Knowledge of vapor pressure and rates of evaporation of various materials is valuable information for those operating vacuum furnaces, whether we are heat treating or brazing at high temperature and low vacuum levels or dealing with outgassing at very low temperatures and pressures.
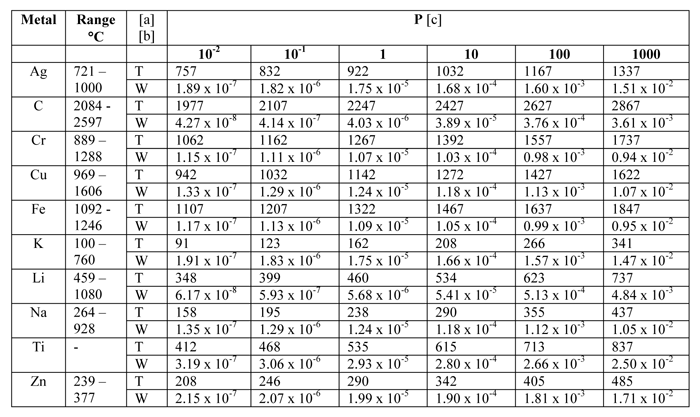
Notes [a] T = temperature, °C [b] W = rate of evaporation in grams per square centimeter per second [c] P = vapor pressure, microns
When we think about a solid or liquid in a sealed vessel, we find that, even at room temperature and atmospheric pressure, there are molecules that leave the surface and go into the gaseous phase. The gas phase thus formed is called a vapor. The process of forming a vapor is known as evaporation and the rate of evaporation is determined by the temperature of the substance involved. In time, some of the evaporated molecules will, in all likelihood in the course of random movement, strike and stick to the surface of the vessel. This process is known as condensation and the rate of condensation is determined by the concentration of gas molecules (that is, the pressure of the evacuated gas). Eventually, the number of molecules leaving the surface of the substance is equal to the number returning to it (that is, the evaporation rate equals the condensation rate) and we have dynamic equilibrium. The (partial) pressure at which this occurs is known as the vapor pressure of the substance.2 Below this pressure, surface evaporation occurs faster than condensation, while above it, surface evaporation is slower.
Vapor Pressure
The vapor pressure in a vacuum system is only dependent on the temperature and can be expressed in general terms as
where
P = vapor pressure
T = temperature
A, B = constants (associated with each element present)
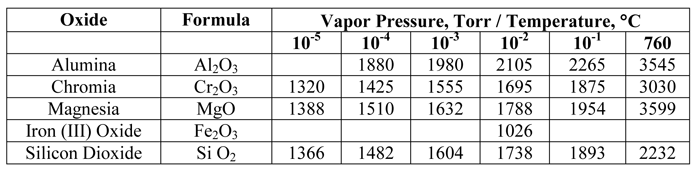
When dealing with vacuum applications, it is important to know how the partial pressure changes for certain solids and liquids present in a vacuum environment (Table Nos. 1 – 4). In practice, however, we often find that our operating ranges are 1 – 2 orders of magnitude higher than calculated and/or experimental values to compensate for real-world conditions.
Material that we readily associate with having low boiling points (e.g. water, oils, greases) can be expected to give us trouble in a vacuum environment. Surprisingly, other materials, including most forms of rubber, plastics, and certain insulating materials can also readily break down. Knowing the vapor pressure characteristics of a number of fairly common materials used in and around vacuum systems can be quite helpful.
![Table 31 - Characteristics of Selected Solids in Vacuum Notes: [a] Data not available.](https://vacaero.com/wp-content/uploads/2014/09/charact-selected-solids_lg.gif)
Notes: [a] Data not available.
Evaporation
Evaporation is the process of molecules leaving a liquid state and going into a gaseous state. The liquid state arises because molecules are attracted to each other, making the condensed state lower in energy than the gaseous state. To form the condensed state from the gaseous state, the molecules need to give off energy in the form of heat. To form the gaseous state from the condensed state, the reverse must occur, that is, the system must absorb heat. That’s why evaporation has a cooling effect. The reason that different liquids evaporate differently is that the attractions between molecules are different for different substances.
The maximum evaporation rate can be expressed by the formula:
where
Qmax = maximum evaporation rate, in g/cm2-s
Pv = vapor pressure, in Torr
T = temperature, in °K
M = molecular weight of the substance
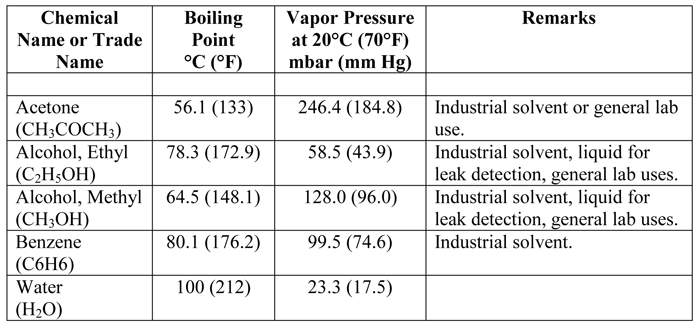
Here the dependence on temperature is due to the variation in vapor pressure with temperature (which is nearly logarithmic). Thus, the rate of evaporation is greatest in high vacuum.
A Practical Example
Moisture in the form of liquid water has always been considered problematic in vacuum furnaces and is an issue often arising from improperly dried loads or high humidity environments, The longer the chamber is open and the more humid the ambient air, the more water will enter the chamber (Fig. 1) with water vapor molecules depositing on the internal vessel surfaces (chamber walls, insulation, etc.). This will result in a longer and slower pumpdown than normal, which is why we want to keep vacuum furnaces closed and under vacuum when not in use and load/unload as quickly as possible in actual operation. The more water absorbed, the more time and effort will be required to rid ourselves of it.
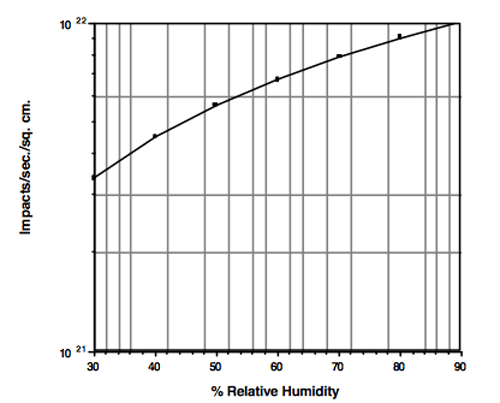
The vapor pressure of water is 9 Torr at 10°C. That is, at 9 Torr the rate at which the water is changing to the vapor phase (i.e., the evaporation rate) is equal to the rate at which the vapor is changing to the liquid phase (i.e., the condensation rate). Hence any change in temperature causes a change in both the evaporation rate and the condensation rate until a new equilibrium is reached. As the temperature increases, for example, to 20°C the vapor pressure of water increases to 17.5 Torr, while at 30°C the value is 31.8 Torr (it should be noted that the vessel does not have to be evacuated for this to occur; the partial pressure due to the water vapor will rise to this level provided there are no chemical reactions taking place). 2
If one were to pump on the vessel, the water present in the gas phase would be removed at a fixed rate (depending on temperature), but equilibrium would never be reached (since most of the molecules would have evaporated and have been evacuated before they could condense).
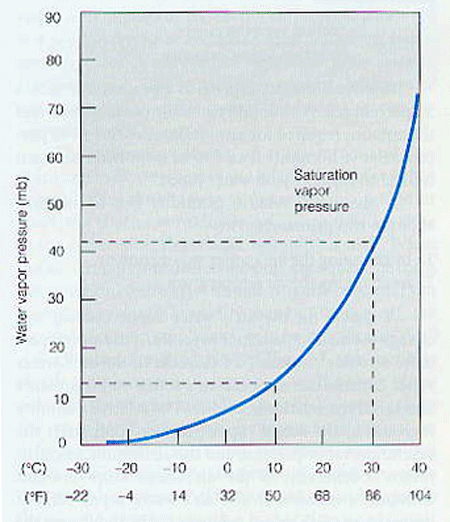
In Summary
Understanding partial pressure and evaporation in vacuum furnaces is an important aspect of vacuum technology both in heat treatment, brazing and coating (deposition) technology. Once we understand these phenomena, we can use partial pressure to control these reactions6, 7.
References
- Herring, Daniel H., Vacuum Heat Treatment, BNP Media Group, 2012.
- Brunner, Jr., William F., Practical Vacuum Techniques, Robert E. Krieger Publishing Co., Inc., 1965.
- Dushman, Saul., Scientific Foundations of Vacuum Technique, Second Edition, 1962.
- Critical Melting Points and Reference Data for Vacuum Heat Treating, Virginia Osterman and Harry Antes Jr. (Eds.), Solar Atmospheres, 2010.
- Danielson, Phil, Understanding the Effects of Air Exposure, A Journal of Practical and Useful Vacuum Technology, The Vacuum Lab, 2005.
- Herring, Daniel H., Using Partial Pressure in Vacuum Furnaces, Industrial Heating, November 2005.
- Herring, Daniel H., When to Use a Partial Pressure in a Vacuum Furnaces, Vacuum Technology Series, Vac-Aero International, 2012.