BY JEFF PRITCHARD
In any heat treating cycle, there are two important considerations concerning temperature: the temperature of the furnace hot zone which is generating the heat input, and the temperature of the actual workload. Heating by direct radiation, the main heating mechanism in vacuum, tends to be a slower process than other heating mechanisms such as convection or conduction. As a result, there are times in the heat treating cycle, particularly during heat up, when the load will be at a lower temperature than the furnace hot zone. This is known as temperature lag. Hot zone temperature is controlled and measured through two (or more) thermocouples located close to the heating elements. One thermocouple, the control thermocouple, is connected to the thermal process controller which transmits signals to control the amount of power directed to the furnace elements.
The second thermocouple is known as the overtemperature thermocouple and is connected to the overtemperature safety controller. Both control and overtemperature thermocouples are also connected to the furnace datalogger to provide a permanent record of time and temperature data. These thermocouples are usually constructed of a platinum-platinum/rhodium combination known as Type S that retains accuracy under vacuum throughout a range between ambient temperature and 1480ºC (2700ºF). The location of these thermocouples within the hot zone is quite important in maintaining good temperature control and uniformity.
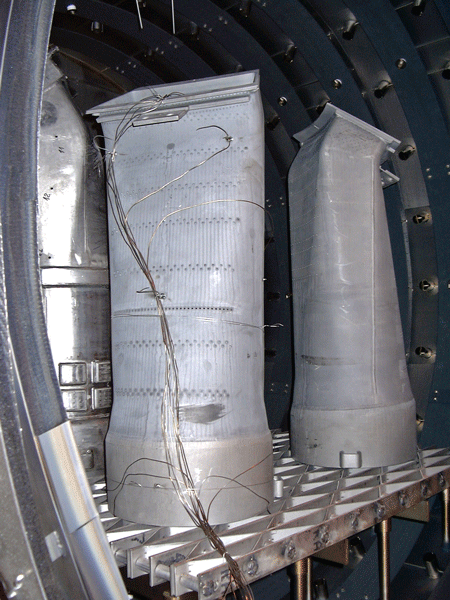
The recommended practice is to use at least three workload thermocouples. One should be buried deep inside the load. The second should be placed at a midpoint between the center and outside of the load. The third can be placed on the surface or outermost limit of the load. Normally, the center of the load will require the longest amount of time to heat to the processing temperature. By monitoring all three workload thermocouples via the datalogger, processing decisions can be made to ensure a sufficient soak of the entire load is achieved. VAC AERO furnaces can also be programmed with a load guaranteed soak feature where signals from workload thermocouples to the thermal process controller ensure that the load automatically receives the full programmed time at temperature. Workload thermocouples are usually attached directly to the load and connected to the furnace datalogger through extension cables. This makes it possible to record the exact time at temperature of the workload. Proper placement of these thermocouples will ensure the load receives the correct time at temperature by making adjustments for any temperature lag. Workload thermocouples are usually a chromel-alumel combination known as Type K, though Type N (nicrosil-nisil) is also popular for general heat treating applications. While these thermocouple types are not recommended for repeated use at high temperatures, they are less delicate and much cheaper than Type S and can be supplied in a flexible construction ideally suited for attachment to a variety of load configurations. The locations where workload thermocouples are placed in the load can have a significant effect on temperature indications.
The automated control systems in VAC AERO vacuum furnaces are designed for repeatability. Once heat treat cycle parameters have been established, using the same load configuration and workload thermocouple placement in subsequent loads will ensure consistent results.
For more information on VAC AERO’s Furnace Manufacturing please click here.