Experience has shown us that sensitive materials in the presence of minute quantities of unwanted gaseous contaminates can destroy the integrity and shorten the life expectancy of components. It is natural to ask ourselves what can be done to further protect the work in a vacuum environment after the pumps have done their part in reducing the chamber pressure to as low as is economically feasible in a production environment? This task falls on getter materials.
What is a Getter?
A getter is simply a reactive material that is deliberately placed inside a vacuum system for the purpose of improving the efficiency of that vacuum by scavenging unwanted contaminates. Essentially, when gas molecules strike the getter material, they combine with it chemically or by adsorption so as to be removed from the environment. In other words, a getter eliminates even minute amounts of unwanted gases from the evacuated space.
Getter materials fall into three broad categories: bulk getters, coating getters, and flash getters. Examples of getters vary from simple foils, wraps and stamped forms to machined turnings placed in and around the work. Getters can also be applied to the surface in the form of coatings or placed in the gas stream in the form of pellets. The hot zone of most vacuum furnaces whether graphite or metallic (e.g. molybdenum and/or stainless steel shields), acts as a getter. Getters are especially important when processing reactive metals such as titanium or tantalum and in sealed systems such as vacuum tubes, cathode ray tubes and the like. The sophistication of the getter is in direct relation to the task at hand.
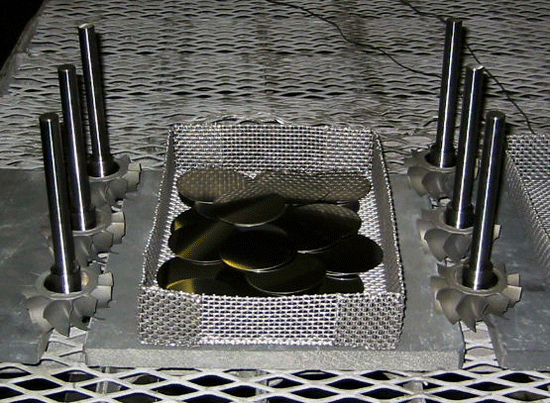
Getter Properties
The action of a getter material depends on:
- Adsorption (i.e. accumulation of gas molecules at the surface);
- Absorption (i.e. diffusion of gas molecules in the solid);
- Chemical binding (i.e. reaction with the surface atoms).
A getter material is designed to react with the gas species present, thus creating a chemical reaction. Typical gases present in vacuum systems are carbon monoxide (CO), carbon dioxide (CO2), nitrogen (N2), hydrogen (H2), and water vapor (H2O). Most metal surfaces have a protective oxide on them, which under vacuum and at high temperature must dissolve and diffuse into the getter material before it can be effective. Thus a getter material must also have the ability to allow diffusion of contaminating gases once they have been absorbed.
Getters bind gases on their surfaces. Thus, the greater the surface area, or the more porous the material, the better it will perform. In some cases getters can be reused provided a bake-out process is employed (typically performed in a vacuum) so as to unbind the absorbed gas species. Certain types of surfaces (e.g. nitrides) require diffusion rather than extraction of the gas to return the surface to a useful condition.
Getter Materials
For most heat-treating applications, stainless steels and metals in Group IV of the periodic table (titanium, zirconium, hafnium) are particularly well suited as getter materials. For more sophisticated applications, tantalum, niobium, thorium and many other materials have been successfully used.
The amount of gas that a getter can absorb is often referred to as its “getter capacity” (Table 1). In more scientific terms, it is the number of atoms or molecules of the contaminating species bound up inside the material.
![Table 1 [1] Getter Capacity of Common Materials](https://vacaero.com/wp-content/uploads/2012/02/getter_capacity_materials_lg-2.gif)
By way of example, the getter capacity of titanium for hydrogen from Table 1 is 27 Pa–l/mg. Since the molar mass of titanium is 48 g/mol, we find that 1 mg of titanium contains 1.25 x 1019 titanium atoms. The Ideal Gas Law (PV = NkT) tells us the state of any amount of gas is determined by its pressure, volume, and temperature. As a result, 27 Pa-l contains 6.7 x 1018 particles (i.e. 6.7 x 1018 hydrogen molecules or 1.34 x 1019 hydrogen atoms). These can be distributed over the 1.25 x 1019 titanium atoms so that each titanium atom in the getter corresponds to (approximately) one hydrogen atom.
The chemical reactions (in simplified form) are as follow (here GM represents the getter material):
(1) 2GM + O2 → 2GMO
(2) 2GM + N2 → 2GMN
(3) 2GM + CO → GMC + GMO
(4) 2GM + CO2 → CO + 2GMO → GMC + GMO
(5) GM + H2O → H + GMO → GMO + H (bulk)
(6) GM + H2 → GMH + H (bulk)
(7) GM + CxHy → GMC + H (bulk)
(8) GM + Inert Gas (He, Ne, Ar, Kr, Xe) → No reaction
Getter capacity is affected by temperature since diffusion rates of the surface-bound gas atoms in the bulk of the getter material increase with temperature. This helps keep the getter surface active continuously and getter capacity rises for gases that bind only to the surface due to chemical reactions. Adsorption also continues for longer periods of time (until saturation).
Titanium can be used as an effective getter material when running titanium parts in a vacuum. For example, to keep parts surfaces clean (i.e. to avoid oxidation and discoloration) during annealing at a temperature in the 650°C – 760°C (1200°F – 1400°F) range, titanium scrap (often in the form of clean, dry machine turnings) is commonly included with the load.
Non-Evaporative Getters
Non-evaporable getters have become an integral part of many ultrahigh vacuum environments mainly due to their unique surface properties which are conducive to achieving extremely high vacuum conditions (in the order of 10-10 mbar (10-9 torr) or lower). Binary, ternary and multicomponent alloys from Group IV and Group V (vanadium, niobium, tantalum) elements are most often used. These generally consist of a film of a special alloy, often zirconium based; the requirement is that the alloy materials must form a passivation layer at room temperature which disappears when heated. Many of these alloys have names of the form St (Stabil) followed by a number:
- St 707 – a 70% zirconium, 24.6% vanadium balance iron alloy;
- St 787 – an 80.8% zirconium, 14.2% cobalt balance mischmetal alloy;
- St 101 – an 84% zirconium and 16% aluminum
In tubes used in electronics, the getter material coats plates within the tube which are heated in normal operation; when getters are used within more general vacuum systems, such as in semiconductor manufacturing, they are introduced as separate pieces of equipment in the vacuum chamber, and turned on when needed.
Final Thoughts
For heat treaters, getters are often considered a last resort to help keep parts “bright and clean”. In point of fact, they play an important role in successful vacuum processing of many highly sophisticated products and materials. As a result, we need to do a better job of understanding their role; how and where they can help.
References