BY JEFF PRITCHARD
Good fixturing and loading practices are essential elements in achieving proper heat treating results and long equipment life.
Fixture materials and design must be appropriate for the processing application. Maintenance of fixtures is equally important. The possibility of reactions between the workpieces and baskets or fixtures must also be considered. High-temperature sintering of the workpieces to themselves or the fixtures can occur. Eutectic melting can also occur when certain chemical compositions come into contact at high temperature. Selection of a fixture material is influenced by cost, service environment and compatibility with the workpiece and furnace hearth.
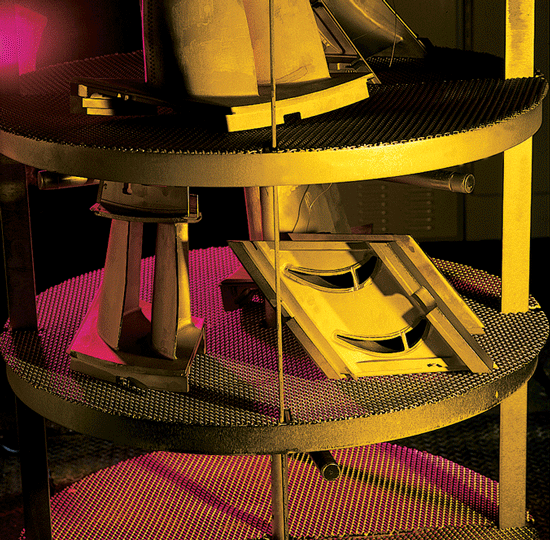
For service temperatures up to about 980ºC (1800ºF), austenitic stainless steels such as Types 304, 309 and 310 are commonly used. However, these alloys can become embrittled from long exposure to temperatures in the range of 595ºC to 815ºC (1100ºF to 1500ºF) due to carbide precipitation and sigma formation. In this temperature range, more expensive alloys such as 35Ni-15Cr or Inconel 600 tend to be more stable and may justify the extra cost.
For higher temperatures, alloys like Haynes 230, nickel-base oxide-dispersed alloys such as MA 956 or pure molybdenum provide good life. Care must be taken in handling fixtures made from molybdenum because of their embrittled condition after high-temperature exposure. For some special applications, graphite fixtures are used. The strength of graphite increases with temperature, it has good thermal shock resistance and conductivity and it is relatively inexpensive. These properties make graphite an excellent fixture material, particularly in the form of a plate to support large workpieces where flatness must be maintained. However, because graphite reacts with many alloys at heat treating temperatures, the furnace hearth and workpieces should be insulated from graphite fixtures during processing.
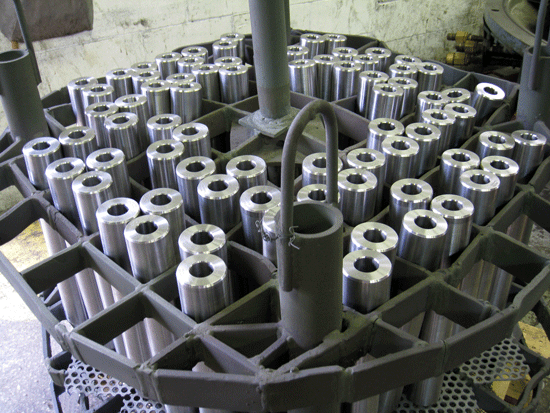
The primary objectives in designing a fixture are to minimize thermal mass (weight), achieve a long service life and minimize cost. A low thermal mass is important for efficient heating and cooling. Service life is largely dictated by the fixture material. However, certain fixture materials, such as molybdenum, are not weldable and must be fabricated using mechanical fastening. This can add to fabrication and maintenance costs.
When designing fixtures that clamp or restrain the workpiece (such as hot straightening fixtures or some brazing fixtures), careful consideration must be given to differences in thermal expansion between the workpiece and fixture. When possible, the coefficient of thermal expansion of the fixture material should closely match that of the workpiece.
Before being used in production, it is recommended that a new fixture be subject to a vacuum bake at a temperature at least 25ºC (45ºF) higher than its maximum operating temperature. This will degas the fixture to rid it of any contaminants formed in fabrication, such as welding oxides. Fixtures may also require periodic grit blasting if they become discolored during service. Regular inspections for cracking, distortion or other thermal cycling damage should be performed. To avoid catastrophic failures, damaged fixtures should be repaired or replaced immediately.
VAC AERO engineers can assist you in fixture material selection and design for vacuum processing.
Contact us to discuss your requirements.
For more information on VAC AERO’s Furnace Manufacturing please click here.