When problems arise, especially those related to safety, we want to know that we have isolated the root cause and instituted corrective action measures so as to avoid their reoccurrence.
Worker safety and the safe operation of heat-treat equipment is both MANDATORY and NON-NEGOTIABLE, especially when operating and maintaining vacuum equipment where dangers of asphyxiation, electrocution, and explosion are as real as they are with any other type of thermal processing equipment. “It won’t happen to me” is not a phrase that belongs in the heat-treat shop and provides a false sense of security to all involved. There is no substitute for understanding the inherent dangers, taking the necessary steps and placing the right safeguards in place to prevent accidents from happening. Safety and safety issues are a serious matter and should be treated as such by all individuals within the company.
HAZARDOUS MATERIALS
Incidents Involving Gases
An example of an almost routine act performed on vacuum furnaces highlights the inherent danger we must constantly concern ourselves with. The operator of a two-chamber vacuum oil quench hardening and case hardening furnace was doing what he had done numerous times in the past, leaned his body (and head) into the heating chamber to attach a workload thermocouple. In this instance, the thermocouple jack panel in this furnace was off to one side and slightly below the height of the heating chamber. He was working alone, a sight not uncommon in the heat treat shop, but in an instant crossed an imaginary line and put himself in an unsafe and dangerous situation. What he failed to realize was that, despite the furnace being open to air for about half an hour, a pocket of nitrogen (backfill) gas lingered in the chamber in a localized area of the furnace. The writer, on his way to check on a process being run in a nearby unit, witnessed the events unfolds. His position was such that his body and head were inside the furnace chamber “for only a few seconds” to make sure that the male end of the thermocouple was in the correct socket of the jack panel. Fortunately for him, he had enough presence of mind to realize something was wrong and jerked his head and torso out of the vacuum furnace, woozy and disoriented. He staggered out an emergency door to the parking lot outside, with the writer in close pursuit. “Are you alright?” was followed by the response “Saw stars and almost blacked out” were the first words spoken. Had he fallen forward rather than moved backward, and been truly alone, a far different outcome would have occurred!
So, what were the lessons learned? First, while we often work alone around furnaces, if we believe we might be placing ourselves into a “confined space” we need to employ the buddy system and alert management of inherent danger. Next, though the specific gravity of nitrogen (0.97) is almost the same as that of air (1.0) and despite the fact that the air we breathe is 78% nitrogen, asphyxiation can occur under the right circumstances. Third, we must be trained to understand all of the dangers we face and how to react when something begins to happen to us. However, in this case, the writer would classify the operator’s action as instinctive rather than the result of training.
Gases and liquefied compressed gases used in and around vacuum furnaces (and all other types of heat treat equipment) fall into various categories:
- Corrosive. Products that react chemically and deteriorate materials (including skin) on contact.
- Cryogenic. Contact with these liquids causes “cryo burns” due to the freezing of the skin. Rapid vaporization in confined spaces can cause asphyxiation.
- Flammable. When mixed with air, oxygen, or another oxidant, these fluids burn or explode upon ignition.
- High Pressure. A sudden release of pressure may cause serious damage to personnel or equipment.
- Inert. These displace oxygen in confined spaces and threaten life support.
- Oxidant. Gases that initiate and support combustion.
- Toxic. Substances that may chemically produce injurious or lethal effects.
With an asphyxiant, oxygen may be displaced up to a level of under 19% quickly and before symptoms appear. Symptoms such as rapid respiration, diminished mental alertness, and impaired muscular coordination indicate there may be a problem. Death occurs almost instantaneously when the oxygen content is below 10%. Examples of asphyxiants include:
- Argon (Ar). Heavier than air. Difficult to purge from pits and recessed areas.
- Nitrogen (N2). Slightly lighter than air.
- Helium (He). Much lighter than air.
- Hydrogen (H2). Much lighter than air. Accumulates in ceiling areas and can reach dangerous concentration levels. Roof sensors tied to automatic ventilation systems are recommended.
- Methane (CH4) or Natural gas. Very slightly lighter than air. Often confused with natural gas (typically 90 to 95% methane). Natural gas has an odorant added, but methane does not.
- Propane (C3H8). Heavier than air. Slight odor.
The explosiveness of the air/gas mixture is the primary hazard with some of these gases. Hydrogen, natural gas, and propane are examples and should not be used near an open flame or heat source as they can “self-ignite”. They are very easily oxidized and react explosively in the presence of oxidizing substances.
Toxic gases, which are especially dangerous, include:
- Carbon monoxide (CO) is especially noxious because it does not provide adequate warning of its presence and its effects are cumulative. In addition, the bloodstream absorbs it and is life-threatening. CO monitors should be provided in all heat-treat shops.
- Ammonia (NH3) is a colorless gas with a strong, pungent odor and is lighter than air. It is usually transported liquefied by compression in cylinders. Ammonia is an extreme irritant to skin, eyes, nose, throat, and lungs. A moderately toxic inhalant, it can cause severe damage to the lungs when inhaled excessively. Not unexpectedly, when ingested orally, ammonia is highly toxic. It is not in and of itself a fire hazard since it is inflammable under 650ºC (1200ºF). However, if ammonia leaks into an area exposed to heat, it can certainly be explosive. And remember that “dissociated” (cracked) ammonia has the properties of hydrogen and nitrogen listed above.
Incidents Involving Liquids
In another instance, a maintenance man, working alone was tasked with cleaning the internals of a vacuum pump located off in an isolated corner of the building. Being winter, the area was sealed off with nearby windows and a bay door (normally left open several inches) closed tightly. For convenience, he decided to use tricholoroethylene from a nearby vapor degreaser, but the story might be similar if he were using acetone or alcohol. The amount of solvent being used was excessive and the location in which the work was being done allowed a plume of noxious gas to hover over the area. However, recognizing the potential danger, the maintenance individual wore a self-contained breathing apparatus and as such was not exposed to danger. The supervisor, who went to check the progress of the work, however, reported that the strong, pungent odor could have easily overwhelmed other individuals who might be working nearby and that this person should not have been working alone and definitely not used such a strong cleaning solvent.
Incidents Involving Explosions
We often believe that vacuum furnaces are inherently safe given that the heating and cooling operations take place in sealed chambers and sometimes (especially where high pressures are involved) in coded vessels. However, the belief that an “implosion” rather than an “explosion” will happen is not always the case. Here is one such example.
In this example, a company was operating a small single chamber horizontal vacuum brazing furnace with a hot zone of approximately 450 mm wide x 600 mm deep x 450 mm tall (18” x 24” x 18”). Multiple furnaces of the same general construction are at the facility and used to braze copper and stainless steel using copper/silver braze filler metal alloy. The vacuum furnace design was typical of many such units found in the industry; an all-metal hot zone, metallic heaters, a water-cooled shell and a standard pump package (mechanical pump, blower, diffusion and holding pumps in combination with a cold trap refrigeration system with chevron baffle on top of the diffusion pump). The furnace was equipped with a program controller and a programmable logic controller.
The incident described below resulted in the furnace outer door opening and almost being blown off. Several individuals received (luckily) only minor injuries. The root cause of the explosion was then thoroughly investigated and corrective action was taken.
The Incident
The following sequence of events took place. A routine shut down of the furnace was done to perform maintenance, which involved flushing of the water jacket, diffusion pump trace cooling coils, copper trace tubing around the hot zone, and the cooling fan copper heat exchanger, with a 1 : 1 ratio of water and Rydlyme (which has 5 – 9% hydrochloric acid by weight). The cooling water system of the furnace was flushed with this solution for approximately 1-1/2 hours. The system was drained and then flushed with clean water. The furnace was ready to be restarted after similar work was completed on several other furnaces on the same chill water system. To this point, nothing out of the ordinary was observed.
Then the following sequence of events took place.
1. The (chilled water) closed-loop recirculating system was turned on. All pumps were started along with the Poly Cold refrigeration system.
2. An outgassing cycle was run to remove moisture that may have accumulated in the furnace during the downtime. The furnace was held at 1095ºC (2000ºF) for two hours. Other than maintenance personnel who checked that the furnace was running the proper program, the furnace ran unattended.
3. At some point later, a furnace operator was alerted by a ringing alarm on the unit. A quick inspection indicated that this was due to a high foreline pressure (1 Torr). He also noticed that the diffusion pump was “off”.
4. Maintenance was called and found the holding pump contaminated with a great deal of water. The oil was changed but the foreline pressure was still around 1 Torr and the diffusion pump would not turn on. An electrician was called to check the fuses for the diffusion pump and found the over-temperature on the diffusion pump had tripped.
5. The electrician checked the fuses for the diffusion pump in the control cabinet and found them to be good. When the door to the cabinet was closed, it created enough vibration to affect one of the PLC modules that control all the vacuum valve solenoid valves (roughing, holding, diffusion, high vacuum). It turns out that the wiring was loose causing the valves to activate and move to their safe position or “ lost power positions”. The foreline, which was assumed to be open, now closed as did the holding valve. The furnace control was placed in the “Standby” mode.
6. The electrician heard these valves closing. Then he heard a steady alarm coming from the front panel. All of a sudden the furnace door, which was clamped shut and presumed to have approximately 0.008 Torr (-8” Hg) of vacuum inside, blew open breaking 3 out of 4 door clamps and creating an extremely loud noise. The heat pack on the door dislodged as the door flew open and it flew across the room. A white fog-like substance filled the air.
The question raised was, with the furnace at room temperature and empty, and the diffusion pump being cooled down and off, what could have caused such a blast?
There was no power to the heating elements (room temperature inside the hot zone) and no power going to the diffusion pump heaters. On disassembly, the jets in the diffusion pump were found to be undisturbed. Furthermore, the argon backfill should not have triggered and the chamber had a working pressure relief valve that did not activate.
The Root Cause
A thorough investigation found that the silicone-based diffusion pump oil had been overheated due to a lack of cooling water to the pump (a water line plugged with mineral deposits). Furthermore, the over-temperature limit did not trip.
The oil was analyzed and it was found that the flashpoint of the oil had dropped considerably (from around 250c to 125c) and there were volatile compounds of different types found in the oil. The over-temperature limit switch did not trip even though there was only about 600 – 650cc of diffusion oil remaining in the pump. It was being displaced by carbon (from oil that had fractionated) making the sight glass appear that there was sufficient oil in the pump.
A small air leak was also found in the holding valve and the boiler-plate was loaded with carbon and the bottom of the baffle assembly in the diffusion pump literally fused to the boilerplate.
Resolution
To avoid this from ever happening again it was recommended that the flow of water to the diffusion pump be monitored, the over-temperature sensing switch on the diffusion pump be replaced, the holding valve be repaired, a different type of pressure relief valve be installed and a change to the preventative maintenance schedule to check more frequently that all valves function properly. Changes in the furnace logic were also made so that the roughing valve would not open if the foreline valve is in the open position (a good practice even if this was not the root cause of this problem).
In addition, changes were also made to the preventative maintenance schedule on the diffusion pump to take them down on a yearly basis to clean and check for the start of any oil degradation (in the form of caramelization).
While one might believe that the volatile by-products of the oil and some air made its way into the furnace vessel, this incident was an explosion in the diffusion pump. Most vacuum furnace operators do not realize that diffusion pump oil can become contaminated over time. A source of this contamination is oil present on workloads, which is volatized on heating and migrates to the diffusion pump. Over time, this results in a lowering of the diffusion pump oil’s flashpoint. On overheating of the oil, with air present, an explosion will occur. The incident in question does not appear to have been the result of a minor air leak but a major one (the result of the diffusion pump near atmospheric pressure). The most commonly employed fix is to change the diffusion pump oil (it should be changed annually as a minimum). However, a more permanent fix is to completely disassemble the diffusion pump (at least every few years) and completely clean the jet assembly and diffusion pump internals.
It is also a good idea not to rely on the sight glass but rather drain the oil completely and recharge with the correct measured amount. Plugging of water lines almost always starts where there is a restriction or in small diameter lines (e.g., diffusion pump coils or power feed thru terminal water lines). Correct water chemistry for cooling water is very important and should be tested monthly and chemicals added as required. Water filter bags on all cooling water systems to filter out mineral deposits and scale (rust) are a good idea and these filter bags should be changed monthly.
In Summary
Health and safety are everyone’s responsibility and being aware of the dangers and taking steps to avoid incidents in the heat-treat shop (or anywhere in the plant) will make it a better place for all of us to work. Remember, nothing replaces common sense when it comes to avoiding injury. Learn and follow the company rules and protect yourself at all times.
INFORMATION CONCERNING CONFINED SPACES
In the article above, we addressed some aspects of vacuum furnace safety and before we talk about confined entry spaces and how this applies to vacuum furnaces, it is worth remembering what we talked about previously when we said:
“When problems arise, especially those related to safety, we want to know that we have isolated the root cause and instituted corrective action measures so as to avoid their reoccurrence. Worker safety and the safe operation of heat-treat equipment is both MANDATORY and NON-NEGOTIABLE, especially when operating and maintaining vacuum equipment where dangers of asphyxiation, electrocution, and explosion are as real as they are with any other type of thermal processing equipment. “It won’t happen to me” is not a phrase that belongs in the heat-treat shop and provides a false sense of security to all involved. There is no substitute for understanding the inherent dangers, taking the necessary steps and placing the right safeguards in place to prevent accidents from happening. Safety and safety issues are a serious matter and should be treated as such by all individuals within the company.”
We went on to talk about such topics as (a) incidents involving gases; (b) incidents involving liquids and (c) incidents involving explosions. Now we need to address an important safety aspect that may apply when servicing vacuum equipment – confined spaces.
What is a Confined Space?
In simplest terms, a confined space is one in which there is only one way in and one way out. Thinking about most single chamber vacuum furnaces – either horizontal (Fig 1) or vertical (Fig. 2), this definition applies. As such, there are a number of rules, procedures, and training that must be followed, some of which will be briefly discussed below. Appropriate signage (Fig. 3) should also be provided.
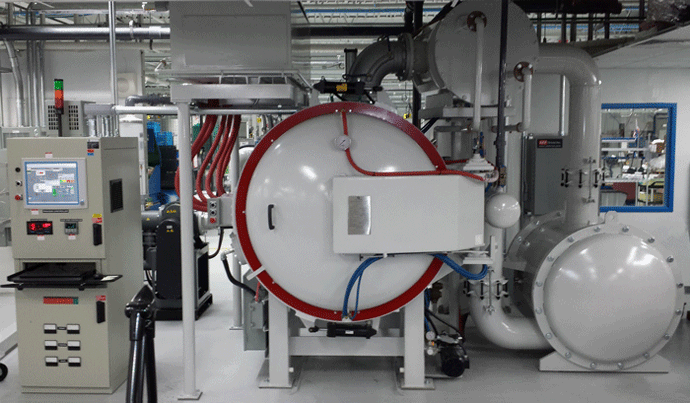
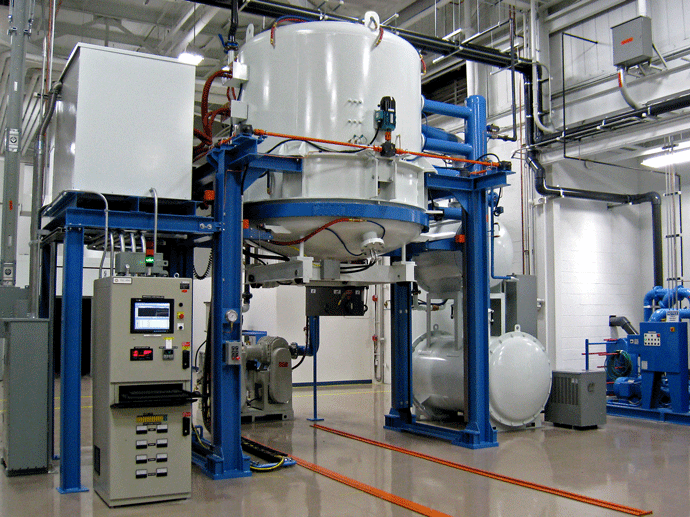
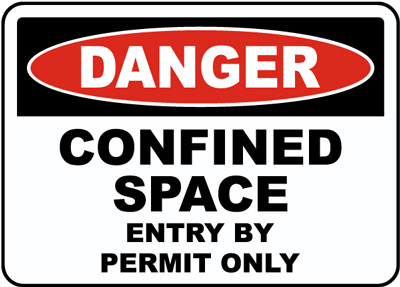
Confined Entry and Permit-Required Confined Entry Spaces
It is the employer’s responsibility to identify all confined entry spaces (Fig. 4) in the workplace and to then distinguish between a confined space and a permit-required confined space (Fig 5). These terms can be defined as follows:
- “Confined space” – a space that meets one or more of the following:
- Is large enough and so configured that an employee can bodily enter and perform assigned work;
- Has limited or restricted means for entry or exit (for example, tanks, vessels, silos, storage bins, hoppers, vaults, and pits are spaces that may have limited means of entry);
- Is not designed for continuous employee occupancy.
- “Permit-required confined space” – a confined space that has one or more of the following additional characteristics:
- Contains or has a potential to contain a hazardous atmosphere;
- Contains a material that has the potential for engulfing an entrant;
- Has an internal configuration such that an entrant could be trapped or asphyxiated by inwardly converging walls or by a floor which slopes downward and tapers to a smaller cross-section; or
- Contains any other recognized serious safety or health hazard.
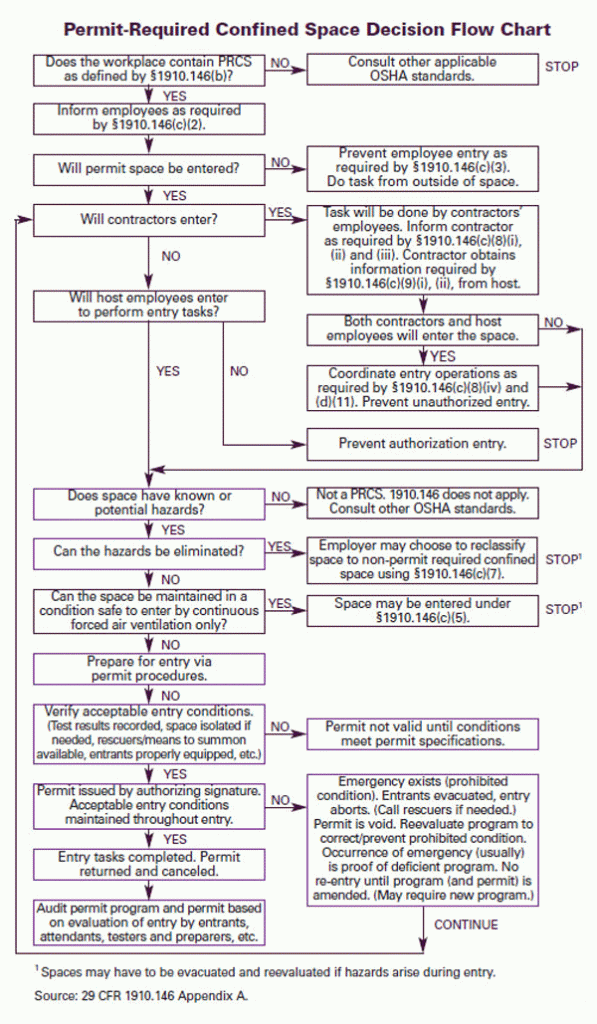
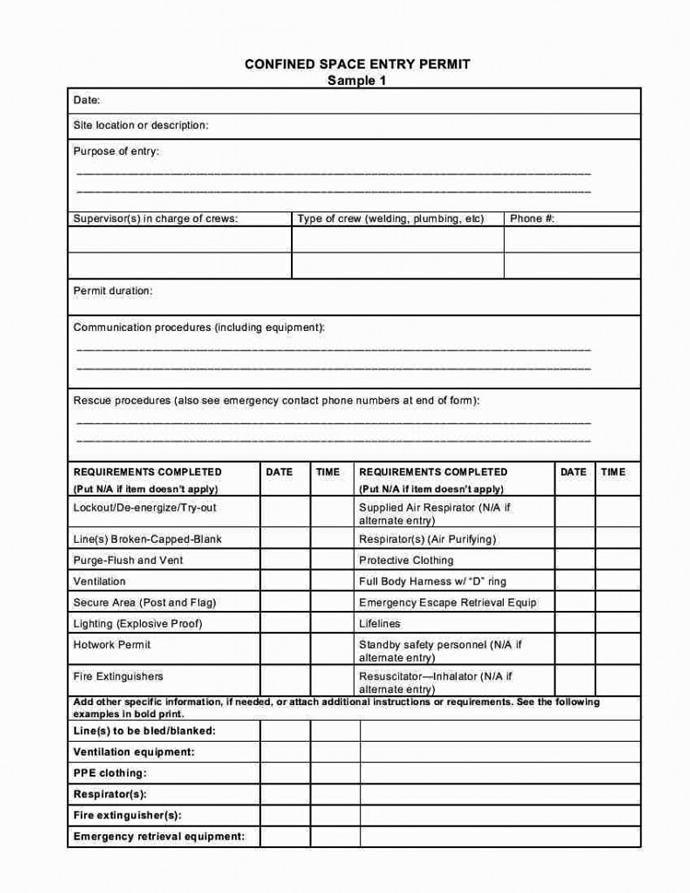
Other Definitions
We also need to understand other terms that are commonly used by OSHA and other agencies when talking about confined spaces, namely:
- “Entry” – the action by which a person passes through an opening into a confined space. Entry includes ensuing work activities (e.g., maintenance activities) in that space and is considered to have occurred as soon as any part of the entrant’s body breaks the plane of an opening into the space.
- “Entry permit” – the written or printed document that is provided by the employer to the employee allowing entry into a permitted confined space. The entry to a permitted space is witnessed by members of the plant safety team who are required to be in attendance.
- “Authorized entrant” – an employee who is authorized by the employer to enter a permitted space. This authorization is typically granted only after some form of training on the hazards or potential hazards associated with the space involved. The space should have been tested to ensure proper air quality (see below) and the individual entering the space should have an oxygen monitoring device.
- “Attendant” – an individual stationed outside a confined entry space or one or more permitted spaces and who monitors the authorized entrants and who performs all attendant’s duties assigned in the employer’s permit space program. NOTE: It is not the responsibility of the attendant to enter the space to assist an entrant experiencing difficulties in that space.
- “Rescue service” – the personnel designated to rescue employees from a confined or permit confined space.
Remember that all confined spaces are potentially hazardous to enter. Potential hazards within a vacuum furnace involve such items as:
- A space in which the atmospheric oxygen concentration may be less than 19.5%
- A space in which there can be an atmospheric condition brought about by inadvertently introduced life-threatening gas (e.g. nitrogen, argon, acetylene, etc.) into the area that is immediately dangerous to life or health.
- A space in which there can be the removal of oxygen from the space brought about by inadvertent activation of the vacuum pump(s) and that is immediately dangerous to life or health.
- The potential for the presence of flammable gases, vapors, mists or other airborne contaminants, which can combust or exceed the lower flammable limit (LFL).
Before an employee enters a confined space, the internal atmosphere shall be tested, with a calibrated direct-reading instrument, for oxygen content, for flammable gases and vapors, and for potential toxic air contaminants, in that order. Any employee who enters the space, or that employee’s authorized representative, shall be provided an opportunity to observe the pre-entry testing performed for each of these conditions.
Typical Procedure
A generic procedure for individuals working within areas designated as confined spaces will follow. The reader is directed to procedures outlined in applicable Occupational Safety and Health Administration (OSHA) standards and State Office of Risk Management (SORM) guidelines for safe work practices, which supersedes the generic information contained here. See the partial list of other applicable documents below. The primary purpose of these procedures is to provide generic information to help ensure that individuals are protected from injury or death associated with working within designated confined spaces.
- The Facilities Coordinator or his designate in combination with the plant safety committee must determine if work in the confined space is necessary after reviewing and evaluating options.
- If confined space work is authorized by the Facilities Coordinator or his designate, a written Confined Space Entry Log and Debriefing Documentation must be maintained.
- The authorized entrant must conduct an initial atmospheric test using a device for that purpose prior to entering the confined space. Adequate ventilation of the confined space must also be confirmed. The authorized entrant must ensure that atmospheric oxygen content is between 19.5% to 23.5% oxygen and that the LEL (lower explosive limit) is 0%. Otherwise, entry will not be permitted unless and until the condition changes or proper protective equipment is used to safely enter.
- The authorized entrant must be equipped with the proper protective equipment, if required, ensure that it is functional and is used during the entry.
- While the authorized entrant is in the confined space, a standby attendant must remain outside of the confined space entry location at all times.
- The authorized entrant must have a means of regularly (at least every 10 minutes) communicating with the standby attendant when in the confined space area. Communication by cell phone, radio, or verbal contact is acceptable. The purpose is to access the condition of the individual in the confined space.
- The standby attendant will contact 911 – Emergency Service Personnel and follow all additional plant rules and regulations should a rescue situation occur. The standby attendant must never enter the confined space for rescue or other reasons. The purpose for this is that the same hazard that affected the authorized entrant may overcome the standby attendant as well.
- If rescue services are required, the standby attendant should next contact the Facilities Coordinator. The Facilities Coordinator should notify the Facilities Director, the Safety & Risk Manager and the plant safety committee members.
Training, Record Keeping, and Documentation
- Annually, the Facilities Coordinator and other supervisory staff who may instruct employees to enter confined spaces and any employee who may be required to work within a confined space must participate in training and basic knowledge testing of confined space procedures. Initial and refresher training is to be provided so that employees will have an understanding of the procedures to be followed as well as the understanding, knowledge, and skills to perform confined space entry work safely.
- Training is the responsibility of the Facilities Coordinator. For confined space entry training requirements, refer to OSHA standards and SORM guidelines. Annual training can be done by computer-based interactive CD-ROM’s which include course testing and record-keeping documentation.
- Training and basic knowledge testing documentation will be maintained by the Facilities Coordinator for audit and institutional compliance review purposes, for a minimum of three years following the close of the active fiscal year. Training records will include each employee’s name, the signatures or initials of the trainers, and the dates of training.
- The meter used to conduct the atmospheric testing and the LEL testing should be calibrated annually or per manufacturer’s guidelines and per applicable industry standards. Employees conducting the testing should have initial training and annual refresher training on the proper use of the meter.
Confined Space Entry Log and Debriefing Documentation
- Facilities Services will maintain a written Confined Space Entry Log and Debriefing Documentation of all confined space activities including contractor confined space entry.
- The Confined Space Entry Log will include the following information as a minimum: The reason for entry, building or plant area location, standby attendant name, Authorizing Supervisor signature, authorized entrant’s name and signature, date of entry, time in and time out. A debriefing document will ask each authorized entrant specific questions related to his/her activities in the confined space entry.
Contractor Confined Space Entry
When the company arranges to have employees of another employer (aka contractors) perform work that involves confined space entry, the company shall:
- Inform the contractor that the workplace contains confined space entry and that entry is allowed only through compliance with confined space entry program meeting OSHA standards.
- Apprise the contractor of the elements, including the hazards identified and the Company’s experience with the confined space entry.
- Apprise the contractor of any precautions or procedures that the Company has implemented for the protection of employees in or near the confined space entry where contractor personnel will be working.
- Coordinate entry operations with the contractor by verifying that the contractor employees have been properly trained, authorizing the entry, providing the entry log and debriefing documentation, testing the internal atmosphere and ensuring the entry is performed safely.
In addition to complying with the confined space entry requirements that apply to all employers, each contractor who is retained to perform confined space entry operations shall comply with applicable Occupational Safety and Health Administration (OSHA) standards specifically 29 CFR Part 1910 – Permit-Required Confined Spaces, Section 1910.146 (c) (9) (i, ii, iii).
Annual Review
The Facilities Coordinator shall review annually this procedure and recommend any changes to the Safety & Risk Manager and plant safety committee. Changes may result from OSHA standards or SORM guideline changes or changes in company practices.
Sample Documents (Partial List)
The reader is directed to the OSHA website (www.osha.gov) for links to obtain copies of all documentation on this subject including but not limited to:
- OSHA Permit-Required Confined Spaces (OSHA Document 3138-01R – latest revision)
- OSHA Permit-Required Confined Spaces (OSHA Document 29 CFR 1910.146 – latest revision)
- OSHA Safety and Health Topics | Confined Spaces
- OSHA Confined space entry
Other OSHA documents that may apply include:
- OSHA 1910.146 Permit-required Confined Spaces
- OSHA 1910.146 App A – Decision Flowchart
- OSHA 1910.146 App B – Procedures for Atmospheric Testing
- OSHA 1910.146 App C – Examples of Programs
- OSHA 1910.146 App D – Pre-Entry Check List
- OSHA 1910.146 App F – Rescue Team or Rescue Service Evaluation
- OSHA Small Business Training: Confined Spaces
- Confined Space Entry: OSHA Regulatory News (SSPC)
- Confined Space Entry (DOE)
- Confined Space Entry Manual
- Confined Space Entry Manual
- Confined Space Entry: Glossary of Commonly Used Terms (RescueNet)
- Confined Space Entry: No Room for Error! (RescueNet)
- Confined Space Hazards (SafetyInfo)
- Confined-Space Pre-entry Checklist (DOE)
- Confined Space Pre-entry Checklist
- Confined Spaces (Saftek)
- Confined Spaces (Lab Safety Supply)
- Confined Spaces Documentation Requirements Checklist (Saftek)
- Confined Space Rescue (RescueNet)
- A Guide to Safety in Confined Spaces
- NIOSH Confined Space Entry Document (RescueNet)
- Permit-Required Confined Spaces
- Preventing Entrapment and Suffocation (NIOSH)
- Preventing Occupational Fatalities in Confined Space (NIOSH)
- Sample Confined Space Program
In Summary
Our intent was to introduce this important subject to the reader who is encouraged to seek additional information and training before making decisions as to whether to participate in activities involved with confined entry spaces.
References
1. Herring, Daniel H., “Vacuum Heat Treatment, BNP Media, 2012.
2. Herring, Daniel H., “Atmosphere Heat Treatment Volume II, BNP Media, 2015.