BY JEFF PRITCHARD
The hot zone is perhaps the most critical feature of a vacuum furnace in terms of its effect on furnace performance and operating cost. There are a variety of hot zone designs and the choice of a design should be based on a careful analysis of specific processing applications.
Most vacuum-furnace hot zones consist of four major components: the heating elements and the details on which they are mounted; the insulation package (or heat shields); a surrounding structure that supports the heating elements and insulation package; and a hearth that supports the load during processing. A hot zone can be constructed in either rectangular or cylindrical form, with the latter being far more prominent in vacuum furnaces today. All hot zones are constructed in modular form for ease of installation into and removal from the vacuum chamber (Fig. 1)
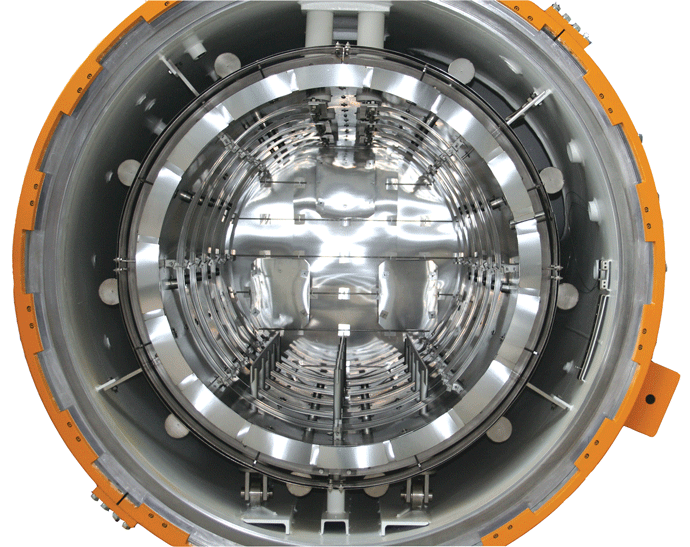
Hot Zone Construction
Heating Elements
Almost all high-temperature vacuum furnaces are electrical-resistance heated. Heating elements may be constructed from metal or graphite in a variety of styles. The choice of a heating-element material depends largely on operating temperature. For low-temperature operations such as vacuum tempering, inexpensive nickel-chromium alloys can be used for the heating elements. For higher-temperature general heat-treating applications such as hardening or brazing, molybdenum or graphite are the most popular element materials. For heat-treating applications above about 1482°C (2700°F), a refractory metal such as tantalum is a popular choice, though graphite is also used.
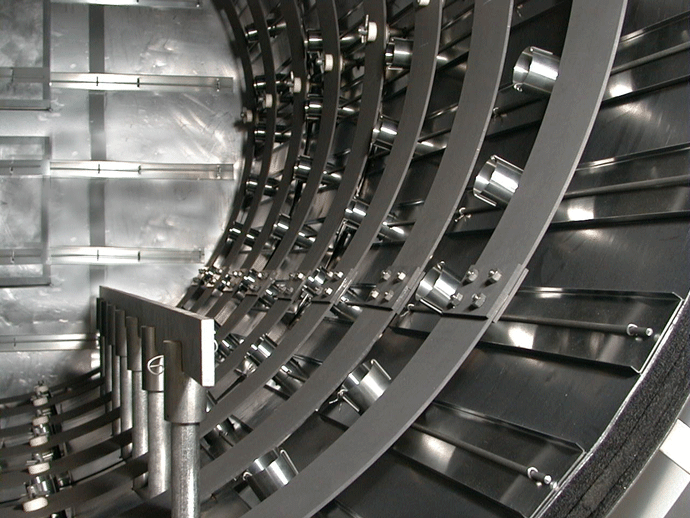
For many years, molybdenum elements were used almost exclusively in vacuum furnaces for general heat-treating and brazing applications. There was a widespread misconception that emissions from graphite elements could react with and contaminate certain materials. Early graphite-element designs were bulky and limited to simple shapes. Furthermore, connections between element segments and electrical feedthroughs were prone to failure. With advances in both materials and manufacturing techniques for graphite-based electrical products, however, the popularity of graphite heating elements now exceeds that of molybdenum elements in general heat-treating and brazing furnaces. The most widely used graphite-element design incorporates lightweight, curved bands that are durable and easy to work with (Fig. 2).
Insulation/Heat Shield
Molybdenum and graphite are also used for vacuum-furnace insulation. In an all-metal hot-zone, the heat-shield package is made up of multiple layers of sheet metal with spaces between each layer (Fig. 3). In a standard furnace with a maximum 1315°C (2400°F) operating temperature, the heat shielding often consists of two layers of molybdenum sheet backed by three layers of stainless steel sheet. For higher operating temperatures, the number of molybdenum layers is increased as well as the thickness of each layer. For very high operating temperatures over 1650°C (3000°F), tantalum sheet can be used in place of molybdenum. The insulating properties of the all-metal design come mostly from the gaps between the layers of sheet metal. These gaps prevent heat from being conducted outward from the hot zone. The reflectivity of the inner molybdenum sheet also helps to direct the radiant heat from the elements inward toward the load. All-metal hot zones tend to be preferred when high-vacuum or very clean processing environments are required (medical-component processing). Care must be taken in operating furnaces with all-metal hot zones because molybdenum embrittles due to recrystallization after a single exposure to temperatures above about 1150°C (2100°F). Embrittled heat shields can be relatively easily damaged if struck by fixtures or parts. Due to the high cost of molybdenum, all-metal hot zones also tend to be more expensive than some other choices.
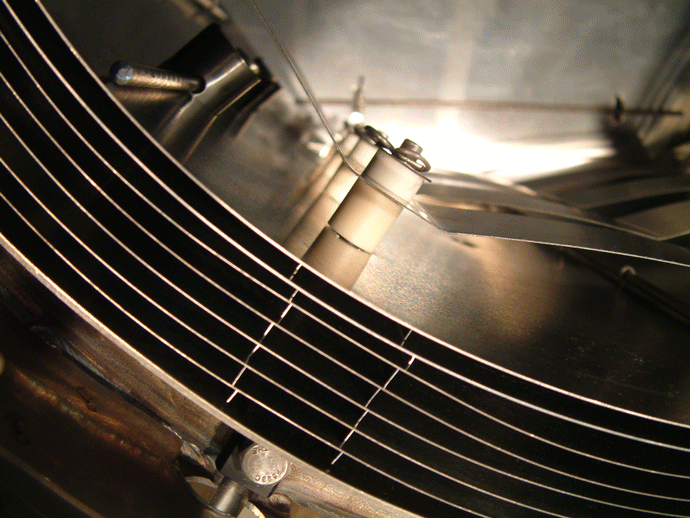
Another popular heat-shield design incorporates graphite-based materials. A standard graphite insulation package normally consists of a minimum thickness of 1.5 inches of graphite-based material in the form of layers of blanket or board. An inner face of graphite foil or foil-bonded carbon composite is added to enhance reflectivity. Because the insulating material is itself porous and permeable, no spaces are required between the layers. These graphite-based materials have excellent insulating properties, are usually cheaper than metal heat shielding and are very easy to work with. Graphite blanket has some advantages over graphite board in terms of construction cost, durability and ease of maintenance.
The hot-zone support consists of a cylindrical steel ring or multiple rings depending on furnace size (Fig. 4). Though slightly more expensive, constructing the support from stainless steel rather than carbon steel increases its durability substantially. In most vacuum-furnace designs, the support also acts as a manifold to distribute the quenching gas throughout the load. The gas is forced out through nozzles that are built into the rings. The rings are hung in the furnace tank with stainless hangers and clamps. At the front and rear of the furnace (or top and bottom for vertical models), the support consists of a heavy-gauge stainless steel sheet metal and bar structure upon which the insulation package is mounted.
Hearth Choices
The hearth is the structure that supports the load during heat treating. Again, molybdenum and graphite are the most popular choices as hearth materials in vacuum furnaces. The hearth is usually constructed of rails upon which the load sits, with the rails supported by pins mounted on reinforced areas of the furnace chamber. Because of the material’s higher strength, a molybdenum hearth can be built with less mass than a graphite hearth designed to support the same load. Unlike the molybdenum sheet used in elements and heat shields, the thicker sections of molybdenum used in the hearth components are not easily damaged even after recrystallization. Molybdenum hearth rails sometimes warp after long-term thermal cycling, however, and must occasionally be hot-straightened. A graphite hearth is very rigid and will maintain its shape almost indefinitely. Though its heavier mass may result in slower heating rates at lower temperatures, the good thermal conductivity of graphite tends to minimize this effect. While usually less expensive than molybdenum, graphite hearth rails can be prone to chipping during the transfer of furnace loads. Newly developed graphite-fiber-based materials are more resistant to chipping but very expensive – even compared to molybdenum.
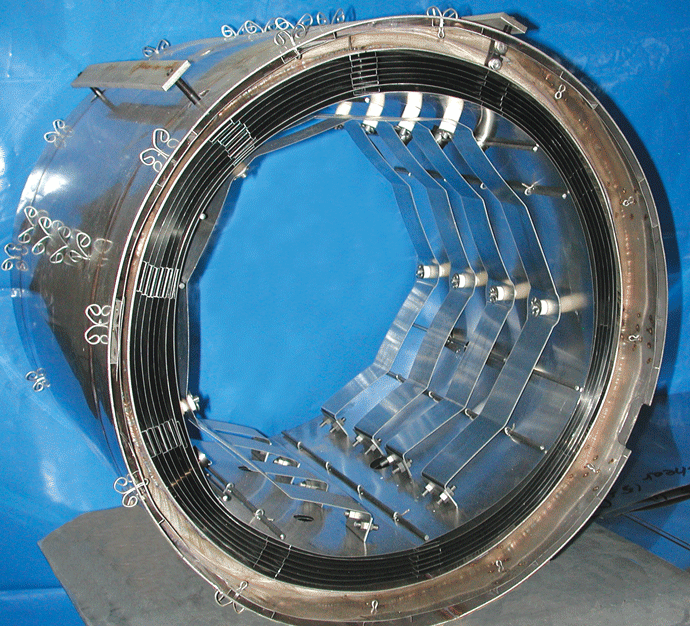
A major issue when selecting a hearth material is the possibility of solid-state diffusion between the hearth and load at high temperatures. Solid-state diffusion of certain elements can cause a phenomenon known as eutectic melting. For example, solid-state diffusion between carbon and nickel can begin to occur at temperatures as low as 1165°C (2130°F), causing localized melting. As nickel is a common element in many steels (particularly stainless), these steels should not be allowed to come into contact with graphite hearths or fixturing materials during heat treating. For this reason, graphite hearth rails are usually designed to accommodate ceramic or molybdenum inserts that isolate the load from the graphite in the hearth. High concentrations of nickel are also present in many of the high-temperature materials used in the fabrication of furnace baskets and grids. Under the proper conditions, molybdenum will also combine with other elements to cause eutectic melting. The molybdenum reactions with the more common alloying elements in steel, however, tend to occur at temperatures well above the normal heat-treating range.
Vacuum Brazing Case Study
VAC AERO’s Thermal Processing Division in Oakville, Canada, provides repair services for damaged components from land-based and aerospace gas-turbine engines. Engine manufacturers, operators, overhaul centers and commercial airlines are just a few of the customers that depend on these services. Many hot-section engine components are fabricated from nickel-based superalloys. These materials cannot be repaired by traditional techniques, such as welding, without causing significant reductions in mechanical properties. Therefore, VAC AERO developed proprietary vacuum-brazing techniques to repair cracks, wear, and other service-induced damage.
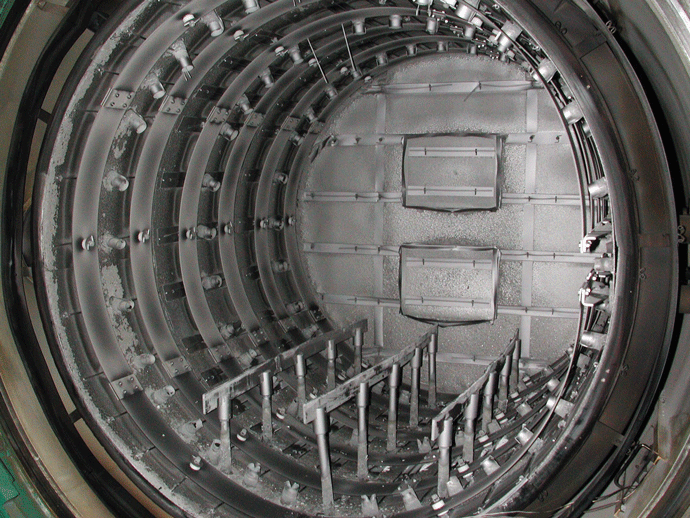
The extent of damage to the engine components is often severe. As a result, the brazing process involves the use of large amounts of brazing filler metal to make the necessary repairs. When subject to high temperature under vacuum, volatile metallic and organic constituents vaporize from the filler metal. While a portion of these volatiles are removed from the furnace chamber by the vacuum pumping system, the balance tends to condense within the chamber, much of it depositing on the hot-zone insulation. In addition, excess molten braze alloy occasionally drips from the workload onto the heating elements and insulation, despite the use of drip trays. These deposits can have a detrimental effect on the performance of the furnace.
Many nickel-based superalloys contain alloying elements like aluminum and titanium that form stable oxides in the presence of moisture or other contaminants in the brazing environment. Oxides inhibit the flow of the filler metal, making the superalloy particularly difficult to braze. Traditionally, vacuum furnaces used for brazing of superalloys were built with all-metal hot zones insulated with layers of molybdenum and stainless steel sheet. Because metal insulation does not readily absorb moisture or other contaminants, it was considered the only type of insulation that would provide a suitably clean environment for processing difficult-to-braze materials. Graphite insulating products were considered too “dirty” for brazing exotic materials like nickel-based superalloys.
New Hot-Zone Design
Through production experience, the manufacturer had determined that all-metal insulation does not stand up well in aggressive brazing environments. As condensed metallic constituents from the brazing filler metal build up, the metal insulation begins to curl and crack due to differential expansion between the insulation and the deposit from the filler metal. This eventually causes a deterioration of the hot zone’s insulating properties. Metal insulation is also particularly vulnerable to braze-alloy spillage. Molten braze alloy will often dissolve metal shielding, leaving holes through which heat can escape. The use of thicker sheet and special molybdenum alloys in the insulation will extend the life of an all-metal hot zone but also add considerable expense.
As a manufacturer and user of vacuum furnaces, VAC AERO needed a hot zone designed to withstand aggressive brazing applications and therefore decided to evaluate the performance of graphite-based insulation and heating elements. Tests confirmed that a properly maintained hot zone incorporating these materials can be used to successfully and consistently join difficult-to-braze materials such as nickel-based superalloys. Indeed, the results were better than anticipated. The hot-zone insulation consisted of three layers of graphite blanket with an inner face of foil-bonded carbon composite. While there is little doubt that graphite insulation is more likely to absorb moisture than metal insulation, regular burn-out cycles will rid the insulation of moisture and contaminants that are detrimental to the brazing process. The heating elements were lightweight, curved graphite.
The hot-zone design performed remarkably well. Figure 5 shows this hot-zone design in a production furnace after almost five years of daily use in aggressive brazing applications. While the hot zone has a heavy build-up of metallic deposit, it remains completely intact, and the furnace regularly qualifies to the most stringent pyrometry standards. The photograph also shows the durability of the lightweight, curved graphite elements used in these vacuum furnaces. Though substantial amounts of braze alloy were spilled on these elements, there was no deterioration in performance.
VAC AERO’s tests confirm that a well-built hot zone incorporating graphite-based materials can be used as a more durable and economical alternative to traditional all-metal designs in even the most difficult processing applications. Regardless of hot-zone design, however, proper preventive maintenance and good heat-treating practices are essential to maximizing service life.
For more info on VAC AERO Hot zones please click here.