by J.E. Pritchard & R. Laub
When joining aluminum for aerospace electronics, brazing often is the most practical choice for creating a continuous all-metal joint interface.
Because of its light weight and excellent thermal conductivity, aluminum often is the material of choice for assemblies that house or cool airborne electronics.
Aluminum’s properties are particularly important in combat aircraft. Weight minimization becomes a major design consideration for many components going into these aircraft. Thermal conductivity is especially important in the electronics packages because of the heat problems created by the dense packing of powerful systems in limited spaces. The complex aluminum enclosures, chassis and heat dissipators used in military avionics systems often are manufactured from numerous individual components, which must then be joined.
Selection of a joining process must be based on a thorough analysis of the service requirements and materials involved. For example, the joint’s mechanical strength properties often are critical. A structural joint usually requires good tensile and shear strength as well as resistance to fatigue from cyclic vibrations. Thermal conductivity of the joint is essential for heat exchangers and heat dissipators.
Electrical conductivity also may be important in some applications. In addition, the service environment must be considered, particularly when the joint will be exposed to temperature extremes, moisture or other corrosive media.
In enclosures, shielding sensitive electronic components from electromagnetic interference (EM!) often is critical. Certain joining processes provide joints with better EMI shielding characteristics than do others.
The base metals being joined must be considered. Some aluminum alloys can be joined only by certain processes. Finally, cost always is a consideration. The cost associated with the complexity and quantity of the assembly to be produced usually is the major influence on selecting a joining procedure after all other requirements have been satisfied.
There are a variety of ways to join aluminum. These are the most common:
- mechanical fastening (rivets, screws, etc.)
- adhesive bonding
- welding
- brazing
Mechanical, Adhesive Joining
Mechanical fastening produces a relatively strong joint, often at a comparatively low cost. The process is compatible with all aluminum base metals. Unfortunately, mechanical fasteners often are unsuitable for joining thin sections in soft materials like aluminum because of the base metal’s inadequate strength. Further, because the actual joint interface is localized only to the area immediately surrounding the fastener, the EMI shielding properties of the joint are relatively poor.
Adhesive bonding now is used fairly extensively in joining aluminum for aerospace applications. Modern adhesives are easy to use, cost effective and capable of producing joints with reasonable mechanical strengths in all aluminum alloys.
Metal particles such as aluminum or silver are added to some adhesives to enhance their relatively poor thermal conductivity and EMI shielding characteristics. Adhesive bonding is limited to applications in which service temperatures are relatively low. Exposure to service temperatures greater than about 300°F/149°C reduces the mechanical strength of many adhesively bonded joints. Even after curing, some adhesives deteriorate in the presence of solvents or other chemicals.
As a result of these limitations, mechanical fastening and adhesive bonding often are used in combination with other joining processes rather than on their own.
Welding
In most aerospace applications, joining processes that produce a continuous all-metal joint interface best satisfy mechanical and physical property requirements. A continuous all-metal joint provides substantial mechanical strength and excellent conductivity and EMI shielding. These joints also withstand considerable extremes in service conditions. Welding and brazing are the most common methods for creating a continuous all-metal joint in aluminum alloys. Welding is differentiated from brazing primarily on the basis of the temperatures at which the processes are performed, and the changes that occur in the base metals near the joint.
In welding, temperatures must be sufficiently high to cause localized melting of the base metals in the joint area. Filler metals are not always necessary to form a welded joint. Brazing processes require a filler metal to create the joint and occur at much lower temperatures than welding for any particular base metal. Because of these lower temperatures, the base metal does not melt.
In aluminum, welding creates a joint with a strength that generally is much higher than can be attained through any of the other common joining processes. The melting and subsequent resolidification of the base metal in the joint area can produce a joint with mechanical properties close to that of the base metal itself. Similarly, the physical properties of the welded joint (conductivity, corrosion resistance, EMI shielding) can approximate those of the base metal. Furthermore, most common aluminum alloys are weldable by normal commercial methods.
While the properties of the welded joint would seem to make the welding process the preferred method for joining aluminum, the high temperatures required can cause severe distortion of the base metal components.
Distortion is especially prevalent in arc-welding aluminum. The metal’s excellent thermal conductivity demands a comparatively high localized heat input to successfully make the weld. Coupled with the relatively low melting temperatures of aluminum and aluminum alloys, this high heat input tends to soften the base metals during welding, making them very susceptible to distortion by both mechanical forces and thermal gradients. The distortion problem is especially pronounced when welding very thin sections or components of markedly different section sizes. As a result, arc-welding of aluminum usually is limited to fairly simple but rugged structures.
There are other welding processes for aluminum that require less heat input than arc-welding, thereby lessening the risk of distortion. They include electron beam and laser welding. However, these processes tend to require very careful joint preparation and often are limited to relatively simple part geometries. Also, they tend to be more expensive because special equipment and skilled operators are required.
Brazing
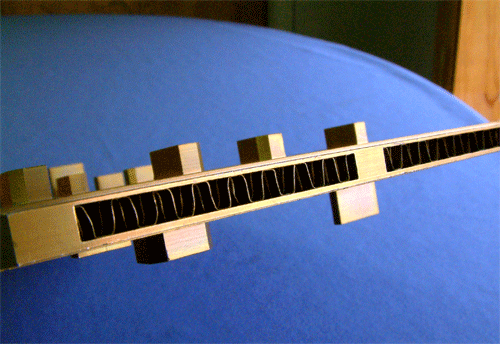
Because of the limitations of welding in many applications, brazing often becomes the most practical choice for creating a continuous all-metal interface when joining aluminum.
Not all aluminum alloys can be brazed. Pure aluminum has a relatively low melting point of about 1200°F / 649°C. When alloying elements are added to improve other properties such as mechanical strength, the melting point is suppressed even further. Aluminum brazing filler metals basically are aluminum-silicon alloys close to the eutectic composition of 12.6 percent silicon with optimum brazing temperatures in the range of 1080°F / 582°C to 1100°F/593°C.
The aluminum alloy most often selected for aerospace applications requiring strength is 6061, which melts at about 1100°F/593°C. Therefore, brazing this material requires careful temperature control, so the base metal will not melt. The most common aluminum casting alloys have melting temperatures below the melting points of available brazing filler metals and cannot be brazed at all.
Aluminum alloys such as 3003 and 1100 contain very little alloy additions and have melting ranges close to that of pure aluminum. These are readily brazable. Unfortunately, due to lack of alloying additions, they have poor mechanical strength and often are unsuitable for many aerospace applications.
There are four common brazing methods for aluminum:
- inert-gas atmosphere
- torch
- dip (molten salt bath)
- vacuum (fluxless)
Aluminum has a very tenacious natural oxide over which braze alloy will not flow readily. Successful brazing of aluminum depends on removing this oxide and preventing it from reforming during the brazing process.
The inert-gas atmosphere, torch, and dip brazing methods involve the use of flux or other activators to promote the flow of the braze alloy. Flux is a material that dissolves or assists in the removal of oxide on the aluminum’s surface. It also prevents the oxide from reforming. However, the flux can be corrosive to aluminum and must be cleaned off thoroughly after brazing.
Brazing in inert-gas atmosphere furnaces is used fairly extensively in the automotive industry. All furnace brazing processes offer the advantages of thorough and uniform heating, which reduces thermal gradients within the assembly and the resulting problems with distortion. In addition, uniform heating of the assembly means that multiple joints can be formed simultaneously.
Inert-gas brazing normally requires fluxes, though certain proprietary processes involve the use of nickel plating to enhance braze alloy flow. Recent efforts have resulted in the development of non-corrosive fluxes that produce consistently acceptable joints when brazing in a dry nitrogen atmosphere. Unfortunately, these fluxes are not compatible with most of the hardenable aluminum alloys such as 6061 and 6951 that usually are specified for aerospace applications. The inert-gas atmosphere brazing process generally is better suited to the high-volume production-line applications common to the automotive industry, rather than the smaller quantities associated with aerospace work.
Most often used for repairs or producing small quantities of simple assemblies, torch brazing usually is a manual operation that requires the application of potentially corrosive fluxes. Because the method involves localized heating, torch brazing can be difficult to control, presenting a greater risk of distortion of the assembly compared to other brazing processes.
Dip brazing involves the immersion of the assembly in a bath of molten flux. As in the furnace brazing process, this provides both thorough and uniform heating of the assembly. Because the bath is composed of a mixture of chemical salts, dip brazing also is referred to as salt-bath brazing.
The dip brazing method begins with chemically cleaning the components to remove surface oxides. The assembled components then are pre-heated in an air-circulating oven before being transferred to the salt bath. During brazing, the molten flux protects the joint surfaces, preventing oxides from reforming. This process produces consistently good joint quality for both simple and complex shapes.
Vacuum furnace brazing is the only process in which flux is not required, which is why this process often is called fluxless brazing. In this method, pre-braze chemical cleaning must be used to remove surface oxides. The subsequent brazing operation is performed in a vacuum, providing an environment relatively free from air and moisture to prevent oxide reformation.
Both the dip and vacuum methods are currently the most practical and popular for joining aluminum in airborne electronics applications, but each method has its advantages and limitations.
Dip Brazing Pros, Cons
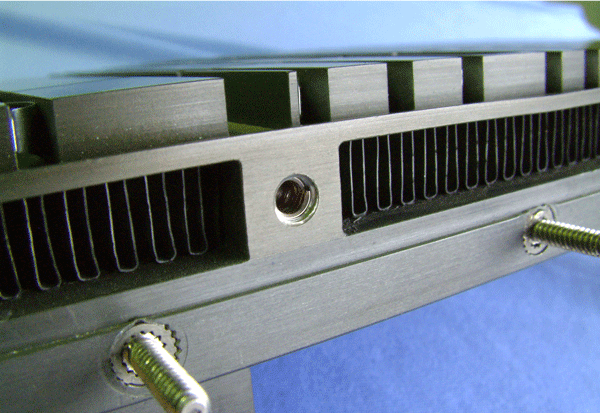
The complete immersion of an assembly in the salt bath during dip brazing ensures that all joint surfaces receive the benefits of the flux. The flux’s protective action enhances the capillary flow of the braze alloy within the joint and the wetting of all mating surfaces.
Dip brazing probably is the best process for creating long vertical joints such as those required in the fabrication of boxes or enclosures. Because the salt supports the structure, the braze alloy tends to stay in a long vertical joint during dip brazing, rather than pooling at a low point, which often happens in other aluminum brazing processes.
In both dip and vacuum brazing, the joint is loaded in compression during the brazing process to control the gap between the mating surfaces. However, because the flux enhances the flow of the braze alloy during dip brazing, control of the joint gap is not as critical. Therefore, the fixturing used to exert the required compressive force can be relatively simple, such as inexpensive spring clips or even dead weights.
When forming joints in multiple orientations, dip brazing is the preferred method. Structures such as complex enclosures or intricate waveguide assemblies usually are dip brazed. The vacuum brazing process tends to be limited to forming joints in parallel planes.
Considering all the factors involved in dip brazing, the method tends to be more economical than vacuum brazing. The inherent and main drawback of dip brazing is the risk of corrosive residues being left on the assembly after brazing. A thorough post-braze cleaning operation is a necessity, usually involving washing with large volumes of hot de-ionized water. This step may be followed by exposure to a humidified environment in an attempt to leach out any entrapped residues.
Despite these operations, it is unlikely that 100 percent of the residual flux will be removed. It can be trapped in narrow channels, in recesses and within the joint itself. Subsequent exposure to moisture can result in corrosion of the aluminum base metal and affect the joint’s integrity. The impact of dip brazing’s limitations can be reduced if a structure is designed for dip brazing.
Designs should allow for easy flux draining as the structure is removed from the bath. Narrow openings or other features that may not be readily accessible during post-braze cleaning should be kept to a minimum. Post-braze machining through brazed joints should be avoided because it may expose previously entrapped salts to moisture and cause corrosion. If post-braze machining cannot be avoided, a further cleaning operation should be performed after machining.
Vacuum Brazing Pluses, Minuses
Vacuum brazing of aluminum has developed into a commercially viable process within the last 20 years. The process differs from other high-temperature vacuum brazing in that it requires specially designed furnaces, which must pump to harder vacuum levels (10-6 Torr range).
The furnaces also must have hot zone designs that allow for rapid heating while maintaining excellent temperature uniformity. In most aerospace applications, vacuum brazing is performed in batch-type furnaces. Semi-continuous furnaces are common in the automotive industry, in which the high quantities of assemblies produced can offset the additional expense of the more complex equipment.
The main advantage of the vacuum braze method is that it does not involve the use of flux, eliminating related corrosion problems. Because there is no risk of corrosive residues on an assembly, after vacuum brazing, there is no need for labor-intensive post-braze cleaning operations. Also, the fumes and chemical wastes generated by the dip brazing process are avoided.
Vacuum brazing is preferred for assemblies with designs making trapped-salt removal virtually impossible, such as liquid-cooled cold plates with narrow internal cooling channels or air-cooled heat dissipators containing intricate radiator fin core.
As with other processes, vacuum brazing has some critical limitations that can be critical.
The process best suits joints in parallel planes that can be brazed horizontally. These usually are flat panel-type structures. Long vertical joints are very difficult to form by vacuum brazing, so assemblies such as boxes and enclosures usually are not suited to this process.
Pre-braze cleaning is especially critical for aluminum vacuum brazing. Because there is no flux, all surface oxides and other contamination must be removed thoroughly prior to brazing.
The cleaning operation usually involves a two-step procedure. The aluminum oxide is reduced to a powdery smut by exposure to caustics or acid. Because the smut adheres to the aluminum, it must be removed by exposure to a second acid, most often nitric acid.
Cleaned parts then are assembled and vacuum brazed as soon as possible because the natural aluminum oxide will start to reform almost immediately. The same cleaning procedure is used prior to dip brazing, but in that process, it is less critical because of the cleaning and protective actions of the flux.
Intimate contact between mating surfaces should be maintained during vacuum brazing. Without the presence of flux to aid the process, the capillary flow of the braze alloy is somewhat limited, making even relatively small joint gaps difficult to bridge. To maintain contact between mating surfaces, complex fixtures often are required, which usually involve some form of heavier spring-loading mechanisms.
Braze filler metals that contain small additions of magnesium have been specially developed for aluminum vacuum brazing. The magnesium in these filler metals vaporizes under vacuum, helping to break up the surface oxide on the aluminum to promote the flow of the braze alloy. The magnesium also offers a secondary benefit of a gettering reaction that removes residual moisture and oxygen from the brazing environment.
Magnesium-bearing braze alloys normally come in the form of a clad sheet with a 3003 aluminum core. Because the core is not hardenable, it usually is unsuitable for aerospace applications. However, with careful control of all brazing parameters, non-magnesium bearing filler metals can be successfully used in the vacuum brazing process. These are widely available clad onto a hardenable base metal core, such as 6951 aluminum.
Overall, the complex equipment and special processing considerations tend to make vacuum brazing more expensive than other aluminum joining processes. However, the benefits it provides by eliminating the problems associated with corrosive fluxes have made it the preferred brazing process for most aerospace applications.
Reprinted from October 1991 issue of HEAT TREATING
Copywrite HITCHCOCK PUBLISHING COMPANY ALL RIGHTS RESERVED