BY JEFF PRITCHARD
For heat treating purposes, “quenching” can be defined as the rapid cooling of a metal to impart some desired property such as hardness. Different metals and alloys require different quenching rates to achieve their optimum properties. Regardless of equipment design, gas quenching in vacuum furnaces involve the same basic principles.
The gas quenching process normally consists of the following sequence of events. First, the power to the heating elements is shut off. Next, the furnace chamber and quench loop are backfilled with a non-reactive gas, commonly nitrogen or argon. The quench blower then activates, forcing the gas through quench nozzles located circumferentially in a manifold that is part of the hot zone and into the hot load. As the gas passes over the load, it picks up heat. The hot gas then exits the main chamber and travels through the quench piping to a water-cooled heat exchanger, where it is cooled. After exiting the heat exchanger, the cooled gas is drawn back through the blower to be recirculated through the chamber in a continuous cooling loop.
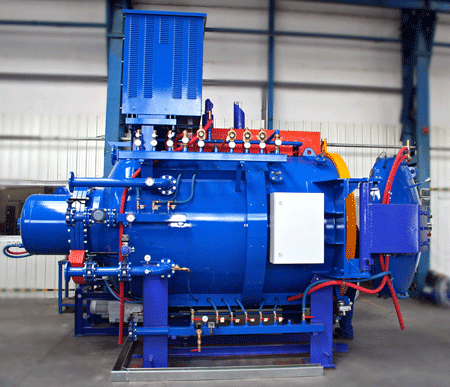
There are two popular quench loop designs available in modern vacuum furnaces. In the external quench loop design, the blower housing, heat exchanger housing and quench piping are located outside the vacuum heating chamber. In the internal quench loop design, the quench blower and heat exchanger are contained within the chamber. While cooling performance criteria are very similar for both designs, each has some advantages and drawbacks.
One of the advantages of an internal quench loop furnace is its compact design. It occupies slightly less floor space than a similarly-sized external quench loop furnace. This statement however does come with a caveat, you still need additional room around the furnace order to access some of its components for maintenance, sometimes while using a forklift. Another advantage sees the elimination of a separate housing for the external quench blower and the heat exchanger. But the chief drawback of this design is the close proximity of the quench blower motor (including drive shaft and bearings) to heat emanating from the furnace hot zone. If a failure of a motor component or heat exchanger does occur, it may be necessary to remove the entire hot zone to gain access for repairs. There is also the risk of considerable damage to the furnace internals, and possibly the load, if the heat exchanger should ever develop a water leak.
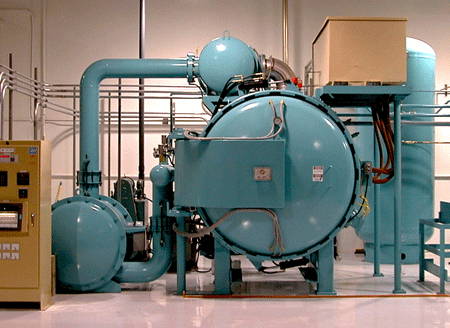
The external quench loop design requires only minimally more floor space than a similar internal quench loop furnace. However, the external design permits much easier maintenance access to the blower and heat exchanger. These can be accessed by simply removing a cover from the housing. The external loop design also minimizes the occurrence of quench blower failures by isolating sensitive components from exposure to heat from the vacuum chamber. Furthermore, any water leaks that might occur in the heat exchanger can be contained within the separate heat exchanger housing.
For more information on VAC AERO’s Furnace Manufacturing please click here.