When performing any type of vacuum heat treatment it is always important to be aware of the possibility of evaporation and/or sublimation of elements, which can be present in the material being processed, introduced into the vacuum system with the workload, inherent in the equipment design or introduced during maintenance, repair or rebuilds. In cases where evaporation may be a concern, the vaporization rate is of prime importance and is directly related to the furnace pressure (the higher the pressure, the more frequent the collision of gas molecules and correspondingly, the few metal atoms leave the metal’s surface).
What is Evaporation?
Vaporization is the process that occurs when a chemical or element is converted from a liquid (or a solid) to a gas. When a liquid is converted to a gas, the process is called evaporation or boiling; when a solid is converted to a gas, the process is called sublimation. The pressure exerted by the vapor of a liquid in a confined space is called its vapor pressure. As the temperature increases so too does its vapor pressure. Conversely, the vapor pressure decreases as the temperature decreases.
The vapor pressure differs for different substances at any given temperature, but each substance has a specific vapor pressure for each given temperature. At its boiling point the vapor pressure of a liquid is equal to atmospheric pressure. For example, the vapor pressure of water, measured in terms of the height of mercury in a barometer, is 4.58 mm at 0°C and 760 mm at 100°C (its boiling point).
All metals evaporate as a function of temperature (first order effect) and vacuum level (second order effect). Equation 1 allows us to determine the evaporation rate, Q, and shows us that the vapor pressure-temperature relationship is nearly logarithmic. The rate of evaporation is greatest in high vacuum conditions.
(1)
where
Qmax = evaporation rate (g/cm3-sec)
Pv = vapor pressure (torr)
T = temperature (°K)
M = molecular weight
In vacuum furnaces metals tend to volatize at temperatures below their melting points. The longer parts are held at the temperature and at a given vacuum level, the greater the loss of the metallic element by evaporation. Where the element is part of a metal alloy system the vapor pressure relationship will change (the total vapor pressure of the alloy is the sum of the vapor pressures of each constituent times the percentage in the alloy – although this relationship has been debated by those knowledgeable in the field).
As heat treaters we often process stainless and tool steels or more exotic alloys in vacuum. Chromium present in these materials evaporates noticeably at temperatures and pressures within normal heat treatment ranges. Processed above 990°C chromium will vaporize if the vacuum level is less 1 x 10-4 torr and parts are held for a prolonged time. Heat treaters often observe a greenish discoloration (chromium oxide) on the interior of their vacuum furnaces, the result of chromium vapor reacting with air leaking into the hot zone. Otherwise, the evaporation deposit is bright and mirror-like. To avoid this, an operating partial pressure between 0.3 and 5 torr is typical for most chromium bearing parts.
For vacuum brazing (silver, copper, nickel) depletion of the filler metal alloy can be avoided by raising the pressure in the furnace to a level above the vapor pressure of the alloy at brazing temperature. For example, copper having an equilibrium vapor pressure at 1120°C of 1 x 10-3 torr is usually run at a partial pressure between 1 and 10 torr. Nickel brazing normally is done in the 10-3 to 10-4 range. However, in the 10-5 to 10-6 torr range you run the risk of losing some of the nickel which has an equilibrium vapor pressure of 1 x 10-4 torr at 1190°C.
For example, processing aluminum, cadmium, magnesium, manganese, and zinc or their alloys at temperatures as low as 400°C may be marginal or totally impractical. This is why processing brass (a mixture of copper and zinc) is normally not done in vacuum systems or if it is, at partial pressures near atmospheric. As the temperature increases, fewer and fewer materials can be run without being affected.
A Little Closer Look
Vapor pressure (aka equilibrium vapor pressure) is defined as the pressure at which the vapor phase is in equilibrium with the liquid (or solid) phase at any given temperature. Below this pressure, surface evaporation is faster than condensation while above it surface evaporation is slower. A substance with a high vapor pressure at normal temperatures is considered volatile. The equilibrium vapor pressure is an indication of a liquid’s evaporation rate, that is, its tendency for particles to escape from the liquid or solid.
As the temperature increases there is a resultant increase in the kinetic energy of molecules (i.e., more molecules enter the vapor phase, thereby increasing the vapor pressure). The vapor pressure of any substance increases non-linearly with temperature according to the Clausius-Clapeyron relation and is often expressed via graphs (Fig. 1) or tabular data (Table 2).
However, for many real world applications, empirical formulas and experimental data are more useful to find the vapor pressure of an element. In this writer’s experience you must increase by 1 or 2 decades the values obtained from this graph to be safe from the effect of evaporation.
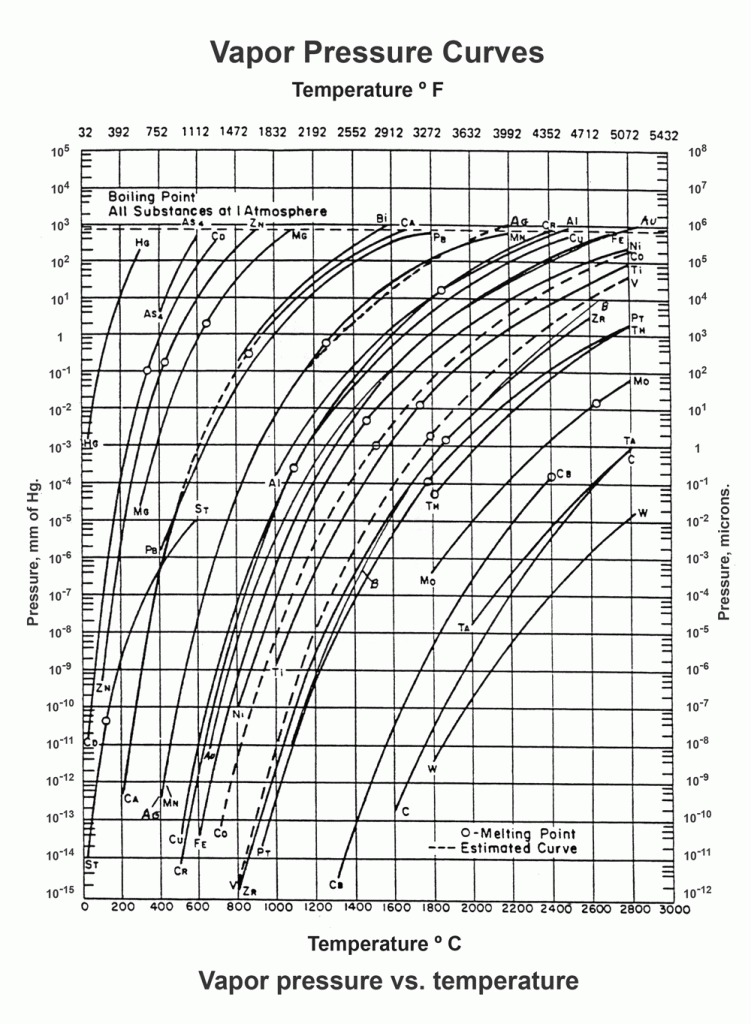
Materials of Construction Used In a Vacuum Furnace
A basic vacuum relationship exists8 between the gas load present in a vacuum furnace and it pumping speed and pressure (Equation 2)
(2) Q = S x P
Where
Q is the gas load (torr-liters/second)
S is the pumping speed (liters/seconds)
P is the system pressure (torr)
Simply stated, the lower the gas load, the lower the pressure for any given pumping speed. Therefore, both the materials of construction used inside the vacuum furnace and the operation of the vacuum furnace itself must be carefully considered (this is one reason why vacuum furnaces should not be left open to room air any longer than is absolutely necessary to unload and reload a new workload and why they should be pumped down when idled or not in use). The goal is to minimize the gas load produced from all of the material present (especially those in the hot zone) such as steel, stainless steel, refractory metals, ceramics, graphite based products and even plastics or quartz. Ceramic fiber insulation is a good example of a hidden problem in vacuum furnace construction, since the material is hydroscopic (i.e. will absorb moisture when exposed to air). This must then be dealt with during the process. If ceramic fiber is used, it should be in a vessel that has limited exposure to air. Any internal surfaces covered with moisture (i.e. water molecules) will have to be removed during the pumpdown. Coupled to this effect is permeation of gases from the atmosphere through the chamber’s walls, and this includes sealants and/or gasket materials such as O-rings (which is one of the reasons why O-rings should be handled with lint-free gloves and care should be taken when wiping them down with alcohol or another solvent since these are absorbed and result in swelling and the potential for outgassing).
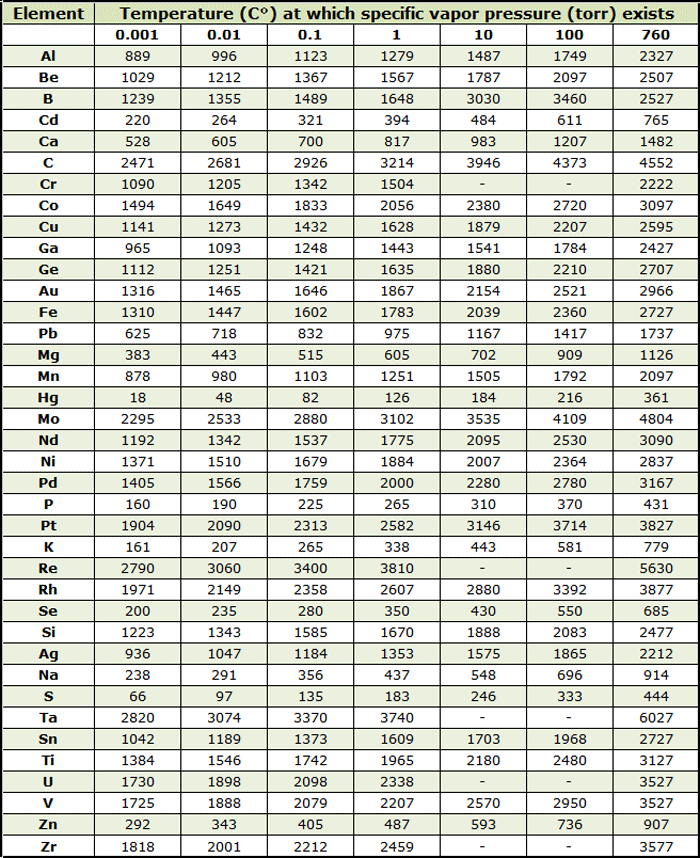
Application Example
Evaporation rates can be controlled and used to our advantage for processes such as the deposition of metallic thin films. The objective here is to control the evaporation and transfer of atoms from a heated source (which can be a liquid or a solid) for deposition on a substrate located a distance away, with the objective of growing a film. The source is heated directly or indirectly until a point is reached where it efficiently sublimes or evaporates. Temperature, evaporation rate and vapor pressure become key process variables as well as the placement of the heater, source and substrate.
The evaporating atoms and molecules leaving the surface of the source will travel in a more or less straight path until they reach a surface at lower temperature (the substrate, the chamber walls or even the instrumentation) where they will condense.
For this to happen effectively, the pressure has to be in the region of free molecular flow. Since these surfaces are at much lower temperatures, the molecules will transfer their energy to the substrate thereby lowering their temperature, which causes them to condense. Since the vapor pressure at this lower temperature is much higher, they will not re- evaporate but adhere to the substrate. This typically occurs at pressures below about 10-7 bar. This process can be used to produce thin metal films, optical filters, mirrors and beam splitters. The resulting deposition thickness is a function of the evaporation rate, the geometry of the source and the substrate, and the time of evaporation.
Final Thoughts
The use of partial pressure (see reference 3) is a practical solution to concerns over evaporation in many of our heat treatment and brazing operations to help us achieve the results we expect. The choice of partial pressure gas, where and how it is introduced, the temperature at which it needs to be introduced and the pressure range(s) over which it acts are all important considerations both from a quality and cost standpoint.
References
- Steel Heat Treatment Handbook, George E. Totten and Maurice A.H. Howes (Eds.), Marcel Dekker, Inc., 1997.
- Herring, Daniel H., Vacuum Heat Treatment, BNP Media Group, 2012.
- Herring, Daniel H., “Using Partial Pressure in Vacuum Furnaces”, Industrial Heating, November 2005.
- Wikipedia (www.wikipedia.org)
- Mackay, Donald and Ian van Wesenbeeck, “Correlation of Chemical Evaporation Rate with Vapor Pressure”, Environ. Sci. Technol., 2014, 48 (17), pp. 10259–10263, 2014 American Chemical Society
- “Vacuum Evaporation” Presentation, Wake Forest University (www.wfu.edu)
- Hablanian, Marsbed H., High-Vacuum Technology: A Practical Guide, Second Edition, Revised and Expanded, Marcel Dekker, Inc., 1997.
- Danielson, Phil, “Choosing the Right Vacuum Materials”, R&D Magazine, April 2003.
Daniel H. Herring / Tel: (630) 834-3017) /E-mail: dherring@heat-treat-doctor.com
Dan Herring is president of THE HERRING GROUP Inc., which specializes in consulting services (heat treatment and metallurgy) and technical services (industrial education/training and process/equipment assistance. He is also a research associate professor at the Illinois Institute of Technology/Thermal Processing Technology Center.