By Jeff Pritchard, Scott Rush and A. Kiela
For maximum fuel efficiency, many gas turbine engine designs depend on sacrificial coatings to tighten internal clearances between moving parts. An extra gap of .005″ between the rotating blades and the engine casing can increase fuel consumption by as much as 0.5%. As fuel comprises more than half of direct operating costs, this waste can be significant. Engine efficiency largely depends on close clearance between blades and casing. Clearance can be affected by a number of engine operating variables, including casing expansion and contraction, loading due to maneuvering, thrust, gust, stall, vibration and manufacturing tolerances. An industrial turbine engine manufacturer (“OEM”) was experiencing unsatisfactory results with the ring segment coatings used to maintain rotor-shroud clearance. Because of poor abradability, the coatings cause excessive wear on the tips of the turbine blades. The OEM and VAC AERO agreed to work cooperatively to develop an improved abradable coating for these applications.
Materials normally used in sacrificial coatings for gas path seals include sintered metal-powder segments, sintered metal-fiber segments, metallic honeycomb (filled and unfilled), elastomers and thermally sprayed abradable coatings. Thermally sprayed coatings offer advantages over the other materials, including direct application, easy removal, and repair, variety of coating materials and good performance. New abradable thermal spray coating materials have been proposed for performance in industrial turbine engines at operating temperatures up to 980°C.
An investigation of a variety of these new materials was undertaken in order to quantify their performance during cyclic oxidation burner rig testing, hot corrosion burner rig testing and hot abradability rig testing as compared to existing abradable coating technology. Based on the results of these tests it was concluded that a significantly improved coating for abradable seals in industrial gas turbine engines was developed. This new coating can prevent excessive blade tip wear between 24,000-hour inspection intervals at operating temperatures up to 980°C. The successful coating consists of a specially heat treated MCrAIY bond coat, applied by HVOF, covered with a proprietary abradable top coat, applied by air plasma spray.
Two of the most important properties of a good abradable coating are hardness and lubricity. A good coating will not be so hard that it causes wear of the material by which it is being rubbed, nor so soft that it can be easily eroded by particulate matter contained in the engine gas stream. Lubricity is a characteristic that allows the rubbing material to smoothly cut into the abradable coating, rather than tearing it away in large pieces. The coating must also have satisfactory high-temperature oxidation and corrosion resistance for protection of the substrate to which it is applied. For abradable applications, powders containing a combination of metallic and non-metallic constituents are favoured. The metallic constituent forms the matrix in the coating and provides most of the protection for the substrate. The non-metallic additives provide lubricity and can also be used to create porosity in the coating, which further enhances abradability. The coating developed by VAC AERO meets all of these requirements and has now been proven in thousands of hours of engine service.
The OEM recommends that an engine undergo a gasflow path inspection after every 8,000 hours of operation. Gasflow paths are visually inspected for erosion, foreign object damage and excessive deposits of engine residues. This inspection is considered comparatively minor. It does not require major disassembly of the engine and is therefore relatively inexpensive. After every 24,000 hours of operation, a comprehensive inspection is performed which does involve major disassembly of the engine. The 24,000-hour inspection is labour intensive and much more expensive to perform than the gasflow path inspection.
In past experience from these inspections, the OEM determined that blade tip wear due to abrasion against sealing surfaces often reaches unacceptable levels by 16,000 hours of operation (under some operating conditions, even by 8,000 hours). In addition to tip wear, cooling holes in blade tips may become blocked by coating torn from the sealing surface. As the coating deteriorates, the ring segments that form the sealing surfaces may also suffer from severe degradation due to oxidation and corrosion. When severe damage is detected during a gasflow path inspection, major dis-assembly of the engine is required to replace worn components.
Under more preferable circumstances, replacement of damaged components would not be required until at least 24,000 hours of operation. Worn blades or ring segments can be replaced more cost-effectively during the major disassembly that takes place during the 24,000-hour inspection. For this reason, a 50% improvement in blade tip wear is an attractive target. Such an improvement would equate to an extension of blade life until the 24,000-hour inspection and reduce the high costs associated with replacing blades prior to the scheduled disassembly of the engine. Ideally, blade tip wear would be entirely eliminated by improving the abradability of the coating on the sealing surface. An improved coating would also minimize early corrosive damage of the ring segments that form the casing.
The primary technical objective of this research was to develop an abradable coating to eliminate blade tip losses due to abrasion against sealing surfaces. However, the project would be considered successful even if blade tip losses could be reduced by 50% as compared to losses experienced with existing coatings. Several candidate compositions for an improved abradable coating were developed. Evaluations of the candidate coatings were conducted using laboratory tests with benchmarks for comparison.
Selection of Candidate Coatings
The gas flow path seal coatings currently in use by the OEM are standard MCrAIY compositions applied by shrouded plasma or high-velocity oxygen fuel (HVOF) spray to a total thickness of about 1.5mm. While these coatings provide satisfactory protection to the substrate against hot oxidation and corrosion, they have poor abradability and cause excessive blade tip wear during engine operation. The engines operate at a steady state temperature of about 985ºC. The OEM believes that most blade tip rubbing occurs during engine startup and shutdown cycles at temperatures between 650º and 815ºC.
Two of the most important properties of a good abradable coating are hardness and lubricity. A good coating will not be so hard that it causes wear of the material by which it is being rubbed, nor so soft that it can be easily eroded by particulate matter contained in the engine gas stream. Lubricity is a characteristic that allows the rubbing material to smoothly cut into the abradable coating, rather than tearing it away in large pieces. The coating must also have satisfactory high-temperature oxidation and corrosion resistance for protection of the substrate to which it is applied. For abradable applications, powders containing a combination of metallic and non-metallic constituents are favoured. The metallic constituent forms the matrix in the coating and provides most of the protection for the substrate. The non-metallic additives provide lubricity and can also be used to create porosity in the coating, which further enhances abradability.
Based on a literature survey and consultations with a major powder manufacturer, it was concluded that coatings with an MCrAIY matrix and additions of lubricating and volatile elements (to create porosity) held the most promise for abradable applications in the intermediate range of engine operating temperatures. To ensure that the substrate had hot oxidation and corrosion protection at least equivalent to the coatings currently in use, an MCrAIY bondcoat was applied beneath the abradable top coat. Three powder compositions were selected as candidate abaradable top coats. The amounts of MCrAIY matrix and the lubricating element in each of the compositions were fixed. To determine the effect of porosity level on performance of the abradable top coat, the amount of the volatile element was varied to yield three different porosity levels.
Experimental Procedure
The MCrAIY bond coat was applied by HVOF to L605 base metal coupons. L605 is a readily available cobalt base alloy very similar to that used on the OEM’s ring segments. Spray parameters, coating thickness and post-spray vacuum fusing treatment parameters were developed to achieve a coating with mechanical properties exceeding the OEM’s requirements. All bond coat deposits were evaluated for microstructure, superficial hardness, and bond strength. Each was also subject to a Furnace Cycle Test involving repeated exposure to a temperature of 982ºC in an unprotected air atmosphere followed by fan cooling. The deposits were inspected after each exposure for spallation and general deterioration.
The abradable top coat materials selected for evaluation were designated VA/TC1, VA/TC2, and VA/TC3. The powder used to produce the VA/TC1 coating contained the least amount of the volatile constituent, while that used to produce VA/TC3 contained the most. In addition, two MCrAIY top coats were prepared for evaluation, one applied by HVOF and the other applied by air plasma spray. These MCrAIY top coats were not considered to be “abradable” and were included only to demonstrate that VAC AERO was capable of applying an MCrAIY coating equivalent to the OEM’s current coating. The MCrAIY top coats were designated VA/MC1 (applied by HVOF) and VA/MC2 (applied by air plasma spray). Spray trials were conducted to determine optimum spray parameters for each coating composition. As a benchmark in these evaluations, the OEM provided coupons sprayed with a coating representative of that currently in use in the engine. The benchmark coupons were subject to the same tests as the candidate coatings. The benchmark coating supplied by the OEM was designated WB.
All top coat conditions were subject to a high-temperature exposure test of 982ºC for approximately 200 hours. At intervals during the exposure, the coatings were inspected for superficial hardness and porosity content. All coatings were then subject to separate oxidation and hot corrosion tests on a burner rig and compared to the performance of the benchmark coating in the same tests. Burner rig tests were performed by the National Research Council of Canada using test parameters specified by the OEM. Hot abradability testing of each coating was also performed. The test involves rubbing a vane tip specimen against a coated coupon at simulated engine RPM and operating temperature. During revolution, the test rig forces the vane tip into the coating at a controlled incursion rate that simulates the thermal expansion conditions in the engine. The vane tip is then measured for wear and the coating evaluated for deterioration. Two sets of test conditions were evaluated during hot abradability testing. The first simulated temperatures and incursion rates during engine start-up, the second simulated engine steady state operating conditions.
Data from all tests was then evaluated to compare the performance characteristics of the candidate coatings to those of the benchmark coating.
Results and Discussion
Prior to application of the MCrAIY bond coat, the surface of the substrate was properly prepared to ensure good coating adhesion. Numerous spray trials were performed to establish the optimum parameters for the application of the MCrAIY bond coat. These parameters produced an as-sprayed bond coat with microstructural properties meeting the OEM’s requirements for MCrAIY coatings. Vacuum fuse trials. were conducted and optimum fusing parameters determined to produce a coating bond strength exceeding 10,000 psi when tested per ASTM C633. Using the optimum bond coat spray and fusing parameters, a number of coupons were coated. These were then subject to furnace cycle testing along with coupons coated with the benchmark coating. Based on visual observations, no spallation or degradation of the bond coat or benchmark coatings was apparent through more than 100 cycles. It was concluded that VAC AERO had developed an MCrAIY bond coat with properties at least equivalent to the coating used by the OEM. Parameters for the application of the bond coat were then fixed for subsequent topcoat development trials.
Due to the presence of the volatile element in the abradable top coat powders, air plasma spray was considered the best technique for applying these coatings. Optimum spray parameters were established based on coating appearance, superficial hardness, bond strength (measured by bend test) and microstructure. Porosity content varied extensively among the three abradable top coats, with the volume fraction of porosity increasing with increasing concentration of the volatile constituent in the powder. The abradable top coats were first evaluated through a high-temperature exposure test at 982ºC. At intervals through 200 hours of exposure, the coatings were examined for changes in porosity and superficial hardness. There was some concern that continuous long term exposure would result in increased levels of porosity and reduced hardness. Both of these conditions were expected to have a detrimental effect on abradability. However, analyses showed no significant changes in porosity or hardness throughout the 200-hour exposure.
Based on these analyses, it was concluded that optimum spray parameters had been developed for the three candidate abradable coatings. Using these parameters, coupons for burner rig and hot abradability testing were prepared for each coating. After spraying, the abradable coatings were subject to a burnout cycle in an unprotected air atmosphere. This treatment was performed to vaporize the volatile constituent from the coatings prior to further testing.
Burner Rig Testing
The burner rig at the Institute of Aerospace Research of the National Research Council of Canada is used for endurance testing of turbine hot section components. Testing is done in a high-velocity hot gas generated by a laboratory combustor system that closely simulates the mixing, flow and combustion chemistry of fuels in turbine combustors. Two types of burner rig tests were conducted to evaluate the properties of the candidate coatings. The first was a cyclic oxidation test simulating the thermal stresses to which the coatings would be exposed through multiple engine startup and shutdown cycles. The coatings were subject to 1,000 cycles, each cycle involving four minutes exposure to the burner rig gas stream followed by two minutes forced air cooling. At intervals, the coupons were measured for weight change. The temperature of the gas stream was 1210ºC, which generated a coupon temperature of approximately 970ºC.
The results of the cyclic oxidation test are shown in Figure 1. The test measures weight change of a test coupon versus the number of cycles. For a coating with perfect oxidation resistance, there would be no weight change in the test coupons through exposure to an indefinite number of cycles. In reality, a slight weight increase of the test coupon is normally evident during early cycles. This occurs as a result of oxidation of certain elements in the coating and coupon base metal. Subsequently, a decrease in weight becomes evident as the oxides begin to spall off of the coupon. A low rate of weight loss is an indication of good oxidation resistance.
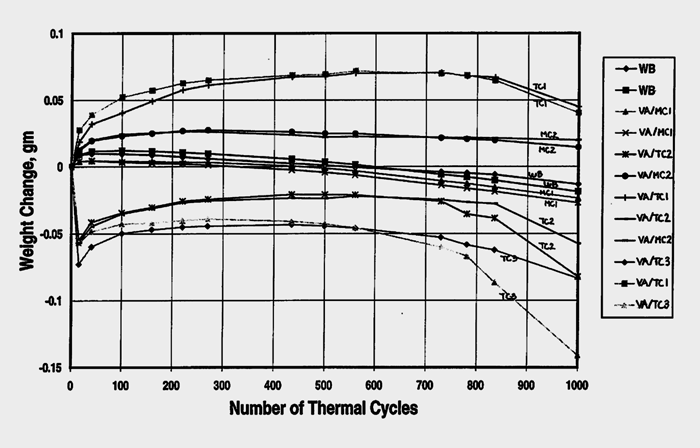
Two samples were tested for each candidate coating with excellent reproducibility of test results. The MCrAIY coatings (WB, VA/MC1, and VA/MC2) all showed relatively similar results. Oxidation resistance for the benchmark coating (WB) and the VAC AERO MCrAIY top coat applied by HVOF (VA/MC1) was virtually identical. Both coatings registered very slight weight gains in the first 50 to 100 cycles and a very gradual weight loss through the final 100 cycles. The VAC AERO MCrAIY top coat applied by air plasma spray (VA/MC2) showed a higher weight gain through the first 250 cycles, but a smaller weight loss through the final 750 cycles. Based on these results, it can be concluded that the VA/MC2 coating will provide the best long term protection from hot oxidation of the three MCrAIY coatings, though VA/MC1 can also be considered at least equivalent to the benchmark.
As expected, the abradable coatings (VA/TC1, VA/TC2, and VA/TC3) did not perform as well in long term exposure as the MCrAIY coatings. VA/TC2 and VA/TC3 actually showed weight losses through the first 15 to 20 cycles. However, this loss can be attributed to vaporization of the residual volatile element in the coating and is not a sign of early coating deterioration. The size of the early weight loss was directly proportional to the amount of volatile element in the powder used to make the coating. The abradable coatings then exhibited a fairly fast rate of weight gain through 200 cycles and relatively stable performance through at least 500 cycles. VA/TC3 then began to show signs of deterioration which accelerated past 700 cycles. VA/TC1 and VA/TC2 both remained stable through more than 700 cycles before deterioration began.
The OEM advised that most industrial turbine engines undergo only a limited number of startup and shutdown cycles between major overhauls. In most cases, this number is less than 10 cycles and rarely exceeds 200 cycles. Based on these operating criteria and the results of the cyclic oxidation tests, it was concluded that all of the coatings demonstrated satisfactory hot oxidation resistance for the intended application. It should be also emphasized that the abradable coatings are applied as an overlay on an MCrAIY bond coat. The bond coat will provide most of the protection for the substrate.
The second burner rig test to which the candidate coatings were subject was hot corrosion testing. This test simulates longer term exposure of the coating to corrosive elements in the engine gas stream. Test coupons are cycled through the burner rig gas stream for periods of three hours at a time followed by forced air cooling for three minutes. Weight change is measured at intervals as a function of exposure time through a total test duration of 100 hours. Salt water is added to the gas stream to increase its corrosiveness. A sulphidized fuel is also used to further enhance the corrosive effect. In the hot corrosion test, a gas stream temperature of 1040ºC created a coupon temperature of approximately 900ºC. The coupon temperature was slightly less than the engine steady state operating temperature of 985ºC. However, past experience with the burner rig has shown that corrosive action is more pronounced at this lower temperature.
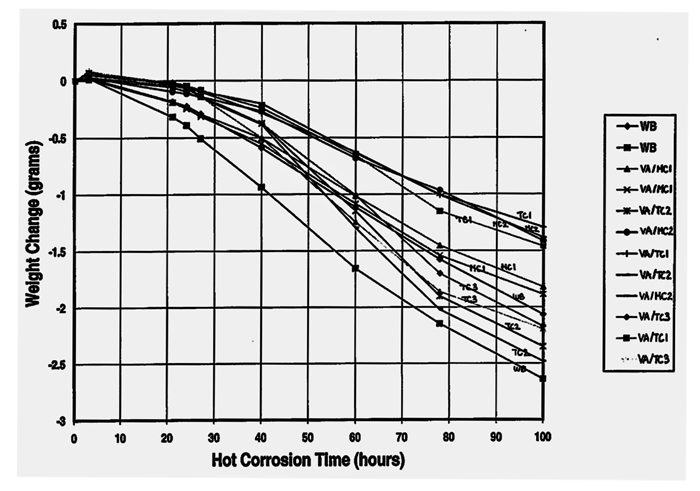
Figure 2 shows the results of the hot corrosion test. Two samples for each candidate coating were tested. With the exception of the benchmark coating, performance results were again very reproducible. Among the MCrAIY coatings, the VAC AERO MCrAIY top coat applied by air plasma spray (VA/MC2) exhibited the least weight loss, followed by the VAC AERO MCrAIY top coat applied by HVOF (VA/MC1). Combined with results from the hot oxidation test, these findings confirmed the conclusion that VA/MC2 has better hot oxidation and corrosion resistance properties than the OEM’s current MCrAIY coating.
Results for the abradable top coats were somewhat mixed with VA/TC3 showing a higher weight loss than VA/TC1 but less than VA/TC2. From these results, no definitive conclusions can be drawn regarding the effect of varying concentrations of the volatile constituent in these abradable coatings on hot corrosion resistance. However, the results did show that each of these coatings underwent weight losses no worse than that of the benchmark coatings. It can, therefore, be concluded that their corrosion resistance will be satisfactory for the intended application. In summary, burner rig testing demonstrated that in the intended application, substrate protection equivalent to the benchmark coating could be achieved with the use of any of the candidate coatings.
Hot Abradability Testing
The final test used in the evaluation of the coatings was hot abradability testing performed by an independent laboratory. The hot abradability test simulates the rubbing of blade tips against the coated casing as occurs during engine service. A schematic of the test rig is shown in Figure 3. The rig consists of a rotor, movable specimen stage, and heating device. The rotor is a steel disc with four machined slots spaced 90º apart, into which dummy blade tips are fitted. Blade tip velocity can be varied up to 500 m/s. The specimen stage is driven by a stepper motor and is used to force the coated coupon into the moving rotor. Incursion rates can be accurately controlled between 1 and 500 µm/s. The coupon surfaces are heated by a high-velocity burner creating a thermal gradient similar to that in an engine. Test temperatures can be varied between ambient and 1200ºC. The rig is microprocessor-controlled and test parameters are collected through a high-speed datalogger. Abradability results are determined by measuring incursion depth of the blade into the coating, blade wear, and abradable roughness.
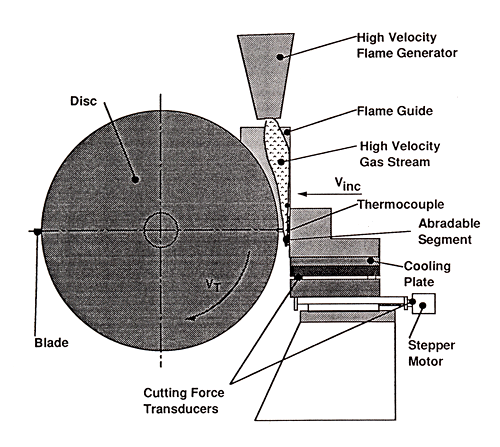
Testing demonstrated that the benchmark MCrAIY coating (WB), VAC AERO’s MCrAIY coating (V AlMC2) and the “abradable” coating containing the least amount of the volatile constituent (VA/TC1) had poor abradability under both sets of test conditions. These results were not surprising and served to confirm the practical experience of the OEM. At the lower test temperature, these coatings suffered from considerable adhesive wear with significant transfer of the coating material onto the blade tip. At the higher test temperature, these coatings became more plastic causing melting wear of the blade and little adhesive transfer. The dummy blade tips were made from IN738, the same blade material in the OEM’s engines. Two sets of test parameters were selected to simulate two engine operating conditions. A test temperature of 700ºC, incursion rate of 10 11m and blade tip velocity of 400 m/s were used to simulate engine start-up conditions. To simulate engine steady state conditions, a test temperature of 985ºC, incursion rate of 2 JlID and blade tip velocity of 400 m/s were used. Two benchmark coupons and two coupons coated with each of the abradable top coats were tested under both sets of conditions. Two coupons coated with V AlMC2 were tested only at the lower temperature for comparison to the benchmark.
VA/TC2, based on the powder containing an intermediate amount of the volatile constituent, showed partial abradability at 700°C. However, the abradability was a result of break out of chunks of coating rather than a more desirable cutting mechanism. In a turbine engine, the creation of larger chunks of the coating during abrasion increases the risk of cooling hole blockage in vane tips. At 985°C, VA/TC2 became more ductile causing blade wear and no incursion into the coating.
VA/TC3 showed good abradability under both sets of test parameters. No transfer of coating to the blade tip was evident and the abraded surface was very smooth. No measurable blade tip wear occurred at 700°C and only minor wear was measured at the higher temperature. Based on measurements of blade tip wear, the hot abradability of VA/TC3 was much more than 50% better than the benchmark coating at both test temperatures. Though the results of these laboratory tests should be confirmed by engine testing, it appears that the VA/TC3 coating would prevent excessive blade tip wear between major engine overhauls. These tests demonstrated that VA/TC3 had far better hot abradability than the benchmark coating and the best hot abradability of the three candidate abradable coatings. Combined with the results from the burner rig tests, it is apparent that a much-improved engine casing coating can be achieved by applying an MCrAIY bond coat covered with an overlay of abradable top coat VA/TC3.
Conclusions
Based on the results of laboratory tests, a significantly improved coating for abradable seals in industrial gas turbine engines has been developed. It is expected that this coating would prevent excessive blade tip wear between 24,000-hour inspection intervals at operating temperatures up to 980°C. The coating consists of a specially heat treated MCrAIY bond coat covered with a proprietary abradable top coat. The results of the laboratory tests will be confirmed through actual engine testing.