Vacuum valves are an essential component in any vacuum system. There are a variety of different types that fall into three main categories – operational valves, closing valves and sealing valves (Fig. 1). The selection of the proper valve type requires an understanding of the process application so that the proper design and/or functioning valve can be chosen for a given vacuum furnace operation.
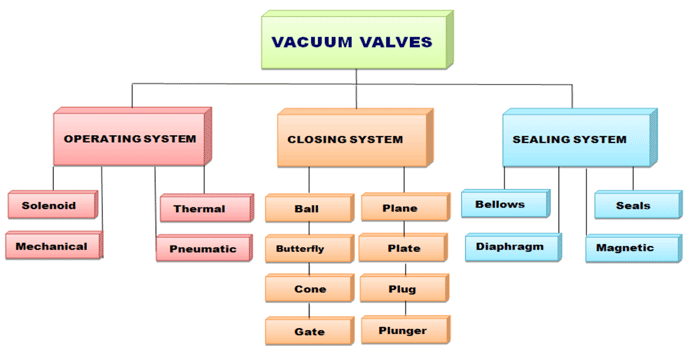
When talking about vacuum valves the ones that most people think of are those installed in lines that connect a vacuum chamber to a vacuum pump: the roughing valve (aka main valve if a diffusion pump package is not installed), the poppet (aka the main valve), the foreline valve and the holding valve. The gas evacuation path is different during initial pump down (aka roughing) with gas moving through the mechanical pump line (Fig. 2a) with the poppet value closed as opposed to when the diffusion pump is activated and the poppet valve is open and the flow is through the diffusion pumps (Fig. 2b) for high vacuum capability.
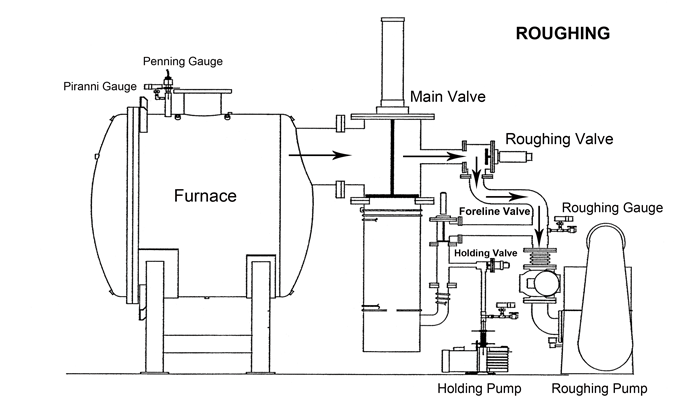
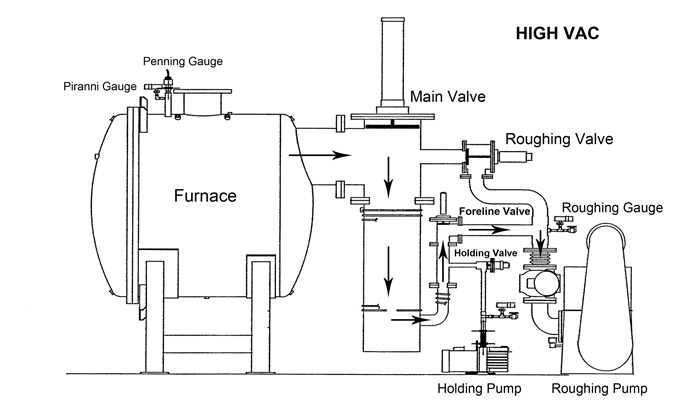
What is a vacuum valve?
A vacuum valve is a device placed in a feed or vent line on a vacuum furnace whose purpose is to isolate the vacuum chamber or direct the flow of gas into the vacuum vessel. These valves can be actuated manually, pneumatically, electropneumatically, electrically or electromagnetically. A series of pressure switches are also installed in most lines with vacuum valves (other than manual valves) to control the flow and changing the internal furnace pressure as demanded by the process being run.
Due to the nature of vacuum, it is necessary to choose a vacuum valve capable of working in the operating vacuum range of the furnace. The knowledge of the application end-use for a given vacuum valve is key to determining the right vacuum valve for the specific application. Examples of design parameters include:
- Size
- Geometry
- Material
- Surface finish
- Vacuum range
- Flow capacity and conditions
- Shutoff response to leakage
- Temperature limits
- Cost
- Actuation method
- Operational speed
- Port configuration
- Conductance
- Suitability, reliability, and durability
- Life span
- Resistance to reaction
- Remote or interlock facility
- Installation
- Ease of cleaning, dismantling and reassembling
- Leak rate (including virtual leak rate)
- Vapor pressure
- Outgassing
Common Types of Vacuum Valves
Roughing and Roughing Vent Valves2
The roughing valve is used when evacuating a vacuum furnace chamber from atmospheric pressure to a so-called “rough” vacuum (typically in the range of 10-2 to 10-3 Torr). In some instances, this level of vacuum is adequate to run the intended process (Fig. 3). In other applications, a diffusion pump is added to the pumping package (Fig. 4) and the roughing pump is used prior to connecting the chamber to the diffusion pump.
The mechanical pump vent valve serves to admit atmosphere to the roughing line, thus “breaking vacuum” and allowing the mechanical pump to return to atmospheric pressure. It is used when shutting down a vacuum furnace pumping system or for maintenance on the pumps or the furnace proper. If present, the diffusion pump is turned off first and allowed to cool, and then the mechanical pump is turned off. Bringing the stopped mechanical pump to atmospheric pressure prevents mechanical pump oil from being drawn back into the foreline. The holding valve and the foreline valve should be closed during the operation, thus keeping the diffusion pump, cold trap and baffle under high vacuum. This assures a clean system when starting up at some later date.
The mechanical pump vent valve serves to admit atmosphere to the roughing line, thus bringing the mechanical pump to atmospheric pressure. It is used when shutting down the system; the diffusion pump is turned off and allowed to cool, and then the mechanical pump is turned off. Bringing the stopped mechanical pump to atmospheric pressure prevents mechanical pump oil from being drawn back into the foreline.
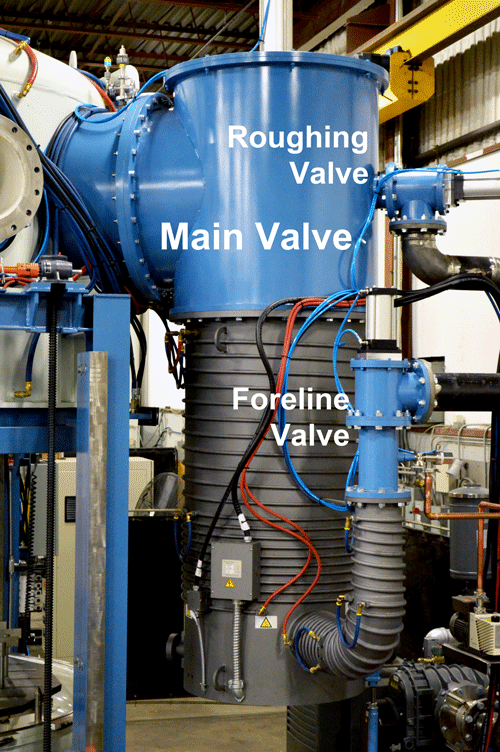

Foreline and Holding Valves2
The foreline valve and the holding valve serve to isolate the diffusion pump, the baffle and cold trap from the roughing line. When roughing has been completed (at approximately 20 mtorr), the roughing valve is closed before the foreline valve and the hi-vac valve are opened. The manifold vent valve admits air to the port manifold to “break” the vacuum and make possible the removal of objects after they have undergone vacuum processing. The roughing valve and the holding valve must be closed during this operation if the pumps on the vacuum system are still in operation. The holding valve and the foreline are usually closed during the operation, thus maintaining the diffusion pump, cold trap and baffle under high vacuum. This assures a clean system when starting up at some later date.
Poppet valves
Poppet valves are standard on most diffusion pump systems operating in a vacuum range down to 10-7 Torr, with 10-4 to 10-6 Torr being a more typical range for most heat treatment processes.
A poppet valve (Fig. 5) consists of a relatively large valve body and an internal poppet that moves linearly when activated (typically by a pneumatically powered actuator). When the poppet is adjusted towards the top of the valve, the body cavity is open to the system and the gas flow is unimpeded, allowing for maximum gas conductance. When the actuator moves the poppet to the bottom of the valve, the sealing ring attached to the poppet is compressed onto the seal surface, stopping gas flow and creating a vacuum-tight seal.
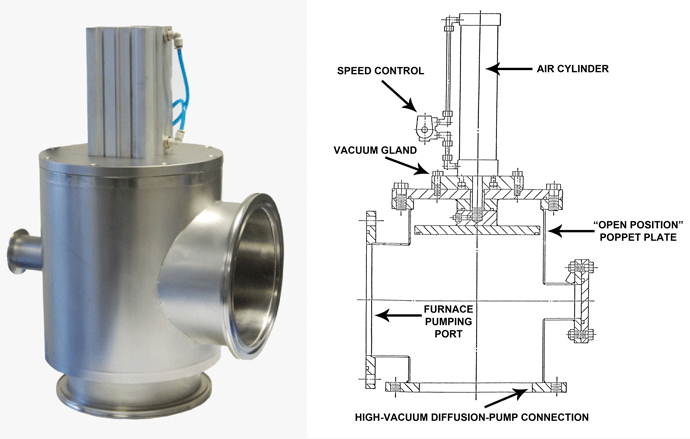
Gate valves
A vacuum gate valve is designed to isolate and seal a vacuum chamber. Gate valves fall into three main categories based on where the valve body is sealed: negative pressure valves, where the valve body is sealed from the vacuum side (i.e., low pressure to high pressure), equalization valves (the pressure of the lines on either side of the valve are equal) and positive pressure valves where the valve body is sealed from the atmosphere side (i.e., high pressure to low pressure).
A gate valve provides straight-through and uninterrupted flow in a typically large diameter. They are characterized by their low flow resistance and compact size and are an ideal valve for furnaces where maximum clearance and flow conductance is needed but space is tight. They typically have an inside diameter range of around 25-300 mm (1-12 inches).
An actuator within the valve can cause a central gate within the body to be either raised, allowing uninterrupted airflow past the valve or lowered, stopping the flow completely. Gate valves can typically seal against a differential pressure in the range of 1.3-13.3 mbar (1-10 Torr).
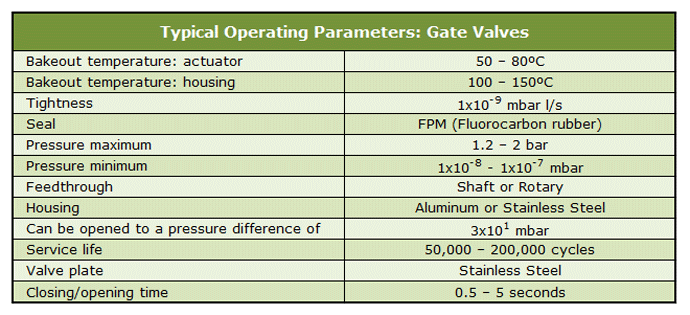
Butterfly or Plate valves
Butterfly valves (aka plate valves) are often used to isolate the vacuum furnace pumping system from the main chamber. These types of valves are subject to repeated, cyclical operation and are highly reliable in service. Their construction consists of a sealing plate that is swung open via a lever or tilted open using a rotary motion with the valve plate remaining in the valve opening. Due to their design, butterfly valves are often used to close rather large openings.
Ball valves
Ball valves are less sensitive than other vacuum valves to particulate contamination, making them the ideal solution for “dirty” vacuum operations. A ball is sealed within the valve’s body by end caps, creating a vacuum-tight central cavity. The valve is opened and closed by turning the stem 90º. Ball valves have a “self-cleaning” feature wherein the sealing seat for the ball wipes the ball clean as it is opened and closed.
Summary
There are many types of vacuum valves, some being used in highly specialized applications. This article presents some of the more common types found on industrial heat treatment furnaces.
References
- Akram, H. M., “Selection of Appropriate Control Valves for Vacuum Systems “, Global Journal of Researches in Engineering: A Mechanical and Mechanics Engineering, Volume 14, Issue 4, Version 1.0, 2014.
- University of California at Berkeley, “Description of a Basic Vacuum System”, EECS 143 Microfabrication Technology. (http://www-inst.eecs.berkeley.edu/~ee143/fa10/lab/vacuum.pdf)
- The Vacuum Technology Book, Pfeiffer Vacuum, 2008.