams is contacted by the parts. This is also true with new graphite products.
2. What is the purity of the nitrogen? The gas supplier should be able to bring portable gas analysis equipment to your location or extract samples for analysis in their labs. It may be of value to pull samples of gas from the furnace during various steps in the process and have the composition analyzed.
After checking, the nitrogen was found to have less than 1 ppm (each) of water, hydrocarbon and oxygen. Carbon dioxide and carbon monoxide values were not determined.
3. Does the nitrogen tank or piping have internal contaminants that are being carried into the furnace or are the flakes the result of nitrogen impingement on the surface of the graphite present within the furnace causing particles to be released into the gas stream, then reacting during processing and ultimately wind up on the product. As far as the piping, it is a good idea to isolate the lines and perform a vacuum leak check on them.
The piping appears free of residue or contamination. The tank internal condition is not known.
4. The emphasis should be to look at equipment and process variables. Most important the vacuum level through the entire process cycle so as to make sure that the vacuum level is not so poor as to oxidize the hot zone or fixture and then decompose and redeposit onto the product.
The heating and evacuation program is as follows: After loading and closing the furnace it is evacuated from 1000 mbar (750 Torr) to 0.1 mbar (0.075 Torr). At this pressure the heating begins. After about three (3) hours the temperature is 1050°C (1922°F). The load is held at temperature and under vacuum until the water content drops within specifications. After this soak time, the heat is turned off and immediately quenched with nitrogen at a pressure of about 1000 mbar (75 Torr). At the end of the cycle, when the temperature reaches 50°C (120°F) the furnace is unloaded.
5. How clean are the quartz tubes coming into the process?
Before the parts are stacked onto the graphite rack, they are washed with a mixture of hydrochloric and hydrofluoric acids, thoroughly rinsed with demineralized water and dried with heated air (by blowing clean and heated air through them). The concentration of metals in the almost pure demineralized water is very low (in the range of 1 to 100 ppm).
6. Are the chamber cold walls oily either from dirty product or possibly oil back streaming of the pumps?
On two of the four furnaces, the cold wall of the chamber is oily. These furnaces have a combination of rotary vane pumps and Roots blowers in series.
7. The hot zone insulation should be checked, as it may be carbon rather than graphite and thus prone to “dusting”. If ceramic fiber, the material may be hydroscopic in nature (i.e. retain water) that is subsequently released at temperature. The life expectancy of internal graphite components can vary significantly with frequency of use and thermal duty cycle. In general, heating elements are replaced every 5 – 7 years and graphite racks about every 10 – 12 years. Have the components inside your furnaces reached or exceeded their normal life expectancy?
The insulation consists of ceramic felt/fiber with a molybdenum hot face. In the two older furnaces there are several cracks in the molybdenum.
8. Quartz is usually laden with water and will outgas heavily on heating in vacuum. Quartz has the ability to hold water inside its structure and release it all at once when the temperature reaches 950°C (1740°F). It is important that the water does not overwhelm the diffusion pump (greater than 50 microns) and cause back streaming. One way to prevent this is to slow the heating rate or run the entire cycle at 1 Torr in partial pressure nitrogen.
As it turns out, the water content of the quartz is about 150 ppm. Therefore, a 1000 kg (2200 lb.) load contains almost one bucket of water or about 10 liters (2.27 gallons). However, monitoring the pressure only revealed a minor amount of outgassing during heating.
9. What is the furnace leak rate?
The normal furnace leak rate is about less than 0.005 mbar liter/sec although 1- 2 times in the last several years the furnace has had problems holding this leak rate but repairs were performed at those times and the leak rate returned to normal values.
10. The presence of oil on the cold walls of the furnace could indeed be mixing with graphite deposits or decomposition of a hydrocarbon present. Ceramic fiber insulation is hydroscopic in nature further complicating the situation. The fact that a pressure rise on the temperature graph is not observed could indicate the water vapor is reacting with the graphite and forming carbon monoxide/carbon dioxide. There may be a partial carbon reversal reaction taking place during cooling (carbon monoxide decomposing to carbon dioxide and carbon in the form of soot) which can occur in the temperature range of 480°C – 705°C (900°F – 1300°F).
The furnace interior does indeed have an oily residue. The oily residue found near the furnace door was tested and found to be the same oil as used in mechanical vacuum pumps. A bake out cycle on the furnace was conducted but the problem did not go away.
Test Results
Using a simple Scotch Tape Test, “dirt” samples were collected from the “bottom” of the hot zone, the cold walls and from the lowest part of the inner door. These were looked at via an optical microscope and the following observations noted:
The flakes were found to consist of carbonaceous fibers in the size range of 0.05 mm – 0.5 mm (0.0020” – 0.020”), splinters of quartz in the range of 0.1- 0.5 mm (0.0040” – 0.020”), beads of quartz in the size range of 0.05 – 0.5 mm (0.0020” – 0.020”), graphite dust, graphite particles and small parts of vacuum paint from the inside of the vessel. Also, there were very small metallic appearing particles in the size range of 0.01- 0.03 mm (0.0004” – 0.0012”). The samples were also oily or greasy except the samples from the furnace running a dry pump (all other furnaces run mechanical (wet) pumps).
The flakes deposited on the quartz tubes were analyzed and found to contain carbon (c), oxygen (O), silicon (Si), aluminum (Al), calcium (Ca) and iron (Fe) with some molybdenum (Mo) and sulfur (S) present. Some flakes contained large amounts of Fe and/or Ni. The amount of Mo and S varied considerably.
The flakes deposited on the molybdenum shielding in the hot-zone were analyzed and found to consist of large percentages of carbon (c), silicon (Si), oxygen (O), and iron (Fe) with lesser amounts of magnesium (Mg), nickel (Ni) and chromium (Cr).
90% of the flakes were found to be magnetic.
Root Cause
The root cause of the contamination was determined to be the presence of quartz splinters, which were found to have originated during stacking of the tubes onto the racks. During processing, these splinters were circulated throughout the furnace by the incoming nitrogen quench gas, essentially blasting the surface of the graphite in the racks, creating both graphite dust and quartz dust which subsequently deposited onto the parts and the cold walls of the vacuum furnace. Some of these splinters formed beads due to exposure to elevated temperature. Metal dust and oils were also attracted to these particles which manifested themselves as “flakes” in the size range of 0.5 – 5 mm (0.020” – 0.200”) in diameter appearing on and between the quartz product as well as the bottom of the hot zone and in the lower part of the door.
Summing Up…
Problem solving is often a matter of asking a series of questions and making careful observations of the evidence. Such was the case here.
References
1. Godbeer, W. C., and R. W. T. Wilkins, The Water Content of Synthetic Quartz, American Mineralogist, 1977, Vol. 62, pp. 831 – 832.
Daniel H. Herring / Tel: (630) 834-3017) /E-mail: dherring@heat-treat-doctor.com
Dan Herring is president of THE HERRING GROUP Inc., which specializes in consulting services (heat treatment and metallurgy) and technical services (industrial education/training and process/equipment assistance. He is also a research associate professor at the Illinois Institute of Technology/Thermal Processing Technology Center.