BY JEFF PRITCHARD
In vacuum processing, metal surfaces remain very clean and free of oxides. When these near-perfect surfaces are in contact with other surfaces, certain elements have a tendency to interact between the surfaces through solid state diffusion. Therefore, a major consideration when selecting both hearths and load fixturing materials for vacuum heat treating is the possibility of solid-state diffusion between different materials in contact at high temperatures. Solid state diffusion of certain elements can cause the formation of a lower melting point alloy called a eutectic. For example, solid-state diffusion between carbon and nickel can begin to occur at temperatures as low as 1165ºC (2130ºF) and cause local melting, also known as eutectic melting.
As nickel is a common element in many steels (particularly stainless steels), these steels should not be allowed to come into contact with graphite hearths or fixturing materials during heat treating. For this reason, graphite hearth rails are usually designed to accommodate ceramic inserts that separate the load from the graphite. High concentrations of nickel are also present in many of the high-temperature materials used in the fabrication of furnace baskets and grids. Under the proper conditions, molybdenum will also combine with other elements to cause eutectic melting. However, the molybdenum reactions with the more common alloying elements in steel tend to occur at temperatures well above the normal heat treating range. Table I shows eutectic combinations and the temperatures at which solid state diffusion can cause melting.
Severe eutectic melting reactions can cause extensive damage to workloads and furnace hot zones. There are dozens of cases where eutectic melting has resulted in tens of thousands of dollars in furnace repairs alone. Therefore, an active approach to preventing this phenomenon should become standard practice. The best solution is to separate potentially reactive materials from each other with completely non-reactive insulators. There are several options to consider. High purity stable ceramic materials such as aluminum oxide or zirconium oxide are popular choices.
These are often available in the form of papers, cloth blanket, plates or other solid shapes upon which the workpieces can be placed. It should be noted that some ceramic papers and cloths can release abrasive fiber particles that can lead to deleterious effects on vacuum pumping systems. Ceramic materials are also available in the form of stop-off paints that can be applied liberally to furnace baskets, grids or other fixtures. These coatings must be inspected and touched up regularly as they will deteriorate with use. The same materials can be applied by plasma spray. This process provides a thicker and more durable protective finish but is slightly more expensive than the paint-on versions.
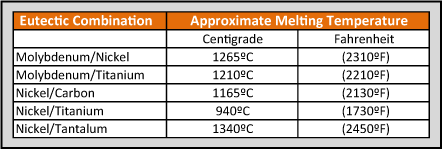
As a heat treat and furnace manufacturer, VAC AERO can assist you in developing best practices for vacuum heat treating. VAC AERO also offers plasma spray coating services to protect your heat treat tooling. For more information on VAC AERO’s Heat Treating Services please click here.