The type and reliability of instrumentation and process controls used on vacuum furnaces in the heat treatment industry (Fig. 1) is critical to both the performance of the vacuum furnace itself as well as the results that are achieved when processing critical components. It is not an understatement to say that given the life expectancy of vacuum equipment, instrumentation and controls should be updated every few years to take advantage of the most advanced technology possible (e.g., remote communication and diagnostics, process monitoring and control by Internet-based devices and the like).
Demands on Instrumentation and Control Packages
Temperature control and as a result temperature uniformity can be difficult because of the heat transfer characteristics of the furnace as it moves, for example, from convection to radiant heating and convective/conductive heat transfer during quenching. For example, the ability to vary the furnace heating rate (e.g., 3°C/min – 25°C/min) demands precise and accurate measurement and control, including setpoint program control with guaranteed soak features.
Vacuum furnaces are often used for a variety of products and processes by the heat treater making recipe management an important function. Temperature overshoot of set points is typically not allowed. Setpoint program control is often applied to the temperature, vacuum level and gas pressure with extensive interaction between these programs and also with the logic control.
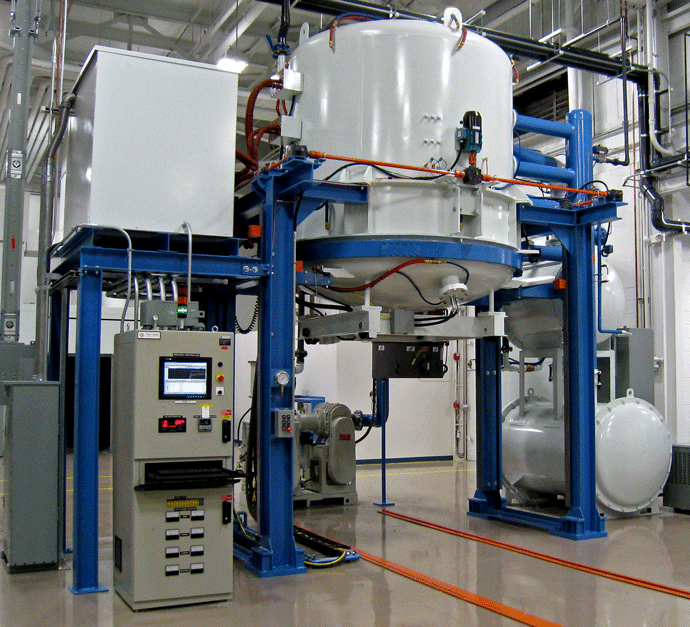
Given the tremendous application diversity of vacuum furnaces (e.g., annealing, brazing, case hardening, diffusion bonding, hardening, melting, tempering, thin film deposition) and the need to process these materials over a broad range of temperature, typically with no surface reaction (e.g. oxidation) makes the instrumentation package choice even more demanding, diverse and complex. Whether running at partial pressure to prevent vaporization of various elements present in the material, or at over pressure to improve low-temperature uniformity, process control (temperature, vacuum) is mandatory. In addition, surface and internal contaminants present on the material surface are often volatized and removed prior to high-temperature processing making the control of heating and the method of expulsion of these unwanted products part of the requirements of the process control system.
Process Example
Vacuum furnaces for heat treating and brazing are typically single chamber furnaces operating batch cycles. The batch cycles vary between processes but commonly require regulation of temperature, vacuum and sequence logic. The temperature and vacuum interact extensively with the logic.
A typical heat-treating cycle starts after the product is loaded into the furnace and the door is clamped shut. Some users secure the furnace and perform a leak test before proceeding. A roughing vacuum pump lowers the pressure to about 0.05 torr (50 microns). An optional diffusion pump can lower the pressure to below 1 x 10-3 torr (1 micron). Some processes require an inert gas such as argon to be fed into the furnace at a low flow rate, allowing the pressure to rise to about 0.50 torr (500 microns) or higher – this is part of the partial pressure control devices.
The pressure increases as the temperature rises and contaminants volatilize. Control of the vacuum is maintained at about 0.50 torr (500 microns) in partial pressure processes or below 10-4 torr in high vacuum processes. If the vacuum deviates from the specific set point by more than a specific value, the temperature program is held until the condition is corrected. The temperature program goes through a series of ramps and soaks. After a high-temperature soak, the quench process activates, and the temperature is allowed to drop. An increased flow of inert gas (e.g., nitrogen, argon, helium) and circulation of cooling water in the furnace walls and heat exchanger cools the work. The cooling lowers furnace pressure, requiring additional pressure control. During the cooling, the pressure is typically controlled between 0.85 bar to 10 bar depending on process type. A light or horn usually activates as an indication to the operator that the cycle is complete. The operator then brings the furnace back to atmospheric pressure manually and unloads the product.
Control Implementation
Over the last 40 – 50 years of vacuum furnace manufacturers have used many different hardware platforms for equipment and process control. A common platform is based on the Honeywell HC900 hybrid controller together with Experion HS R500 SCADA software. Features of this package can be described as follows:
Features of the Honeywell HC900 Experion HS R500 Process Control
The HC900 Hybrid Controller combined with Experion HS R500 interface (Fig. 2) is designed for efficient, safe and productive use on vacuum equipment with maximum operator convenience. Some of its abilities include:
- Program control of sequencing and variables versus time
- Proportional (PID) modulating loop control
- Logic functions for equipment and process status
- Alarm detection, annunciation, and logging
- Data acquisition and data logging
- Recipe configuration, local storage, and download capability
- Easily programmable by operators in engineering units.
- Sixteen (16) programmable events for integration with sequence control functions.
- Alarms and events may be programmed to send an e-mail message.
- Modbus/TCP protocol allows interfacing to HMI, data acquisition and OPC server software.
- Ethernet port supports direct PC connection or external Modem connection for configuration upload, download, and maintenance.
- Isolated, universal analog inputs allow a mix of analog input types on the same card, saving I/O cost
- Auto tuning and fuzzy overshoot protection for quick start-up and proper control operation
- Storage of up to 1000 recipes for fast, error-free product selection
- Storage of up to 1000 time/temperature profiles. Each profile may be part of a recipe.
- Any HC900 can support up to 8 peer controllers for the exchange of analog or digital data over Ethernet.
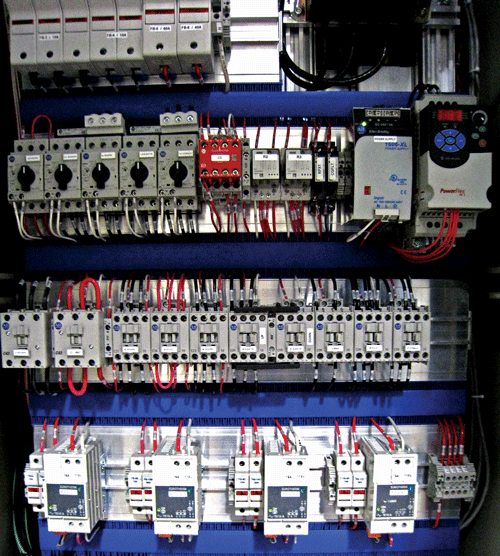
Vacuum Furnace Control System Example
Control of temperature is executed with an internal algorithm set capable of handling most application requirements. Multiple tuning constants may be used to tailor the control response to the dynamic characteristics of the furnace.
Approach limits allow maximum heating rates without overshoot, reducing cycle time and optimizing efficiency. The HC900 integrates the setpoint programmer, loop and logic functions within a single device. The Setpoint Program capability of the HC900 is used to control the temperature profiles with up to 1000 different profiles appropriate for a wide range of products, can be created and stored for use when these products are processed.
A typical heat-treat cycle profile (Fig. 3) uses load guarantee soak function (as event 7) to control critical soak temperature. The cycle profile also contains other events used to control diverse functions required by a heat treatment cycle (high and low vacuum level, partial pressure, quench, etc.).
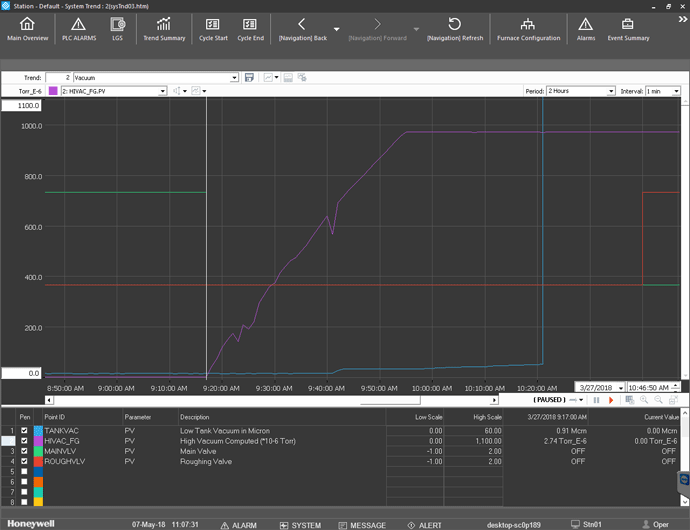
A single configurable database integrates both the loop (proportional, modulating) functions and the logic (discrete, Boolean) functions required by the process. User-friendly operator displays provide the operator with dynamic information about the status of each run as it progresses. Alarms are announced in color on dedicated displays and can be acknowledged directly from the operator interface.
The data acquisition and control capability of the HC900 permits ongoing process analysis to define and implement the various control strategies.
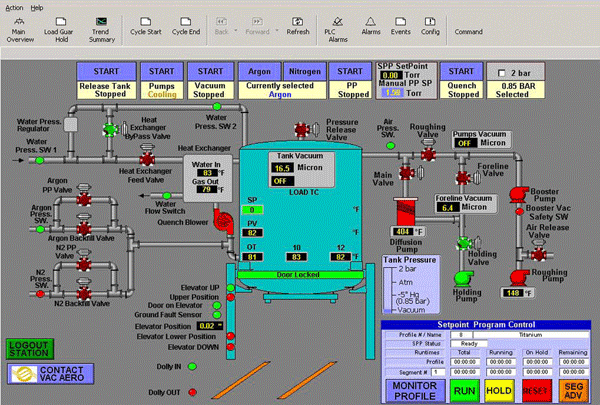
Implementation
The HC900 is a panel-mounted controller connected to a computer-based operator interface. All field signals terminate at the controller. The controller has universal analog inputs, analog outputs and a wide variety of digital input and output types. This controller will provide all the vacuum furnace control functions.
Configuration
The Hybrid Control Designer tool (Fig. 4) provides advanced configuration techniques that allow for a variety of strategies to be easily implemented. The run-mode configuration monitoring and editing capability allow these strategies to be tested and refined as process knowledge is gained.
Monitoring
The complete operation can be monitored and controlled from the display screens. Standard and customized displays make it simple for operators to learn and use the system (Fig. Nos. 5 – 9).
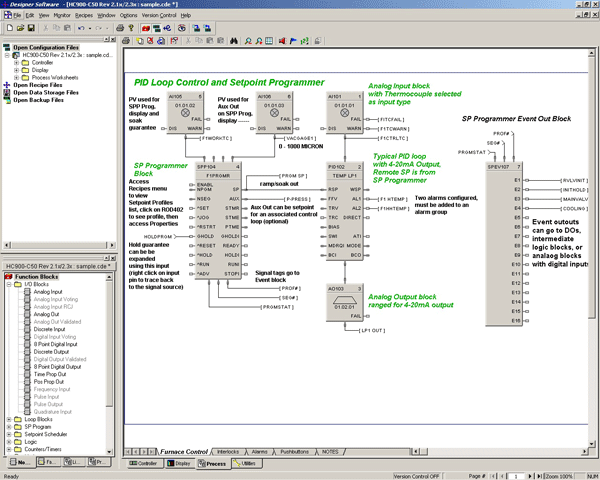
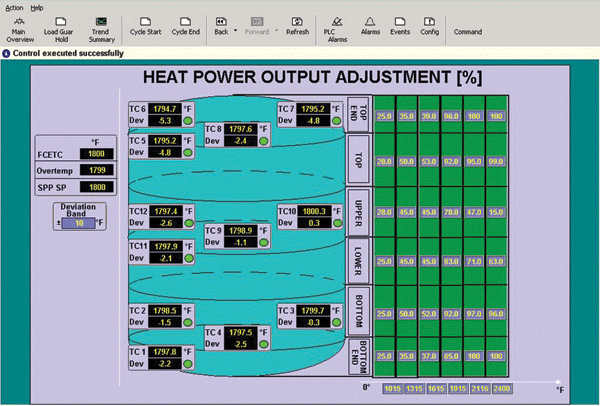
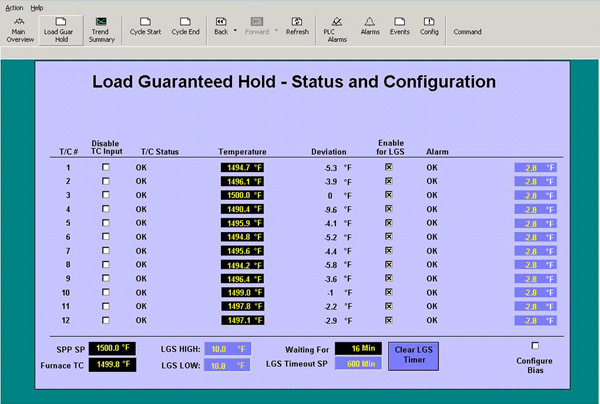
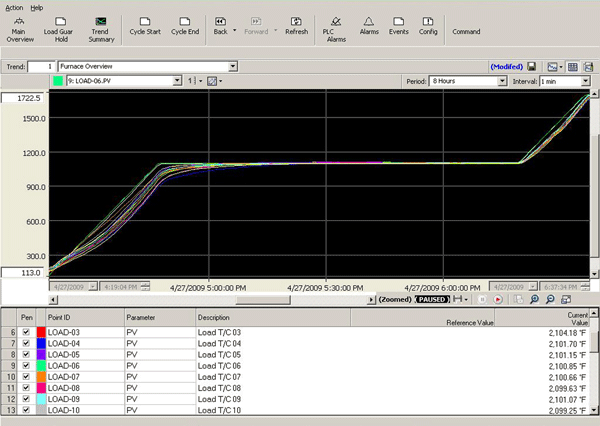
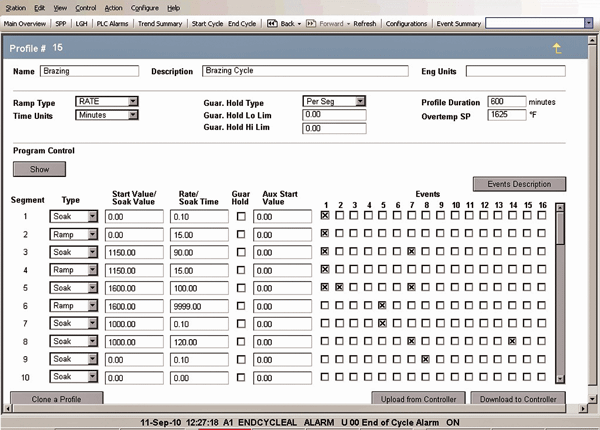
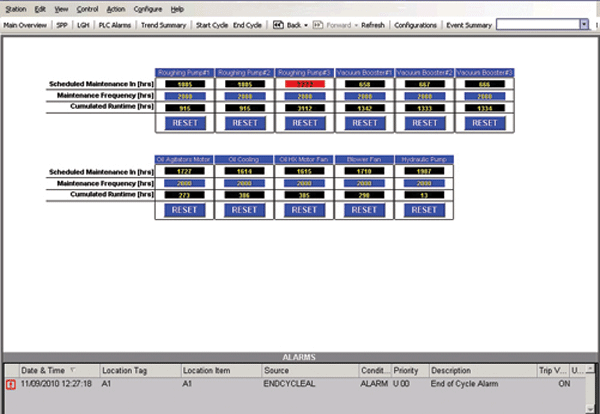
Data Collection and Storage.
Data collection and storage is handled within the supervisory system and includes a variety of reporting functions. Some of these include:
- Alarm / Event Log reports all alarms and events in a specified time period.
- Alarm Duration Log reports the time of occurrence and elapsed time before return-to-normal for specific alarms in a specified time period.
- Alarm Pager (optional). Setpoint alarms may be sent to an alarm paging or messaging system.
- Integrated Excel reporting provides the ability to launch a report built using Microsoft Excel.
- Batch reports collect history for points and events that occurred during a process production run. Static batch data may also be added to the report such as batch number, customer name, lot size, etc.
- Bar-coded data functionality may be used to enter batch information.
- Reports may be generated periodically, or on an event-driven or demand basis. Report output may be directed to screen, printer, file, or directly to another computer for analysis or viewing electronically.
- History collection is available over a wide range of frequencies in both average and snapshot/production formats. A large amount of history can be retained on line, with automatic archiving allowing retention of and access to unlimited quantities of historical data.
- Flexible trend configuration allows trends to be configured. Real-time and historical data are presented together on the same trend.
- The data storage feature can be used to log process information during the cycle to an internal hard drive disk or to a plant network storage device for a permanent record.
Alarm Functions
The software has been optimized to anticipate all normal operating and alarm conditions. The software also provides Supervisory Control and Data Acquisition (SCADA) using a touch screen LCD for operator interface for features such as:
- Compatibility with plant-wide SCADA and network integration.
- Process cycle validation.
- Extensive alarm and event management and reporting.
- Temperature control using advanced algorithms, auto-tuning, and multiple zone digital trimming.
- Operator sign-on/sign-off security to limit operator control of individual functions.
- Enhanced maintenance and troubleshooting management.
- Extensive set of advanced algorithms for maximum process performance
- Open Ethernet connectivity via Modbus/TCP protocol that provides plant-wide process access and data acquisition
- Extensive equipment diagnostic and monitoring to maximize process availability
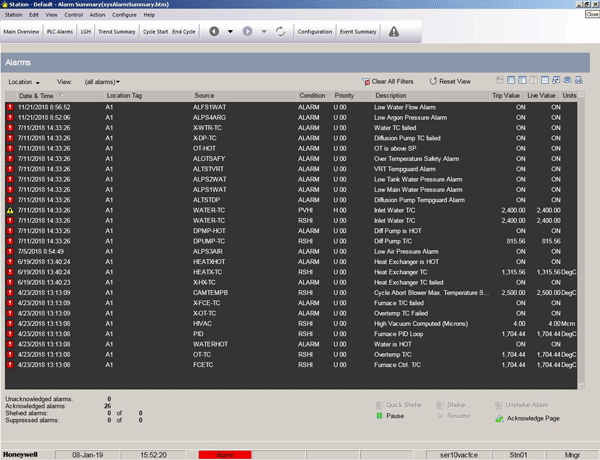
Summary
The Honeywell HC900 control system is a good example of a highly flexible instrumentation and process control package capable of being used out on the shop floor and numerous systems are currently operating in the field. Whatever your choice of instrumentation and process controls, it is important that the system be flexible, expandable and designed for future integration with software and hardware platforms that have yet to be conceived. Stay current with the latest innovations so that your vacuum equipment provides your customers with the best possible products.