Passing a Nadcap audit is considered by most heat treaters to be both a significant company-wide accomplishment and a benchmark as to their commitment to quality. Nadcap accreditation not only allows the company to perform heat treating for the Aerospace/Defense industries but perhaps equally important announces to all of its customers and potential customers that it has met or exceed the highest quality standards in the industry.
What is Nadcap?
In simple terms, Nadcap accreditation is an assessment process whose approach is focused on establishing conformity throughout the industry. This is brought about by bringing together technical experts from all over the world for the purpose of establishing requirements for accreditation, supplier approval and to define operational program requirements.
Nadcap accreditation is considered the “gold standard”, not only in Aerospace heat treatment but throughout the industry. Having Nadcap accreditation means the company has taken a proactive approach to guarantee heat treat proficiency and taking steps toward risk management of the products they heat treat or produce. In other words, heat-treatment operations are better managed, better controlled and deliver fewer defective parts.
How Does it Work?
The Performance Review Institute (PRI, www.p-r-i.org) administers the entire Nadcap program and has many tools, including classes, to help ensure that applicants will be well prepared for their audit. PRI will schedule an audit and assign a registered auditor to conduct the actual on-site audit This will be done using standards and checklists that have world-wide acceptance.
At the end of the audit, any nonconformity issues (major or minor) will be documented and nonconformance reports issued. PRI will then remotely administer closeout of these reports and this process is neither simple nor quick given the amount of documentation and proof of compliance involved. Therefore, it is critical to go through a rigorous pre-audit process and correct all nonconformities prior to the formal audit. DO NOT take this process lightly.
Upon completion, PRI will present the completed audit package to a special-process task group made up of members from the industry that will review it and vote on its acceptability for approval. Accreditation is granted when all nonconformance issues are closed.
Comprehensive online resources through the PRI website (www.eAu- ditNet.com) assist with the accreditation process, particularly the Heat Treat Pyrometry Guide (which helps provide clarification/interpretation of a variety of AMS 2750 details), a list of the most common audit findings (which should be very carefully studied), audit checklists, meeting notes, training guides, auditor handbook, audit advisories and operating procedures (NOPs – includes audit-preparation requirements, criteria for audit failure, etc.). Being unprepared or failing to adequately document company processes or procedures are the most common reasons Nadcap audits fail.
Suppliers new to the process may want to consider attending training courses offered by PRI, most notably Nadcap audit preparation courses specific to a discipline (e.g., heat treatment) and root-cause and corrective action (RCCA) training. These are offered in cooperation with PRI and are highly recommended. It is not uncommon for initial RCCA responses to be rejected, requiring additional investigation into the root cause and/or providing significant objective evidence.
In addition to the core checklists for various disciplines, there is also a supplemental checklist with requirements specific to a prime customer. If you have identified that you do business with any of these customers as part of the defined scope of your audit (done in advance of audit), then you must also complete all questions on this checklist applicable to those customers.
Why Should we be Accredited?
Nadcap accreditation benefits not only the company being audited but helps ensure their customers receive products and services that meet or exceed both their expectations and requirements. The audit and accreditation processes result in continuous improvement in multiple areas, with deficiencies (i.e., nonconformances) identified and corrected based on specific rules (i.e., guidelines) to ensure each process meets or exceeds industry standards.
Benefits to customers of working with a Nadcap accredited supplier include:
- Assurance that heat-treating processes or testing adhere to strict guidelines, the purpose of which is to guarantee absolute product quality and enhance overall product safety.
- Assurance that the supplier will conduct regular reviews of their operations, the purpose of which is to continuously improve processes and product quality. Caution:
- This should not be used as a substitute for supplier audits.
- Assurance that the supplier adheres to the latest industry standards for quality and process. Nadcap accreditation tells a supplier that a systematic approach of checking to confirm control and repeatability of a given process is being done.
- Providing proof of both quality control and quality assurance, which ultimately saves customers time and money
- Providing proof of adherence to a nationally recognized certification program managed by Aerospace industry professionals
- Assurance that those suppliers utilizing special processes (including heat treating) comply with consistent, high-quality standards acceptable to critical performance industries such as Aerospace, Defense, Power Generation and the like.
What Areas Will be Audited
PRI has established a Heat Treating Task Force for the purpose of helping companies prepare for the audit process as well as conducting the actual audits themselves. Critical manufacturing processes such as heat treating (Table 1), coating and materials testing can be, individually or collectively audited and accredited (It is not uncommon for a heat treat shop to obtain process accreditation and forget that without an accredited metallurgical laboratory, testing must be performed outside the facility, a costly oversight).
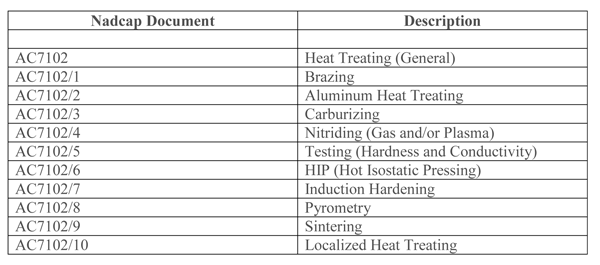
Preparation for a Nadcap Audit
The Nadcap audit process looks at the processes being run, the equipment being used and, if the Aerospace industry is involved, the specifications of the individual primes being serviced.
Nadcap accreditation typically involves the following steps:
- Requesting and scheduling an audit
- Performing an internal (pre) audit
- Implementing corrective actions for any findings from the internal audit
- Performing the official PRI audit
- Reviewing and responding to nonconformances (major or minor)
- Applying and documenting corrective actions to resolve the nonconformances
- Planning and preparing for upcoming Nadcap accreditation
There are a number of steps that can and should be taken to prepare for a Nadcap audit. A few of them are discussed below.
Training
One of the most overlooked areas in most company quality programs and a mandatory component of any Nadcap audit is personnel training. A formal training program must be in place and conducted in accordance with SAE-ARP-1962 (Training and Approval of Heat-Treating Personnel), latest revision.
The training program must include both classroom training and OJT (On-the-Job Training) and have a provision for continued training commitments over time including reinforcement training typically done on an annual basis. Another overlooked aspect of ARP-1962 is the ability of the company to define its own unique training program, the absence of which results in default to the requirements of the specification – in some instances requiring 160 hours of classroom training combined with 2 years of OJT to successfully complete the program.
Audit Preparation
The top ten things to remember that are required when preparing for and conducting Nadcap audits are:
- Provide quality system training including document control, calibration, record keeping, and results of internal auditing to all employees involved in the audit.
- Make all internal parties aware of the impending audit, calibration, receiving, inspection, purchasing, and document control.
- Make key personnel-management representative, quality manager, level IIIs and calibration technician-available for the audit.
- Conduct a comprehensive internal (self) audit using the Nadcap criteria, or checklists. Be thorough and demanding that everyone take the audit process seriously, it will make things far easier later on.
- Collect and review (for compliance) copies of the objective evidence, such as calibration certificates, quality procedures, records, logs, and sample job traveler that the auditor will need to review beforehand.
- Verify that there will be a sufficient number of parts, products, and components available for demonstration of proficiency. Make sure to review all previous jobs run in the past for the conforming of deficiencies as well. This is often a trip point in the audit process.
- Review inspection (destructive and non-destructive) personnel’s competence in performing the required testing processes, inspections during the audits (pre-audit and the official audit).
- Assign knowledgeable escorts for the Nadcap auditor who is familiar with where and how to produce required documents and can help the auditor understand your company operation.
- Provide the required resources for the audit, from having an Internet connection, copier, scanner, and office personnel available to a good workspace.
- Advise your customers, internal and external, of the impending Nadcap audit. They also have a vested interest in your success as an accredited Nadcap supplier.
Details involved with performing a Nadcap audit.
In the article above we discussed the fundamentals of Nadcap accreditation: what it is, how it works, why we should do it, what will be addressed in the audit, and how we should prepare. Here, we will talk about pre-audits, how to review the audit’s findings, how to analyze the root cause of a major or minor nonconformance, how to apply corrective actions, and what we should do after the audit is complete.
Pre-Audits
Pre-audits (aka internal audits, self-audits) are commonly misunderstood – they are not a recommended practice but a mandatory one, to be conducted prior to the formal Nadcap audit process. Failure to perform a pre-audit will result in the Performance Review Institute (PRI) auditor reporting a major nonconformance with accreditation standards. Completion of the pre-audit should be done within the 90-day period of the formal audit. This is considered best practice and will give ample time to resolve any issues that come up and to avoid surprises during the formal auditing process.
Whenever possible, an internal team should be assigned to perform the pre-audit so that no important details of the checklist requirements will be missed. Hiring an independent auditor who was properly trained in Nadcap accreditation is an option worth considering as it offers an outsider’s impression of the heat treat department’s performance that internal people may have overlooked. While PRI has put considerable effort into keeping the audits consistent regardless of the company, the different skill sets of auditors and their experience will influence the audit process.
Corrective actions from previously performed audits will need to be verified as still being effective and in place as part of the pre-audit process. If the PRI auditor notices a repeat finding that has not been fixed, it will automatically be noted as a major nonconformance. Each audit includes checklists to examine all pyrometric equipment including their calibrations, certifications, preventative maintenance and periodic test results (e.g., SAT, TUS, vacuum leak rates, dew point measurements, etc.). Often times, auditors will pay close attention to the calibration of instruments and may ask questions about how they are set and about the manufacturer’s requirements. Furthermore, it is important to make sure all of your thermocouple certifications and calibration points (process T/C, SAT T/C, TUS T/C, quench-oil T/C, etc.) are up to date since auditors tend to give them a close inspection.
With any defined procedure, the required documentation must be present. Failure to have this documentation readily available is also a nonconformance. If a requirement is listed as an industry standard, procedures and documentation must fully comply with the standard in order to avoid a nonconformance during the audit. Support staff should also be on hand during the formal audit, and the work they do should be discussed in the pre-audit. These disciplines include (but are not limited to): hardness test inspectors, metallurgical lab personnel, and TUS/SAT checkers (if applicable). Be sure that all support staff is properly trained. In addition, it is mandatory for Nadcap accreditation to have a heat treat training program that is compliant to SAE-ARP-1962 (latest revision).
It is important to note that the company assumes responsibility for all aspects of compliance, even for those processes that may be performed by outside heat-treating or support companies. Any and all documents that certify compliance, such as those for the calibration of instruments, the certification of thermocouples, or quench-oil test results, must be reviewed and verified. The documentation should be signed by an authorized individual (e.g. metallurgist, quality engineer, technician, supervisor, etc.). Failure of a sub-supplier is the failure of the company.
In addition, the company has the responsibility of gathering all compliance paperwork from any outside service provider and must verify that the paperwork is accurate. Nadcap accreditation requires attention to detail, and companies must show full-time commitment, especially when it comes to acquiring or issuing revision and/or changes including up-to-date documentation on instruments, changes to internal procedures, periodic testing, preventative maintenance and record control/verification. The checklist for the quality system is kept to a minimum if the supplier has AS9100 accreditation (or equivalent).
Tolerances for temperature, ramp rates, preheat and soak times, cooling rates, carbon potential and all other recorded data that follow the company’s internal procedures must be carefully checked. This data should also be consistent with industry standards and specific customer requirements. If a tolerance is not specified, companies should specify the tolerance. A failure to provide a reference to tolerances will again result in nonconformance during auditing (due to the actual values having a tendency to vary during the process).
Think like an auditor! You should be prepared to have sample jobs available to the auditor that are representative of each type of work that is heat-treated at the plant (by customer, material, process, configuration, etc.). Remember, long audit jobs may require more than one audit. The auditor might start with one process that will begin on the audit’s first day and then continue while on-site. In addition, there should be at least one other similar job that was previously run within the months prior to the audit. Other jobs are often selected at random by the auditor.
Reviewing up to eight jobs is not uncommon for short duration job audits. Many times, half these jobs are ones that the auditor will want to see on-site and the remainder can be previously completed jobs. Auditors have a tendency to select jobs that touch on multiple customers if such jobs are available. If the scope of the audit includes a process like carburizing, a carburizing job must be ready for processing during the time of the audit. If no such job is available for processing, the auditor will typically select one that has been recently completed. The collection of job paperwork, ranging from purchase orders to prints, routings, records, product and/or test results, etc.) can be a time-consuming process. It is advised to have resources available to help with the gathering of this information when necessary.
Once the pre-audit is performed, it is critical to follow the proper steps outlined by PRI in preparation for the official audit. These steps include:
- Reviewing, correcting and documenting any nonconformances
- Performing root-cause analysis
- Implementing corrective actions
Reviewing Findings
A nonconformance is a finding that has been identified during the internal audit or one that the auditor identifies during their official audit. Nonconformances can fall into one of two categories: major or minor. A major nonconformance is either “the absence of, or systemic breakdown of, the process control and/or quality management system,” or “any nonconformance where the effect impacts or has the potential to impact the integrity of the product.” A minor nonconformance is “any single system failure or lapse in conformance with the applicable standard or audit criteria”. In other words, a major nonconformance suggests there is a lack of control over the process or product quality, or that the safety of the product might be compromised while a minor nonconformance is any deviation from Nadcap/AMS specifications or customer standards that does not impact the product (e.g., a typographical error). If a minor nonconformance could affect the product (e.g., not having a thermocouple calibration document on hand), then it becomes a major nonconformance.
After the audit is complete, nonconformances should be addressed quickly and completely, starting with any major nonconformances so that product quality is not compromised. Nonconformances should be prioritized and grouped together, if possible. Remember, in order to address a nonconformance, one must determine its root cause, a process that may take time to determine and correct. Clearing audit nonconformances is a painstaking and time-consuming process, which is why so much effort is put forth to avoid their issuance.
Performing Root-Cause Analysis
A common mistake when trying to find the root cause of a nonconformance is to list contributing factors or simply attribute the problem to “human error” (e.g., the operator did not adhere to the correct procedure). However, the root cause in this example is training, which must be conducted and verified as having been done.
Applying Corrective Actions
Implementing corrective actions for any findings discovered during the internal audit is one of the final steps in performing the pre-audit. This must be submitted to PRI at least 30 days before the official audit.
For example, during the internal audit, let’s say you identified a nonconformance due to a typographical error in the calibration report for the overtemperature controller. This has no product impact. However, if the root cause is a lack of quality resources for reviewing calibration reports and if the calibration service provider is not available to correct the root cause within the 30 days before the scheduled audit, you should note in the internal audit report that the corrective action will be fully implemented and verified during the next calibration with the future date. After the official audit, the auditor will then verify that the corrective action was implemented by the aforementioned date.1
Be sure to document the implementation of any corrective action after the internal audit, as auditors will verify that these corrective actions are in place during the official Nadcap audit.
What to do after the formal Nadcap Audit is Complete
Whether the Nadcap audit was successful or not, the steps outlined below are necessary to complete the audit and prepare for the next audit or plan for the re-audit process.
Reviewing Findings
In order to correct a nonconformance, one must review the finding with the auditor while he/she is on-site to make absolutely sure there is an understanding of what the finding was and how it was interpreted. When the audit is complete, it is necessary to respond to all findings in writing. Take this step very seriously. This should include a detailed explanation including:
- A nonconformance statement
- The root cause
- The corrective action is taken
- The impact of the nonconformance on the product(s)
- The action is taken to prevent future reoccurrence
- Objective evidence that the corrective action will provide a complete and thorough solution to the problem at hand.
Performing Root-Cause Analysis
First, it is critical to understand that there is only one root cause to any given problem. It’s identification often requires a company to dig deep into its assumptions, procedures, and methods to understand the true nature of the problem. PRI and other groups often can support this effort with training classes. Depending on the auditor’s findings, it may turn out that multiple findings can be grouped together reducing the time required to solve them.
Applying Corrective Actions
The last and most important step is applying the corrective action in the real world. For example, if there was a finding for improperly located load thermocouples and you determined the root cause was a lack of operator training, the corrective action would be to provide operator training at a specific frequency; you should then note the training schedule that has been followed since the corrective action was implemented.
After the audit is complete, and within 21 calendar days, it is necessary to submit an initial response to the audit findings. After the initial response, one has 7 calendar days to provide a detailed response. PRI will accept or reject the company’s explanations. Only 4 total responses are allowed. Thirty extra days may be allotted if more time is needed; however, utilizing these extra days can affect a company’s merit score and, if unsatisfactory, could lead to an audit failure.
Summary
The simplest advice anyone can give regarding any audit process is to “say what you are doing and do what you say”. In other words, have clearly defined procedures in place and documentation that demonstrates that these procedures are being followed. Be thorough, be open, be honest, and be prepared. Surprises are not what either the auditor or the company want. Contrary to popular belief, auditors are not out to fail you, but rather to evaluate your words and actions toward a goal of total commitment to quality.
Finally, keep track of what worked well and what didn’t so you will be prepared for the next audit cycle. Continuous improvement with respect to processes, equipment and methods will enhance the quality and safety of the products you produce and your reward will be a successful audit!
References
- Ipsen USA (https://www.ipsenusa.com/processes-and-resources/articles-and-white-papers/obtaining-nadcap-accreditation-helping-you-pass-your-audit)
- Herring, Daniel H., Vacuum Heat Treatment, Volume 2 (Chapter 38.4), BNP Media, 2016
- Arrow Cryogenics (https://www.arrowcryogenics.com/nadcap-certified
- Quality (https://www.qualitymag.com/articles/90405-the-role-of-nadcap)
- Aston, Jerry “The Heat Treatment Task Group Offers Its Top Tips in Order to Prepare for a Successful Nadcap Audit”, Thermal Processing, August 2019
- Quality (https://www.qualitymag.com/articles/90405-the-role-of-nadcap)
- Herring, Daniel H., Vacuum Heat Treatment, Volume 2 (Chapter 38.4), BNP Media, 2016.
- Arrow Cryogenics (https://www.arrowcryogenics.com/nadcap-certified)
- Aston, Jerry “The Heat Treatment Task Group Offers Its Top Tips in Order to Prepare for a Successful Nadcap Audit”, Thermal Processing, August 2019.