Many of us who use vacuum furnaces are all too familiar with and have learned how to counteract the unintentional diffusion bonding that has been known to occur between component parts exposed to high temperatures and low vacuum levels.1
By contrast, vacuum technology that has found an important niche is that of diffusion bonding by design2-6. Vacuum diffusion bonding relies on temperature, pressure, time, and (ultra low) vacuum levels to facilitate atomic exchange across the interface between the materials.
The process will work on similar or dissimilar materials so long as they are in intimate contact with one another. Vacuum diffusion bonding can be performed with or without pressure being applied and with or without the assistance of a short-lived low melting point “filler metal” (i.e. “activation layers or interlayer”) to facilitate the joining process.
Why Diffusion Bonding?
Users of vacuum diffusion bonding are often interested in increased joint strength, improved flow characteristics and/or optimizing electrical or optical pathways. Diffusion bonded assemblies can be as simple as bonding the cross-over points of steel wires in fabricated metal mesh for industrial filters, or as complex as bonding rare earth metals to copper heat sinks for nuclear industry applications.
The result of the process is joints suitable for use by a variety of industries, including aerospace, medical, chemical, electronic, optics, energy and instrumentation. Joints are sound, strong and capable of withstanding high service temperatures and/or ultra low vacuum levels. In certain applications, the bond is reversible, a highly desirable feature where, for example, an expensive optic (e.g. diamond or sapphire) has been incorporated into a mounting or housing that subsequently needs to be modified or replaced.
Application Examples
A multitude of structures and materials have been successfully diffusion bonded including:
- Sensors, implantables (titanium)
- Cold plates and flexible thermal straps (aluminum, copper)
- Heat exchangers (stainless steel, superalloys)
- Medical devices (implantables)
- Fuel cells, reactors, reformers, and heat exchangers (microchannel devices)
- Space vehicle components (valve assemblies, robotic assemblies, etc.)
- Robotic and remote device assemblies (submarines, offshore oil industry)
- Electron beam windows
Other common applications include the production of shim assemblies for mini or microchannel devices (used for manifolds, biomedical implants, nozzles, mixers, and other precision assemblies), photo etched laminates, gigahertz waveguides and antennas, corrosion resistant manifolds, and microchannel heat exchangers, meeting the ASME Boiler and Pressure Vessel Code.3 The process has also found a niche in applications where the end-use application temperatures are very high and there is a risk of traditionally joined alloy material softening and/or the joint weakening in service.
Factors to Consider
Vacuum diffusion bonding projects should be reviewed for exact pressure measurements to consider material parameters such as surface finish, flatness, thickness, and hermetic seal requirements. The following factors are typical of what is to be considered:
- End-use service environment
- Suitability of the component design (i.e., end-use application)
- Component part flatness / roughness
- Surface (boundary) features
- Surface chemistry and metallurgy
- Load application profile
- Production tooling design
- Temperature uniformity profile design
- Processing force vectors (stress/stain)
If used, applied pressure requirements should be carefully calculated. Pressure can be applied by dead weights, plates with rods, hydrostatic pressure, differential thermal expansion tooling, or active loading using a pneumatic or hydraulic ram system. The selection of the method of applying pressure is important in minimizing the amount of plastic deformation experienced by the component. Fixtures are typically made of ceramics and/or refractory metal (e.g., molybdenum) and designed to achieve an expansion in the range of ± 0.05 mm (0.002”). Expansion of fixtures is a major consideration in achieving desired results.
Diffusion Bonding With and Without Filler Metal
An example7 of vacuum diffusion bonding with aid of a filler metal is the joining of small plates of Inconel MA 758 (30% Cr, 0.3%Al, 0.5%Ti, 0.65Y2O3, 1.0%Fe, 0.05%C, balance Ni). The joining surfaces were prepared by grinding down to 600-grit (SiC) paper finish to ensure flatness. Prior to bonding operation, parts were cleaned in acetone. Commercially available nickel based interlayers (Table 1) in the form of thin foils were used.
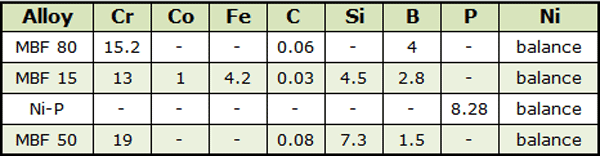
The joining process was performed in a vacuum induction furnace with the vacuum of 0.053 N/m2. A minimum bonding pressure of 196 kN/m2 was applied to keep the bonding surfaces in an intimate contact. The bonding times used were 120, 900 and 1800 seconds depending on the melting temperature of interlayers the bonding temperatures of 1120ºC, 1000ºC and 1170ºC were used for; MBF 80, MBF 15, Ni-P and MBF 50 interlayers, respectively. The parts were furnace cooled to room temperature in vacuum once the holding time was completed.
For metallographic examination (Fig. 1), the bonded samples were sectioned through the joint region and one half of each bonded sample was then heat-treated using a temperature of 1360ºC for two (2) hours. All specimens were prepared using standard methods of metallographic preparation and the joint region was examined using light and scanning electron microscopy. The changes in the composition of the bond interface were examined using energy dispersive x-ray spectroscopy (EDS). Micro-hardness testing was done to assess the homogeneity of the bond region as well (Note: See reference 6 for more specific details).
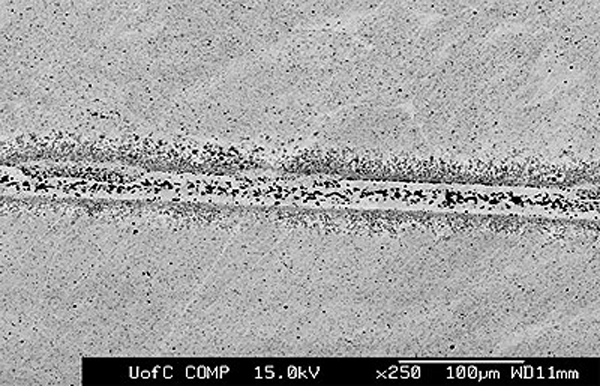
Diffusion bonding can also be used to provide a more integral bond between difficult to diffuse materials. Ceramic-to-ceramic and ceramic-to-metal applications such as diffusion bonding of silicon carbide to silicon carbide benefit from use of a metal filler (e.g., Nb, Mo, Ti, W) to not only promote bonding but also reduce joining temperatures, in this instance from (approximately) 2000ºC to around 1500ºC and overall cycle time.8
A key feature of diffusion bonding is that often no filler material is used so that the joint has properties similar to base materials when properly performed (Note: Traditionally, vacuum diffusion bonding was defined as a process whereby separate parts were joined without the use of filler metal but this definition has been relaxed in recent years). A good example is applications requiring highly accurate and exact contour bonding of precision components such as the diffusion bonding of micro-coolers and/or micro-reactors that are characterized by extremely fine channel structures near the joint).
A Cautionary Tale
One of the writer’s early experiences with vacuum diffusion bonding underscores the importance of attention to detail. In this instance, the design of the system for applying uniform pressure to all surfaces was inadequate for the task. Individual sheets of stainless steel were being diffusion bonded to one another by compressing the stack using a hydraulic ram installed inside a vacuum furnace. Deformation of the lower support platen (due to a poor design) created a mixture of properly and improperly joined areas and poor results.
In Summary…
Vacuum diffusion bonding has made great strides in recent years and overcome many of the problems that plagued the technology in the past (e.g., dirty materials, uneven contact surfaces, equipment design limitations and equipment design flaws) and as such has become a robust technology and one worthy of consideration by the design engineer.
References
- Herring, Daniel H., Vacuum Heat Treatment, BNP Media Group, 2012.
- Herring, Daniel H., “Tips for Improving Vacuum Performance & Operation, Part Five”, Vac-Aero International Inc.
- Vacuum Process Engineering (www.vpei.com)
- Solar Atmospheres (www.solaratm.com)
- Vacco Multi-Fab (vacco-etch.com)
- CCFW (www.ccfe.ac.uk)
- Saha, R. K., and T. I. Kahn, “TLP Diffusion Bonding of a ODS Nickel Alloy”, The AZo Journal of Materials Online, Volume 2, July 2006.
- Ceramic Materials for Energy Applications IV (Hua-Tya Lin, Yutai Katoh, Josef Matyas, Eds.): Ceramic Engineering and Science Proceedings, Volume 35, Issue 7, John Wiley & Sons, 2014, pp. 150 – 152.
- Kazakov, N. F., Diffusion Binding of Materials, Elsevier Ltd., 1985.
Daniel H. Herring / Tel: (630) 834-3017) /E-mail: dherring@heat-treat-doctor.com
Dan Herring is president of THE HERRING GROUP Inc., which specializes in consulting services (heat treatment and metallurgy) and technical services (industrial education/training and process/equipment assistance. He is also a research associate professor at the Illinois Institute of Technology/Thermal Processing Technology Center.