Low-temperature vacuum heat treatment offers unique advantages to a variety of industries including Aerospace, Automotive, Electronics, Household Appliances, Machine Tools and Tool and Die as well as Commercial Heat Treaters who must serve all of these customers. Low-temperature heat treatments that involve a vacuum purge at the onset of the cycle have become increasingly popular throughout the industry. These operations are conducted in vacuum furnaces and furnaces that employ a vacuum purge prior to the beginning of the heating process with parts placed inside a special vacuum tight vessel or in a retort. Processing being run using these methods take advantage of a highly controlled environment designed to minimize surface interactions.
This article will discuss the key factors required to optimize processing parameters in low-temperature heat treatments (e.g. tempering, stress relief) by focusing on the following topics:
- Operation
- Design Features and Performance
- Temperature uniformity
- Control issues (vacuum, partial pressure, positive pressure)
- Heating and cooling rates
- Utility consumption
- Materials of construction
- Applications
- Temperatures
- Materials
- Processes
- Industries
- Unique Features
- Quality
- Clean & Bright work
- Environmentally Friendly Processing
- Safety
- Lean Manufacturing
- Application Areas
- Vacuum Designs
- Performance Capabilities / Requirements
How They Operate
Low-temperature processing can be batch or continuous, either as stand-alone units or “modules” incorporated into a continuous vacuum furnace system. The following is a basic description of the operation of a typical batch vacuum furnace (Fig. 1).
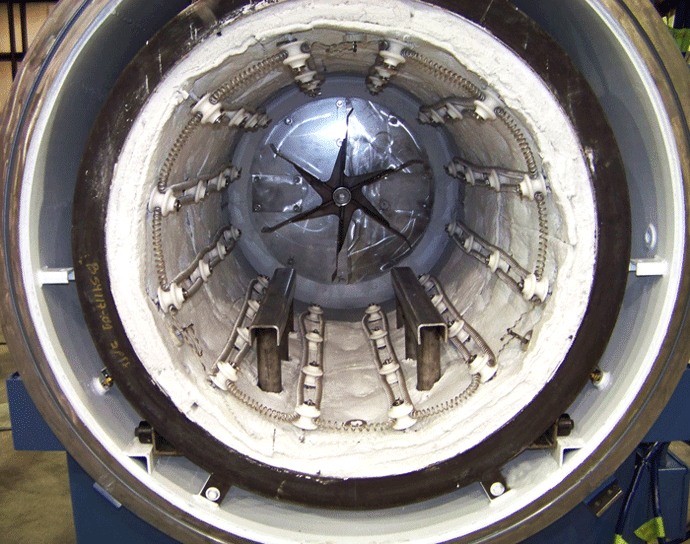
Once a workload has been positioned into the unit, an outer door is closed and the vacuum process can commence. A mechanical vacuum pump, optionally equipped with a blower, produces a vacuum level as low as 1.3 x 10-3 mbar (1 x 10-3torr), a common vacuum level being under 1.3 x 10-1 mbar (1 x 10-1 torr). This is normally achieved in 10 – 20 minutes depending on the size of the pumping system and the nature of any contamination present on the workload. In some instances, a double pump-down sequence is initiated once an initial vacuum level lower than 6.7 x 10-1 mbar (5 x 10-1 torr) is reached.
Once the desired final vacuum level is reached, the unit is backfilled in the range of 667 mbar (500 torr) to 3.4 x 10-2 bar (0.5 psig) positive pressure with an inert gas such as nitrogen, argon or nitrogen/hydrogen (3% maximum) and heating begins. After reaching setpoint and soaking at temperature, a cooling cycle is initiated, typically with hot gases circulated through an internal or external heat exchanger to accelerate the process.
Design Features and Performance
Heating elements are typically positioned either on the sides of the workload or in a 360º pattern around the workload and designed to allow for rapid heating (Fig. 2) and to achieve tight temperature uniformity (Table 1). A circulating fan is provided to aid in uniformity and provide for even distribution of process gas through the workload.
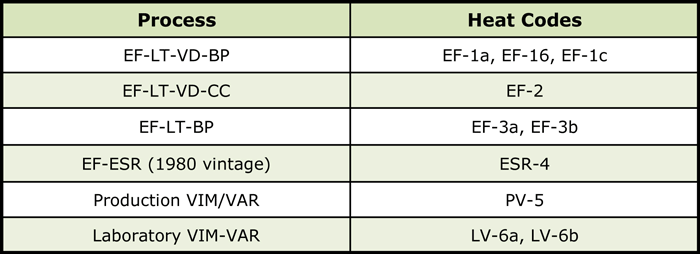
The materials of construction of the heating chamber are typically such that the furnace can be opened and unloaded hot at any required temperature. In most cases, however, surface condition is important and the workload must be cooled to at least 150°C (300°F) before unloading and more commonly to below 65°C (150°F) as measured by a thermocouple positioned in the workload itself. This makes the speed of cooling (Fig. 3) equality important.
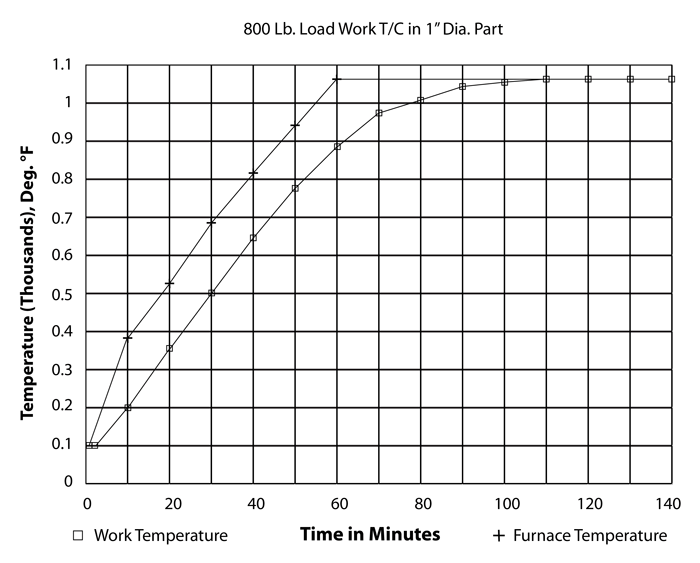
Common workload sizes range from 0.05 m3 – 0.35 m3 (2 – 12 ft3) for smaller units with payloads up to 550 kg (1200 lbs.) to larger units with workload sizes in the 1.0 – 1.5 m3 (36 – 54ft3) and capacities in the 450 – 2500 kg (1000 – 5500 lbs.) range. Typical workloads for these sizes are between 150 – 400 kg (300 – 900 lbs.) and 680 – 1360 kg (1500 – 3000 lbs.).
Positive pressure capability, up to 1.37 x 10-1 bar (2 psig) during both heating and cooling is possible with 3.4 x 10-2 bar (0.5 psig) being the most common positive pressure used.
Applications
Applications vary widely as do materials treated and process temperatures used. A survey of vacuum tempering users provided the following insights.
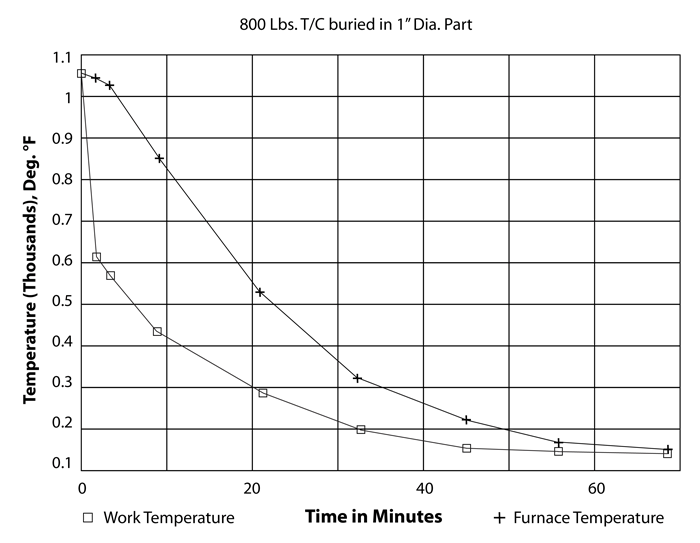
The most common processing temperatures can be expressed as Minimum and Maximum Temperature. Most units being manufactured today have operational ranges from 120°C (250°F) to 800°C (1450°F). Special applications extended this temperature range to as high as 925°C (1700°F), but this was unusual.
Most Common Processing Temperatures. Most processing temperatures were reported to be in the range of 175°C – 730°C (350°F – 1350°F). with the most common processing range being from 315°C (600°F) to 650°C (1200°F).
The most common low-temperature vacuum processes include:
- Aging;
- Annealing;
- Oxidizing;
- Stress relief;
- Tempering.
Typical materials may be categorized as, but not limited to:
- Alloy and high carbon steels (including maraging grades)
- Beryllium copper and beryllium nickel;
- Brass;
- Copper;
- Inconel;
- Specialty alloys (Elgiloy, NiSpan C, Nitralloy);
- Stainless steels (including precipitation hardening grades);
- Titanium alloys;
- Tool steels.
Typical markets served included:
- Aerospace;
- Automotive;
- Commercial Heat Treating;
- Consumer Appliance;
- Electronics;
- Farm Implement;
- Government/Military/Defense;
- Housewares;
- Machine Tool;
- Tool & Die.
Parts processed varied widely and included such items as:
- Bearings, gears, and springs (Aerospace/Automotive/Consumer Appliance/Farm Implement)
- Bolts, nuts, and screws (Aerospace)
- Coining dies (Government)
- Relays, switches, and shielding components (Automotive/Electronics/Military/Defense)
- Tooling, tool holders, dies, and taps (Machine Tool/Tool & Die)
Why Vacuum?
Low-temperature vacuum processing is often referred to generically as “vacuum tempering”, places the component parts in a controlled heat treat environment designed to optimize part quality. Surface condition, productivity, choice of atmosphere, and absolute control of process and equipment variability are superior to alternative technologies. Cost, both initial and operational, is often offset by a reduction in scrap rates, elimination of work in process inventories and lower energy consumption.
Low-temperature vacuum processing is synonymous with these key features:
Quality Assurance. Vacuum processing guarantees quality standards will be achieved, especially as they relate to surface condition; process repeatability; control, the ability to predict results, monitoring of key variables in real time, and automated cycles. For example, vacuum heat treatment of tool steels provides positive process adherence, a “two plus two” temper achieves part cooling below 65ºC (150ºF) before initiation of the second heating cycle.
“Clean and Bright” Work. In all cases, the surface condition of a component part is improved. Since “clean” and “bright” are subjective terms and difficult to define, we say instead that the part surface will not be metallurgically damaged and if a change occurs it is, generally speaking, a positive one.
Often parts are contaminated with oils from prior operations, such as stamping, or have water and/or alkaline wash compound residues, including marking dyes, shop dirt and other prior processing related contaminants. By the very nature of heat-treating in vacuum, these surface contaminants are removed. In some instances, oxide reduction can take place but in general vacuum levels are too high and temperature too low for this to be effective.
Environmentally Friendly Processing. Done properly, vacuum processing should have no impact on the environment. The only source of pollutants is the discharge from the vacuum pumping system, which meets current OSHA and EPA air quality and environmental standards. The byproducts should be water vapor and carbon dioxide. It is often recommended that the vacuum pump exhaust gets piped outside the plant, although in some instances this is not necessary. If discharge inside the factory is undesirable, special filters called oil-mist eliminators can be provided – these are always a good idea to include on any pumping system.
The problem with most non-vacuum processes related to the contaminants present on the parts. Burning oils off in a furnace or oven running in air or under an inert atmosphere and letting these fumes discharge either inside or outside the plant is no longer acceptable. Filters or afterburners to handle these discharges add cost to these systems. Thus cleaning prior to low-temperature processing is mandatory for both vacuum and air or atmosphere systems.
Safety. Vacuum systems are self-contained and present minimal safety hazards to operators or plant personnel. There are seldom concerns over noise levels, pinch points, electrical hazards, discharge of heat into the room, and there is no “burn off” or flames as with non-vacuum equipment.
Lean Manufacturing. Vacuum furnaces are ideal for manufacturing cells and fit well into today’s lean manufacturing environments. Vacuum temper furnaces can be provided either with hot or cold wall construction and combined with their quiet and pollution free operation makes incorporation onto the shop floor and integration into a manufacturing cell environment both practical and realistic.
Summary
Low-temperature vacuum tempering is becoming increasingly popular. The desires to avoid “post-mortem” quality methods as well as to assure process repeatability are key motivations. Designs capable of meeting these needs are available and perform well.
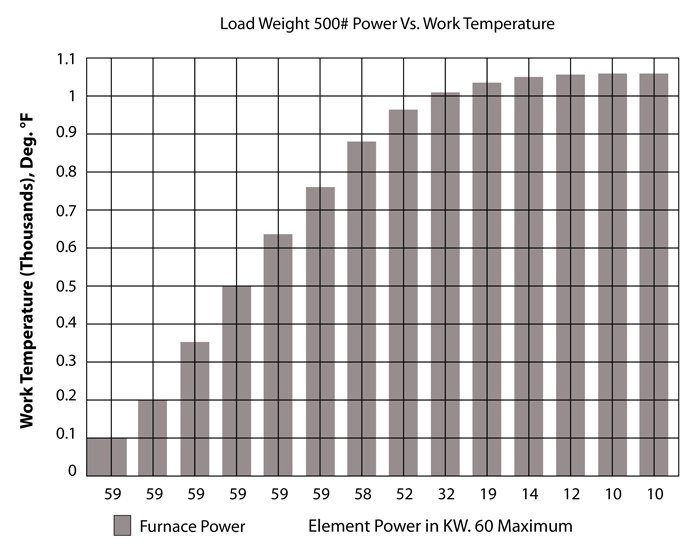
The key considerations in Low-temperature vacuum processing can be prioritized as follows:
- Vacuum heat-treating is considered mandatory for parts that must be processed without surface damage such as oxidation. Parts at all stages of manufacturing, not just finished parts will benefit from this treatment.
- High productivity and energy efficiency (Fig. 4) requirements are best achieved by vacuum processing. The ability to heat slightly more rapidly and especially cool much more rapidly in a positive pressure greatly reduces cycle time. Uniformity of heating and cooling add significant benefits.
- Minimum atmosphere consumption is achieved during vacuum processing. Once a backfill gas has been introduced into the chamber only small amounts of makeup gas is needed (typically during cooling as the gas contracts), Even in cases where gas flushing is required, far less atmosphere is used. Gas savings of as much as 10:1 have been reported.
- Process control is absolute including the ability to upload and download information in real time, including in many cased both process and equipment variables. This allows a more complete history to be maintained either for quality assurance or to allow planned preventative maintenance to occur.
Application Areas
Applications for this technology (Fig Nos. 5 & 6) vary widely but generally fall into the following categories:
- Aging;
- Annealing;
- Oxidizing/Bluing;
- Stress relief;
- Tempering.
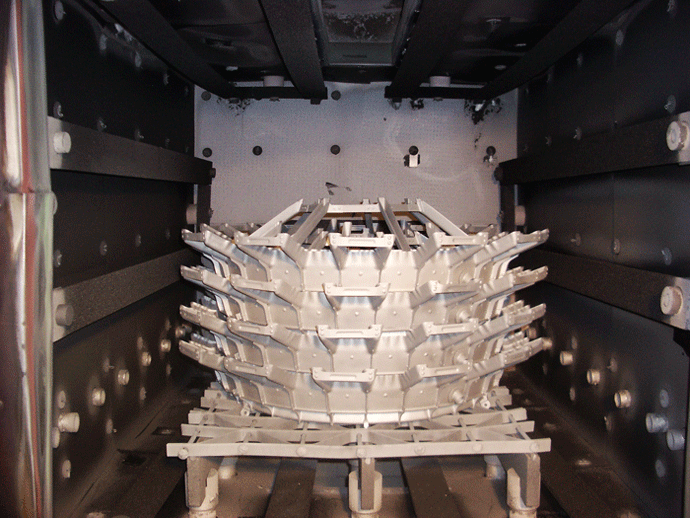
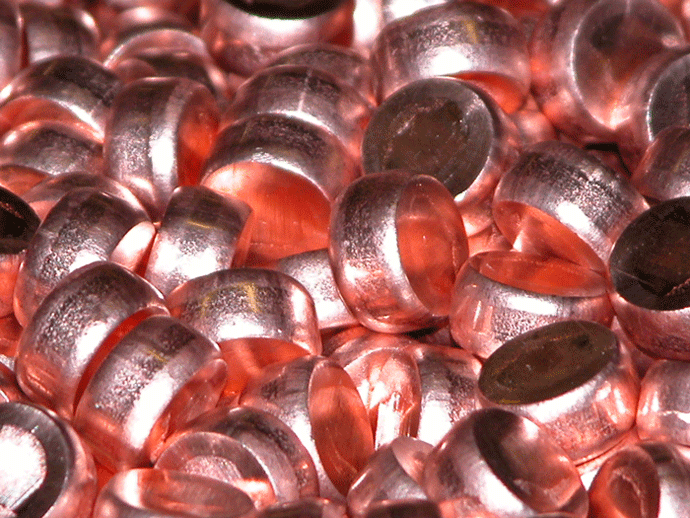
Typical materials include:
- Alloy and high carbon steels (including maraging grades);
- Beryllium copper and beryllium nickel;
- Brass;
- Copper;
- Inconel;
- Specialty alloys (Elgiloy®, NiSpan C, Nitralloy);
- Stainless steels, including precipitation hardening grades;
- Titanium alloys;
- Tool Steels.
Low-temperature vacuum heat treatment is used by both captive and commercial heat treaters and spans such diverse markets as Aerospace, Automotive, Electronics, Optics, Housewares, Industrial Products, Tool & Die, Military/Defense and Farm Implement to name a few.
![Table 1 - Field Data on Low Temperature Vacuum Furnace Uniformity [1] / Notes: a. Class 1 per ASM 2750 (Pyrometry)](https://vacaero.com/wp-content/uploads/2016/01/table-1_lg.gif)
Parts processed vary widely. Typical examples include:
- Bearing, gears, and springs
- Bolts, nuts, and screws
- Relays, switches and shielding components manufactured from stampings
- Tooling, tool holders, dies, and taps
Most processes run in the temperature range of 175°C – 730°C (350°F – 1350°F). Special applications extend these ranges down to as low as 120°C (250°F) and up to as high as 925°C (1700°F), but this is unusual. Temperature uniformity (Table 2) in dedicated furnaces is considered excellent throughout the standard temperature ranges listed.
It is also worth noting that clean and/or bright work is most often associated with this type of processing. Since “clean” and “bright” are very subjective terms and difficult to define in a universal way, we tend instead to say that the part surface is not metallurgically damaged and if a change occurs, it is generally a positive one. In all cases, the surface condition of the parts being processed is said to be improved.
Vacuum Designs
Vacuum furnaces for low-temperature processing can be batch (Fig. 7) or continuous, stand-alone, integrated into continuous vacuum furnace systems or a separate “module” incorporated into a cellular system.
The basic operation for a batch vacuum furnace is as follows. Mechanical vacuum pumps, optionally equipped with blowers, produce vacuum levels down to 1.3 x 10-3 mbar (0.001 torr) with 6.7 x 10-3 mbar (0.005 torr) common. This is normally achieved within 10 – 30 minutes of the start of cycle, depending on the size of the pumping systems and the nature of any contaminates present on the workload. The unit is then backfilled in the range of 66.7 x 101 mbar (500 torr) negative pressure to 0.10 bar (1.5 psig) positive pressure with an inert gas such as nitrogen, argon, or a mixture of nitrogen/hydrogen (3% hydrogen maximum) and heating begins. Double pumpdown cycles are often found to be advantageous to speed the overall cycle time. After reaching setpoint and soaking at temperature, the cooling cycle is initiated.
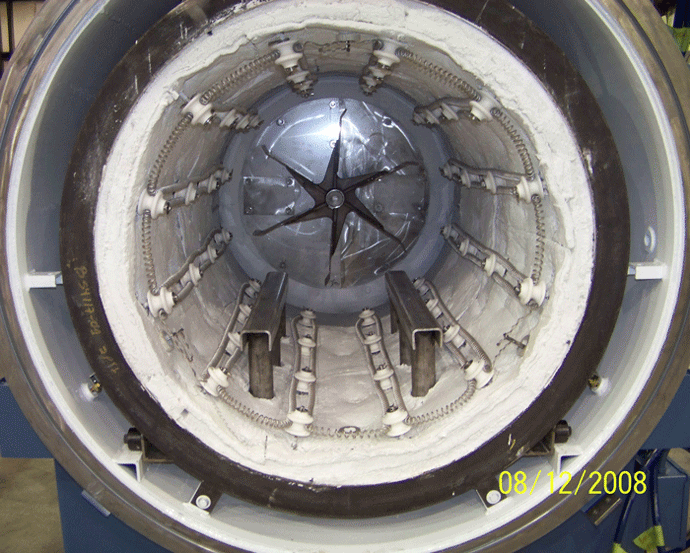
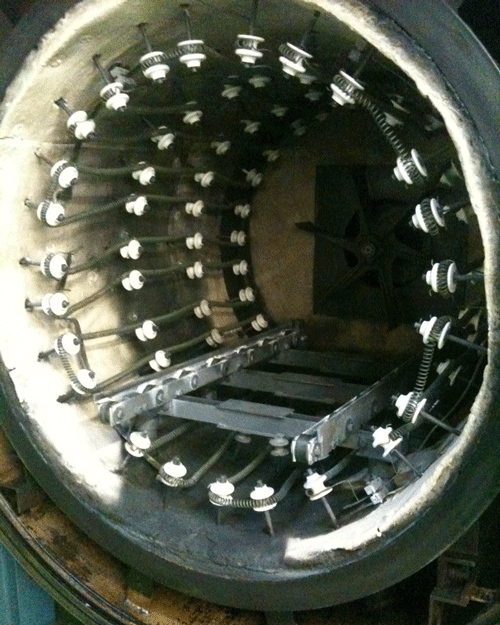
Often parts are contaminated with oils from prior operations such as stamping, or they have moisture or alkaline cleaning compound residues present on them. By the very nature of vacuum processing, many of these surface contaminates are vaporized off and deposit on the furnace interior (Fig. 8) or redeposit on the work during cooling. The Heat Treater must be aware these foreign contaminates will pass through the vacuum system, often degrading its performance negating the benefits of vacuum purging unless proper maintenance is performed. While most low-temperature vacuum processing units can tolerate a great deal of contamination, cleaning (and drying) the work thoroughly before processing is always recommended.
The materials of construction in the heating chamber are such that the furnace can be opened and unloaded at any required temperature. In most cases, however, surface condition is important and the workload must be cooled to at least 150°C (300°F) and more commonly to below 65°C (150°F) as measured by a thermocouple positioned in the workload itself. These units can be either gas-fired or electrically heated. Fiber insulation is typical, often in the form of a “hard pack” or rigidized so as to withstand the high velocities produced by the convection fan. These design features translate into rapid heat-up and cooldown rates (Fig Nos. 9 – 10).
![Figure 9 [1] Typical Heating Rate Performance Data](https://vacaero.com/wp-content/uploads/2018/06/fig-9.gif)
![Figure 10 [1] Typical Cooling Rate Performance Data](https://vacaero.com/wp-content/uploads/2018/06/fig-10.gif)
Performance Capabilities / Requirements
Since low-temperature processing in vacuum or vacuum purged vessels offers so many advantages, the question naturally arises, “What features are most desirable?” (Table 3). The answer often lies in knowing what the application requires and the performance benefits to be gained.
In Conclusion
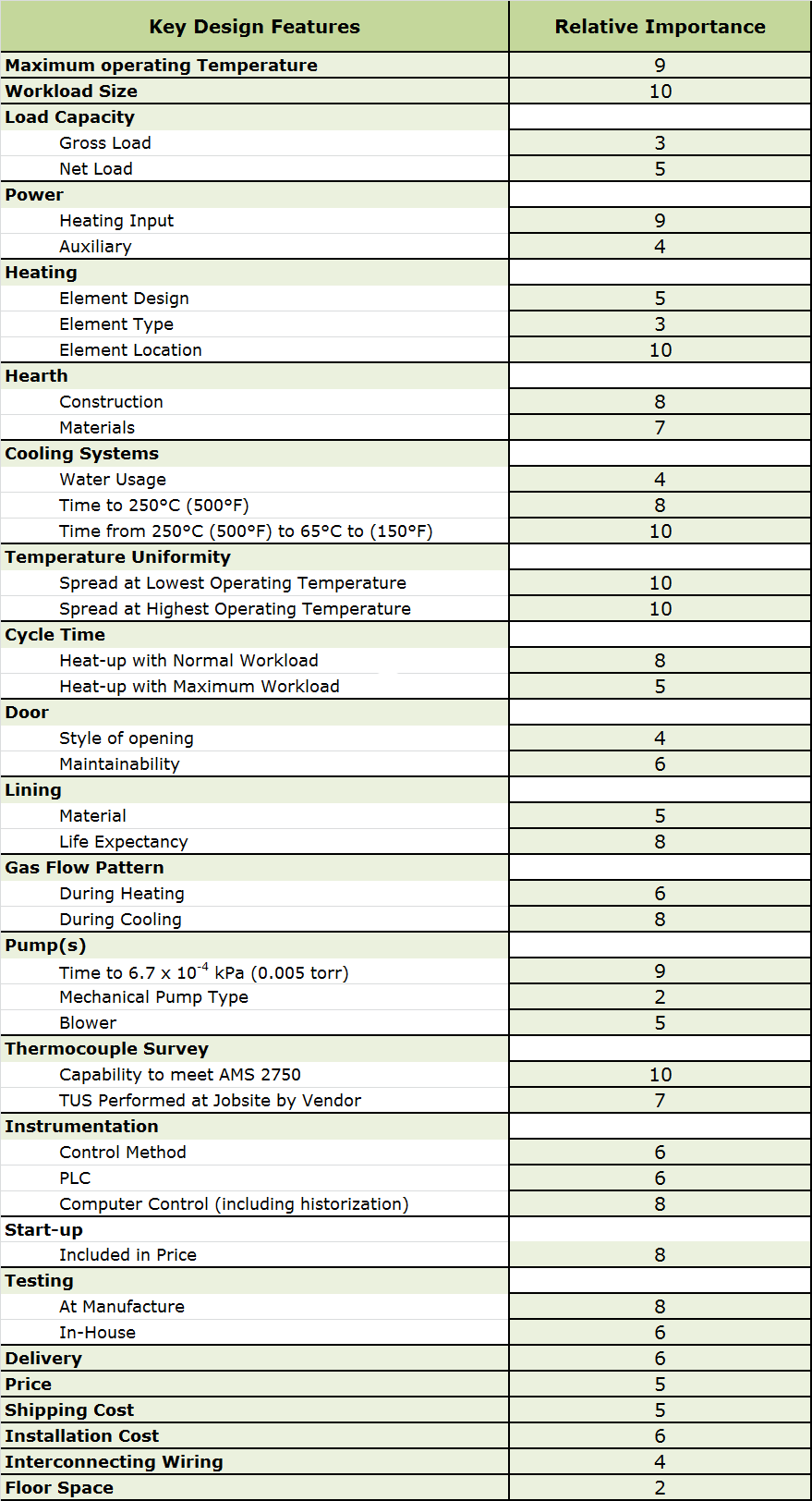
Low-temperature vacuum processing of workloads is becoming increasingly more common driven by a need for improved surface quality, better process repeatability, control of process and equipment variability and the ability to predict quality results. Designs capable of meeting these needs are available and perform well.
Some of the key considerations for choosing low-temperature vacuum processing can be summarized as:
- Mandatory for parts that must be processed without surface damage (e.g. oxidation). Parts at all stages of the manufacturing process, not just finished surfaces benefit from this type of treatment.
- Uniformity and speed of heating and cooling with minimum energy consumption.
- High productivity requirements are best achieved by vacuum processing. The ability to heat slightly more rapidly and, especially, to cool much more rapidly in a positive pressure reduces cycle time. Gas fired equipment is especially beneficial in this regard.
- Minimum atmosphere consumption. Once partial pressure or backfill gas is introduced, only small amounts of make-up gas are needed. Even in cases where repeated gas flushing is required, far less atmosphere is needed.
- Process control is absolute including the ability to upload recipes and download process and equipment variables in real time. Planned preventative maintenance practices and a complete history are simple and straightforward.
References
Herring, D. H., Low-Temperature Vacuum Heat Treating, ASM Heat Treating Conference, 1997.