There is a constant need throughout the industry to produce the highest quality parts to the most stringent product specifications. Both long-established and new materials are being employed to meet the needs of lighter, stronger, smaller and more efficient designs, and the use of vacuum technology in manufacturing is of paramount importance in achieving these goals.
The strategy being adopted by manufacturing to meet these needs relies heavily on vacuum processes and equipment through:
- Process development – New materials, new products, and new applications demand absolute cycle repeatability, flexibility, and control, and as such, designers are specifying vacuum processing over other heat treatment methods.
- Process substitution – Older process technologies and the equipment associated with them are being replaced by vacuum equipment. The justification lies in reduced unit cost achieved by lowering the overall cost of manufacturing and/or through material and efficiency savings.
- Process replacement – Product-performance demands are forcing designers to look toward vacuum processing and its ability to offer a superior product for the same or very similar cost.
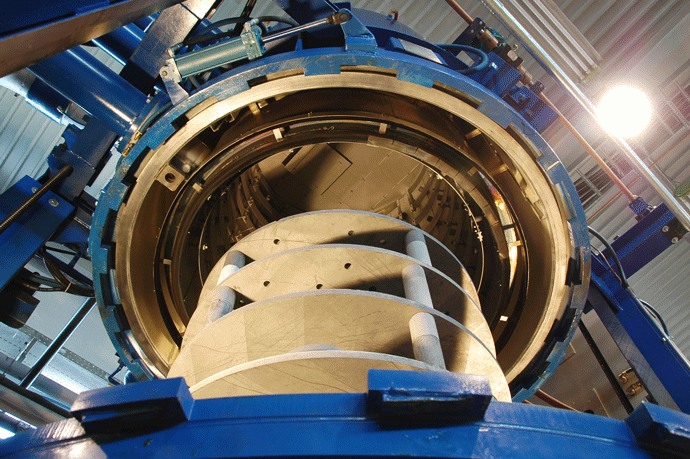
Typical processes performed in vacuum furnaces, by industry, include but aren’t limited to:
- Aerospace – engine, landing gear, etc.
- Age Hardening
- Brazing
- Carburizing
- Casting/melting
- Coating
- Hardening
- Solution treating
- Automotive – passenger and commercial vehicles
- Brazing
- Hardening
- Carburizing/carbonitriding
- Tempering
- Industrial products – appliance, tool & die, etc.
- Annealing
- Brazing
- Carburizing/carbonitriding
- Hardening
- Normalizing
- Sintering
- Tempering
- Commercial heat treating – outsourcing
- Annealing
- Brazing
- Carburizing/carbonitriding
- Hardening
- Nitriding/nitrocarburizing
- Normalizing
- Sintering
- Solution treating
- Stress relief
- Tempering (bright)
A few of the many types of materials being processed in vacuum include:
- Brass*, bronze, beryllium copper (e.g. marine industry)
- Carbon and alloy steels (e.g., automotive industry)
- Ceramics (e.g., nuclear, biomedical, astronautics industries)
- Iron and steel castings (e.g., oil & gas industry)
- Stainless Steels (e.g., food industry)
- Tool Steels (e.g. tool & die industry)
- Nickel Alloys – Inconel, specialty grades (e.g., chemical, electronics industries)
- Powder metallurgy grades – aluminum, steel, stainless steel, tool steels, tungsten carbide (e.g., automotive and tool industries)
- Copper and copper alloys (e.g. consumer electronics industry)
- Superalloys – iron, nickel and cobalt-based (e.g., aerospace industry)
- Tantalum (e.g., electronics industry)
- Titanium and titanium alloys (e.g. aerospace, medical industries)
- Zirconium alloys (e.g., nuclear industry)
* Note: Special precautions are needed to prevent dezincification of these alloys
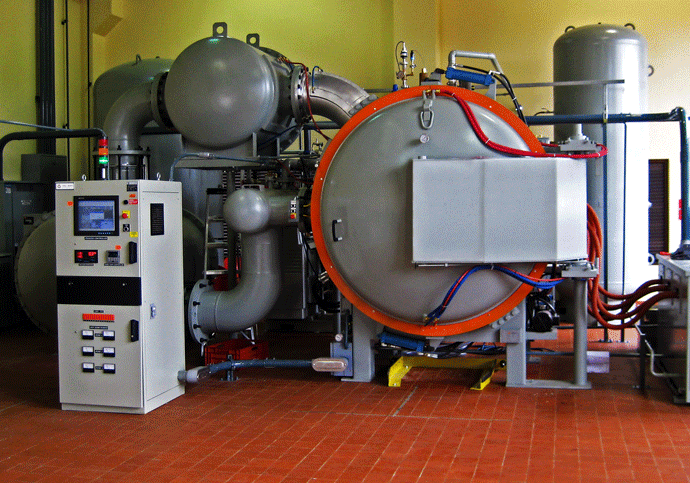
Common Vacuum Heat Treatment Processes4
Some of the most common heat treatment processes run in a vacuum are outlined below along with a brief explanation of the advantages that vacuum treating provides.
Annealing
Annealing treatments are undertaken primarily to soften a material, to relieve internal stresses and/or to modify the grain structure. These operations are carried out by heating to the required temperature followed by soaking at this temperature for sufficient time to allow the material to stabilize followed by slow cooling (except for solution annealing) at a slow and often times controlled rate. The choice of vacuum annealing is primarily influenced by the cleanliness and high quality of surface finish that can be obtained relatively easily compared to other controlled atmosphere heat treatment operations.
Brazing
Vacuum brazing represents one of the growing uses for vacuum furnaces. Tight process (time/temperature) control and the possibility of a metallurgical clean joint at the onset of brazing are attractive attributes. The transportation industry (e.g. automotive and aerospace), in particular, has provided the impetus for increasing demand for vacuum furnace brazing,. In addition, the gain in popularity of lightweight, high-strength materials has also contributed to the popularity of vacuum brazing.
Vacuum furnace designs used for the brazing process can be either horizontal or vertical in design and offer the following technical advantages:
- The process permits brazing of complex, dense assemblies with blind passages that would be almost impossible to braze and adequately clean using atmospheric flux brazing techniques.
- Vacuum furnaces using diffusion pumps to achieve vacuum levels of 10-4 to 10-5 Torr remove essentially all gases that could inhibit the flow of brazing alloy, prevent the development of tenacious oxide films, and promote the wetting and flow of the braze alloy over the vacuum conditioned surfaces.
- Properly processed parts are unloaded in a clean and bright condition often avoiding additional processing.
- A wide variety of materials ranging from aluminum, cast irons, stainless steel, steels, titanium alloys, nickel alloys, and cobalt-base superalloys are brazed successfully in vacuum furnaces without the use of any flux.
Carburizing/Carbonitriding
Carburizing/carbonitriding are specialized case hardening processes performed on gears and many other industrial parts. The process has gained popularity in vacuum furnaces given its ability to precisely control surface hardness and case depth. Quenching is done in either oil or high-pressure gas (up to 25 bar nitrogen being a practical limit).
The case depth on a component surface is a function of the rate of carbon absorption at the surface and the diffusion of carbon away from the surface and into the material. Once a high concentration of carbon has developed on the surface, during what is commonly called the “boost stage”, the process normally introduces a “diffuse stage” whereby the surface carbon concentration is reduced by diffusion into the interior. The result is a reduction of the carbon concentration at the surface while increasing the depth of carbon absorption.
In the carburization process, residual compressive stresses result from the delayed transformation and volume expansion of the carbon-enriched surface. This induces the desirable residual compressive stress through the case-hardened layer.
Hardening
Hardening of steel and other alloys is advantageous in vacuum furnaces where surface oxidation in the form of intergranular oxidation/intergranular attack (IGO/IGA) and surface contamination needs to be avoided. The time/temperature recipes can include controlled ramp rates, single or multiple preheats (common in tool steel hardening, for example) and variable soak times based either on workload thermocouples or time. Quenching can be done in either oil or high-pressure gas (up to 25 bar nitrogen being a practical limit) and isothermal holds are possible as well.
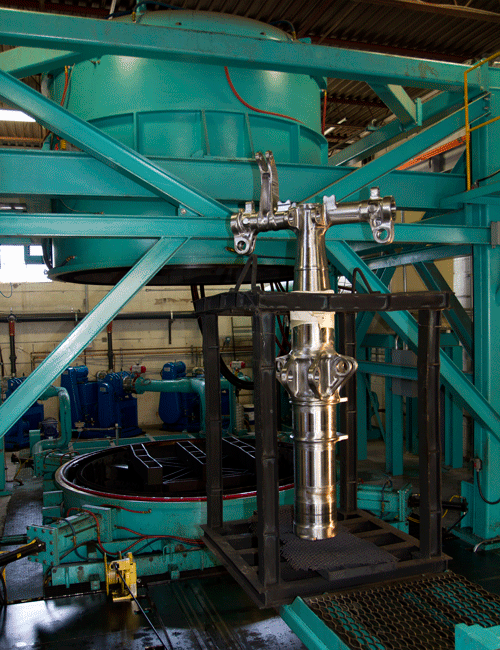
Sintering, Sinter Compaction, MIM and Additive Manufacturing
Vacuum sintering, compaction (CIP, HIP). MIM and secondary heat treatment operations are performed on both conventional powder metal (PM) as well as particulate (CIM, PIM, MIM) materials. In an industry dominated by atmosphere processing, increased interest in controlled vacuum sintering arises from factors such as:
- The purity of the vacuum environment and its effect on part microstructure.
- The use of sub-atmospheric (partial) pressure to improve the efficiency of the sintering reactions especially with highly alloyed materials that require elevated sintering temperatures.
- The use of reducing gasses, at temperatures typically less than 500°C (930°F), aid in binder removal, reduce porosity and minimize oxide formation.
- The ability of the vacuum process to reduce pore size and improve pore size distribution.
- The higher furnace temperature capabilities that permit faster sintering reactions carried out much closer to the melting point and with alloys of higher melting point interstitial elements or liquid phase metal sintering itself.
- The ability to modify, in-situ, carbon balance and affect carbon additions or reductions.
- The use of over-press sintering (HIP) to densify the materials, close type porosity without the formation of alloy rich areas.
- Single-cycle debind, sinter & HIP with rapid cooling for rapid floor-to-floor times.
The limitation on the application of sintering in vacuum furnaces is binder removal and the vapor pressure of the metals being processed at the chosen sintering temperature. If the vapor pressure is comparable with the working pressure in the vacuum furnace, there will be considerable loss of metal by vaporization unless a sufficiently high partial pressure of inert gas is used. In certain situations, care must be taken as the partial pressure gas selected may react with the surface of the part creating an undesirable surface layer or condition.
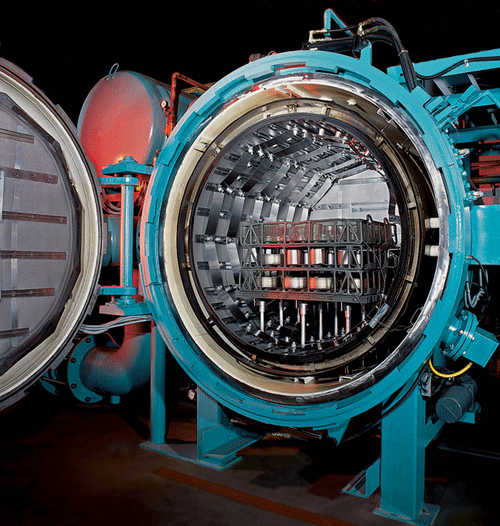
Solution Treating and Aging5
Solution treatment is the heating of an alloy to a suitable temperature, holding it at that temperature long enough to cause one or more constituents to enter into a solid solution and then cooling it rapidly enough to hold these constituents in solution. Subsequent aging (i.e., precipitation) heat treatment allows the controlled precipitation of these constituents either naturally (at room temperature) or artificially (at higher temperatures).
Many aerospace applications requiring high tensile strength, high fatigue strength, and good stress-rupture properties use a solution treatment and a one or two-step aging treatment. Inconel® 718 is one example of a material that is usually used in the solution treated and aged condition. The exact temperatures, times, and cooling rates depend on the application and desired mechanical properties.
Another example involves solid-solution strengthened alloys (e.g., Hastelloy® X, Inconel® 625 and HA® 230) in which work hardening from manufacturing operations limits the ability to further process the material. As such, in-process solution treating (i.e., stress relief) reduces this condition and allows additional processing. In addition, manufacturing processes, such as brazing, welding or coating can have an undesirable impact on material properties which may be reversed through solution treating prior to further downstream processing. Finally, various manufacturing processes may result in the premature start of the final precipitation age hardening process, which can be reversed through re-solution treating prior to further processing.
Age hardening results in the development of final material properties. Typically, this step is performed at or near the end of the manufacturing process, as the heat treat process results in a significant increase in material hardness, and there is a predictable amount of size change that occurs (shrinkage) that must be accounted for.
Tempering (“bright”)
Where surface finish is critical and “clean and bright” parts are desired to avoid any post heat treat processing, many heat treaters, especially commercial shops, now employ vacuum furnaces for tempering and stress relief. These units typically operate in the temperature range of 130°C – 675°C (275°F – 1250°F), which is below the temperature at which radiant energy is an efficient method for heating. As such, heating by convection is utilized; the furnace is normally evacuated to below 0.10 mbar (0.075 Torr), then backfilled with an inert gas such as nitrogen, argon or even 97% nitrogen / 3% hydrogen mixtures to a pressure slightly above atmospheric, typically in the range of 0.5 – 2 bar. A fan in the furnace recirculates this atmosphere, and parts are heated by both convection and conduction. Temperature uniformity in the range of ± 5°C (± 10°F) is common with tighter uniformities possible.
The advantages of processing in vacuum including some of the materials and common processes have been discussed above. We will now continue with a look at custom heat treatment processes conducted in vacuum furnaces including vacuum applications in the laboratory, Research & Development department and for light industrial requirements as well as a look at the future of vacuum processing.
Custom Heat Treatment Processes
There are many types of highly specialized processes that can be run in vacuum furnaces, and most are highly application specific. Some of these include:
Chemical Conversion
One of the applications not commonly considered in vacuum processing is that of chemical conversion. The sample material is loaded in non-reactive trays and placed inside the vacuum furnace or inside a retort (graphite or alloy). The material is then thermally processed under controlled temperatures and pressures to chemically convert a mixture of elemental materials into a compound. A typical chemical conversion process is run at 1370ºC (2500ºF) and requires up to several days for full transformation.
Creep and Compression Forming
Creep forming (aka hot sizing) is often used to flatten or form to a near-net shape and for correcting spring-back and/or inaccuracies in shape and dimensions of preformed parts. The part is suitably fixtured such that controlled pressure is applied to certain areas of the part during heating. This fixtured unit is then placed in a furnace and heated at temperatures and times sufficient to cause the metal to creep under its own weight until it conforms to the desired shape. Creep forming is done, for example, on titanium alloys, often in conjunction with compression forming.
Degassing
Vacuum degassing is a term often used to describe improved cleanliness in the steelmaking process. However, it is also used to reduce the hydrogen levels in many alloys such as titanium, tantalum, and niobium to avoid concerns over hydrogen assisted cracking (aka hydrogen embrittlement). Hydrogen is imparted into titanium during ingot, rolling and forging operations and can also be diffused into titanium during pickling or other chemical processes. Newer aerospace specifications demand that the hydrogen levels be no greater than 70 ppm. Vacuum degassing usually performed between 535°C – 790°C (1000°F – 1450°F) depending on the alloy, can achieve hydrogen levels of less than 20 ppm.
Homogenization
Vacuum homogenization is performed primarily to eliminate or decrease chemical segregation by thermal diffusion in castings and ingots (prior to hot working). Homogenization typically has one or more purposes depending on the alloy, product and fabricating process involved. For example, one of the principal objectives is improved workability since the microstructure of most alloys in the as-cast condition is quite heterogeneous. In addition, a properly homogenized ingot will enhance the validity of ultrasonic testing conducted downstream in the manufacturing process for that material.
Hydriding and Dehydriding
The hydride/dehydride process is used during the manufacturing of transition metal powders such as tantalum, niobium, vanadium, and titanium. These particular metals have a unique characteristic: they undergo a reversible reaction during hydriding. Vacuum purification and activation of the metal is necessary before hydrogen is readily absorbed to form the metal hydride. Absorbed hydrogen leads to an expanded metal lattice, which promotes cracking and embrittlement. Once embrittled, the material can then be crushed into powder for further processing. The refined powder is then returned to the vacuum environment and the hydrogen removed from the material.
Nitriding / Nitrocarburizing
Gas nitriding/nitrocarburizing involves a vacuum purge followed by atmosphere processing. This is an alternative to traditional retort-type gas nitriding systems, and claimed benefits include reduced cycle times and fewer consumables.
Ion (plasma) Nitriding
Ion nitriding introduces nascent (elemental) nitrogen to the surface of a metal part for subsequent diffusion into the material. In actual practice, the injected gas is a mixture consisting of 25% N2 and 75% H2. In a low vacuum condition, high-voltage electrical energy is used to form plasma, through which nitrogen ions are accelerated to impinge on the workpiece. This ion bombardment heats the workpiece, cleans the surface, and provides active nitrogen.
Solution Nitriding
A typical solution nitriding (a.k.a. high-temperature nitriding) process takes place in a vacuum furnace in the temperature range of 1050ºC – 1075ºC (1925ºF – 1970ºF). Nitrogen is introduced at pressures in the range of 1.5 – 1.9 bar for a typical period of 10 – 12 hours. The workload is subsequently rapidly vacuum quenched at pressures in the range of 10 bar.
Stress Relief
Vacuum stress relief operations can be performed on a variety of materials, especially those where no surface oxidation is allowed. An example is the stress relief of nickel aluminum bronze alloy. The stress relief cycle consists of holding at 315°C (600°F) ± 9°C (15°F) for sixty (60) hours after a long, controlled ramp heat-up. After stress relief, a slow rate of cooling is used to prevent reintroduction of stresses into the parts.
Other Thermal Processes
Specialized areas in which vacuum equipment is being used include the following:
Vacuum Metallurgy
Various technologies fall under the umbrella of vacuum metallurgy. These processes are used for the production of substances of great purity, and for materials and alloys requiring extremely high-performance characteristics. Applications include aircraft turbine blades, ingots of tool steels for mining and milling cutters, superalloy ingots for aerospace and power turbines, alloys for the chemical industry, and high-purity metals for electronics and telecommunications. All of these processes use various methods for melting and solidifying materials.
Typical methods and equipment for this industry can be summarized as:
- Vacuum induction melting (VIM)
- Vacuum induction degassing and pouring (VIDP)
- Electroslag remelting (ESR) and various process variations (developed by ALD)
- Increased pressure (PESR)
- Inert gas atmosphere (IESR)
- Reduced pressure (VAC-ESR)
- Vacuum arc remelting (VAR)
- Vacuum precision casting (VPC)
- Vacuum inert-gas metal-powder technology (VIGMPT)
- Vacuum isothermal forging (VIF)
- Vacuum turbine-blade coating using EB/PVD coating applications
Processes such as melting, joining (brazing, welding) and casting are commonly performed by first creating a vacuum and then backfilling with an inert gas into the vacuum vessel. Products that are stronger, with thinner cross-sections and long life are possible due to avoidance of oxidation and contamination. Application in the fields of space, aerospace, atomic energy, automotive defense, lighting and medical have benefitted from processing in vacuum.
Vacuum Thermal Recycling
Vacuum thermal recycling is used for certain hazardous industrial and special waste products (e.g., mercury-containing waste, PCB-contaminated materials, and oil-laden grinding sludge) for the separation of products with the simultaneous recovery of base materials. In these instances, vacuum thermal recycling is a cost-effective alternative to other types of disposal operations.
Vacuum Reclamation of Metals
The principle of separating pure metal from mixed metallic particles by vacuum metallurgy is that the vapor pressures of various metals at the same temperature are different. As a result, the metal with high vapor pressure and a low boiling point can be separated from the mixed metals through distillation or sublimation, and then it can be recycled through condensation under a certain condition.
Vacuum Freeze Drying
Freeze drying is common, especially in the food industry. The principle of freeze/sublimation drying is based on the fact that below its triple point, water only exists in the solid and the gaseous states. The freeze-drying process involves two distinct process steps. Step one is the freezing of the material below the triple-point temperature, and step two involves removing the ice crystals. Since the freezing process has a great influence on the quality of the finished product, this technology ensures that the product will be kept in the freshest possible condition.
Laboratory, Research & Development, Light Industrial
Laboratory and light industrial vacuum furnaces are suited for most common heat treatment processes where small-scale prototyping or product development are required. Melting and distillation processes in which reactivity or the special properties of the material, metal-based alloy or mixture require a complete or partial treatment under vacuum or protective gas. A major use of this equipment is for directionally solidified (DS) and single crystals (SX). In order to produce these components, high thermal gradients and constant-temperature solidification fronts are required.
Laboratory and light production applications include:
- Rare-earth metal production (yttrium, samarium, uranium aluminide)
- Optical coating materials
- Battery recycling
- Sintering of ceramics
- Distillation of metallic scrap and metals
- Ultra-pure materials for semiconductor devices and fiber optics
- Heat treatment of ceramics and glass
The Future of Vacuum Processing1
Industries with especially high potential for rapid growth (alphabetized listing) include:
- Additive manufacturing (medical, aerospace, energy)
- Biological (genomics, proteomics)
- Biotechnology (medical devices, regenerative medicine)
- Defense (anti-bioterrorism, security)
- Energy (fuel cells, fusion reactors)
- Environmental (emissions reduction, materials recycling)
- Material development (ceramics, composites, powder metallurgy)
- Nanotechnology (communications, biomedical, electronics)
These technologies are consistent with identified high-tech growth markets.
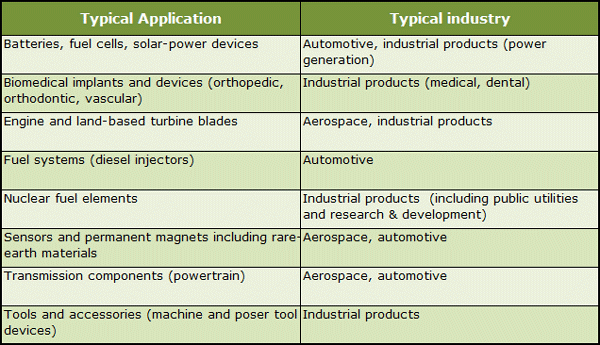
Summary
Vacuum processing and vacuum technology solutions are not a panacea, but they do represent the best way to ensure that the process is performed in a consistent and repeatable way. The challenges are in designing these furnaces, often requiring high temperature, high vacuum or pressure as well as being absolutely leak tight with leak rates in the 5 micron/hour range.
References
- Sakhamuri, Nagarjun, “Vacuum Furnaces for Metallurgical Applications”, Hind Hihg Vacuum Co, Pvt. Ltd.,
- Zahn, Lu and Zhenming Xu, “Application of Vacuum Metallurgy to Separate Pure Metal from Mixed Metallic Particles of Crushed Waste Printed Circuit Board Scraps”, Environmental Science & Technology, American Chemical Society, 2008.
- Jones Metal Products, “Why Vacuum Heat Treating Furnaces Are Important to Aerospace”, 2008.
- Herring, Daniel H., Vacuum Heat Treatment, BNP Media, 2012.
- Bodycote (www.bodycote.com).