BY JEFF PRITCHARD
When heat treating or brazing in vacuum, the vapor pressure of the constituents in the materials being processed can be a very important consideration.
The vapor pressure of a material is that pressure exerted at a given temperature when a material is in equilibrium with its own vapor. Vapour pressure is a function of both the material and the temperature. Figure 1 shows approximate vapor pressure curves for a variety of metals and compounds. The area to the left of each curve represents the conditions of temperature and pressure under which the material exists as a solid. The area to the right of each curve represents those conditions under which the material exists as a gas (or vapor).
For example, in studying the curve for copper (Cu), it becomes evident that heating this metal to a temperature above about 1010ºC (1850ºF) in a vacuum of 10-4 torr or better will cause the copper to vaporize from a solid to a gas. Vaporization of copper will occur at even lower temperatures in better vacuums. Zinc, a common alloying element in brass, vaporizes at such low temperatures that brass is rarely processed in vacuum furnaces. Elements in brazing alloys (particularly silver and copper-based braze alloys) can also be prone to vaporization during vacuum processing, particularly at temperatures near the melting point of the braze alloy. Vaporization can change the chemistry of the alloy being processed and affect its properties. Furthermore, the vapours of volatile elements will eventually condense on colder surfaces within the furnace, creating the potential for other problems with electrical failures and contamination.
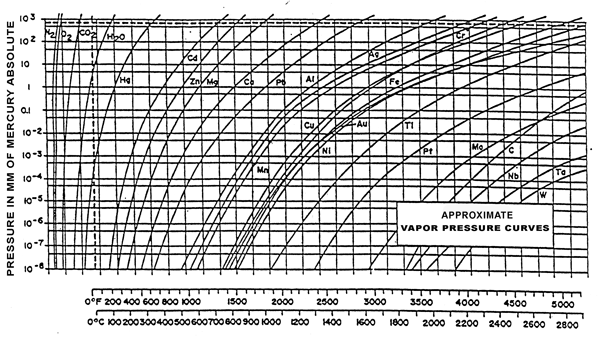
All modern vacuum furnaces are equipped with a partial pressure capability. Knowing when to use this capability will help the processor produce a better end product and extend the service life of the furnace.
To prevent the vaporization of volatile elements during vacuum processing, a partial pressure of an inert gas, such as argon or nitrogen (or even hydrogen), can be introduced to the furnace chamber. The partial pressure is that portion of the total pressure exerted by each gas constituent within the system. By bleeding an inert gas into the chamber, the overall pressure is increased (the vacuum is decreased) and the vaporization can be prevented even at higher temperatures. An inert gas like argon will not react with the alloy being processed so control of the surface chemistry of the alloy can be maintained. However, because of the expense of the gas, heat treating with partial pressures tends to be more costly than processing in a straight vacuum. Partial pressures are usually introduced at temperatures well above ambient during the heat treating cycle. This procedure ensures the removal from the furnace chamber of any residual impurities (such as entrapped moisture) during the initial pump-down and heat-up sequence.