Metal matrix composites are becoming increasingly popular for industrial applications as diverse as aerospace, automotive and electronics. The composites consist of an alloy matrix reinforced with ceramic particles to enhance mechanical properties. Aluminum alloys are especially popular as a matrix material.

The SiC volume fraction and particle distribution in plasma sprayed composite coatings are largely dependent on the quality of the powder being used during spraying. In powders prepared by blending SiC with aluminum alloy particles, the SiC particles are preferentially lost during spraying compared to the aluminum particles.The addition of relatively inexpensive silicon carbide (SiC) particles to an aluminum alloy matrix improves strength, elasticity, wear resistance and corrosion resistance. These composites are used widely for high performance structural components in aerospace and automotive applications. Current techniques for fabricating the composites include casting, extrusion, powder metallurgy and thermal spray deposition. In the techniques for bulk fabrication of composite components, inherent defects such as porosity, shrinkage, oxide inclusions and segregation of the carbide particles can reduce properties such as toughness and low temperature ductility. However, the use of composite coatings deposited by plasma spray on aluminum alloy substrates can produce a component with excellent surface properties while maintaining the ductility of the substrate.
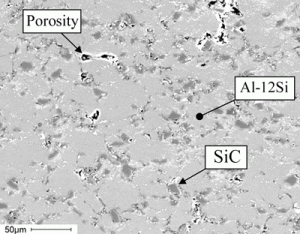
Excess SiC must be added to compensate for the losses. But despite these additions, the volume fraction of SiC that can be obtained in the coating is still limited. This is attributed to the large differences in melting temperature between the SiC and the aluminum alloy and the poor wettability of SiC by aluminum. The other challenge in applying composite coatings by air plasma spray is minimizing the effect of the heat generated by the process on the substrate being coated.
Recently, VAC AERO has been developing techniques to apply composite coatings by the Cold Gas Dynamic Spraying process. With cold spray, the powder particles are not melted, but remain in the solid state throughout the deposition process. The particles are injected into a supersonic gas flow and highly accelerated.
Upon impact, they plastically deform and form a strong bond with the substrate. VAC AERO’s studies showed that composite coatings containing up to 30% of SiC within an aluminum matrix could be obtained. Furthermore, it was determined that the cold spray process can apply thicker coatings with much higher deposition efficiency than air plasma spray techniques, and, the low temperature of the cold spray process causes no negative effects to the substrate.
VAC AERO, in cooperation with the Mechanical Engineering Department at the University of Ottawa, is continuing research into this most promising technique.