A residual gas analyzer or RGA for short (Fig. 1) is a compact mass spectrometer, designed for use either in the laboratory or out on the shop floor. These devices are often mounted for in-situ use on a vacuum furnace (Fig. 2). RGA’s are typically designed for process control and contamination monitoring in vacuum systems.
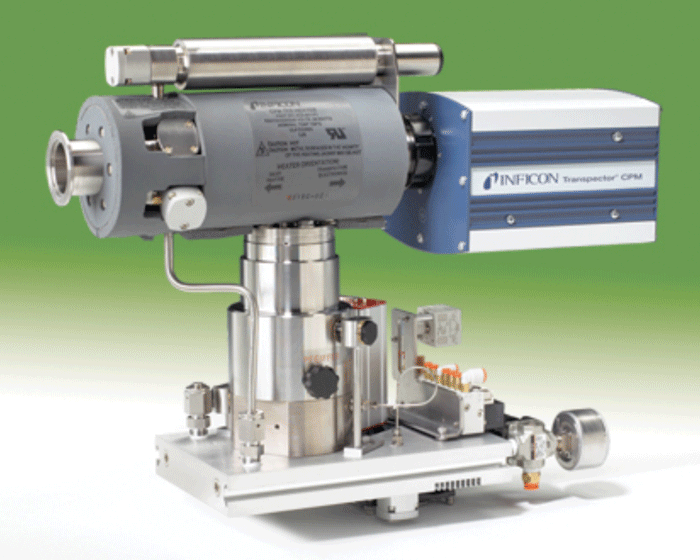
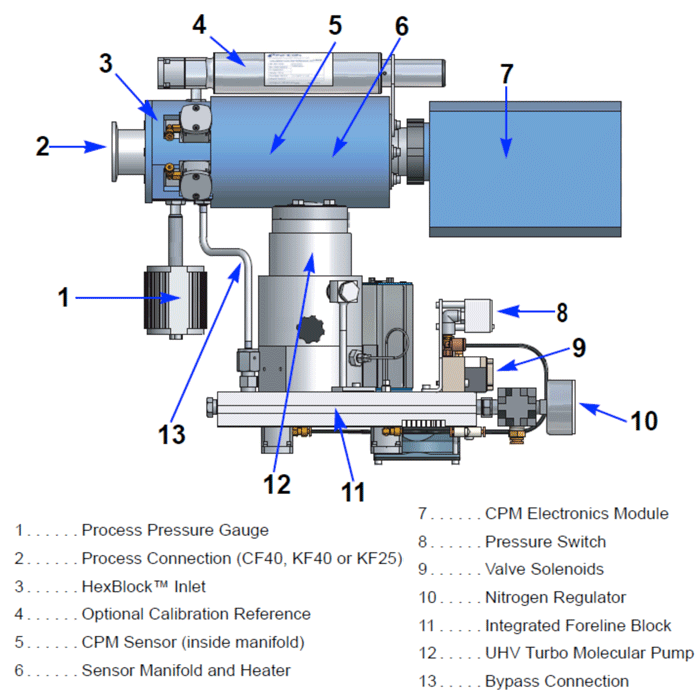
Applications for residual gas analyzers include distinguishing leaks from outgassing, fingerprinting the process background, detecting helium and determining the effectiveness of gas line purging. A typical RGA gas analysis can reveal how much of a particular species is present either in the vacuum vessel or in the pump manifold (Fig. 3).
RGAs are used in most cases to monitor the quality of the vacuum and easily detect minute traces of impurities in the low-pressure gas environment. These impurities can be measured down to 10-14 Torr levels, possessing sub-ppm detectability in the absence of background interferences.
RGAs can also be used as sensitive in-situ, helium leak detectors. With vacuum systems pumped down to lower than 10-5 Torr for checking of the integrity of the vacuum seals and the quality of the vacuum to detect air leaks, virtual leaks and other contaminants at low levels before a process is initiated.
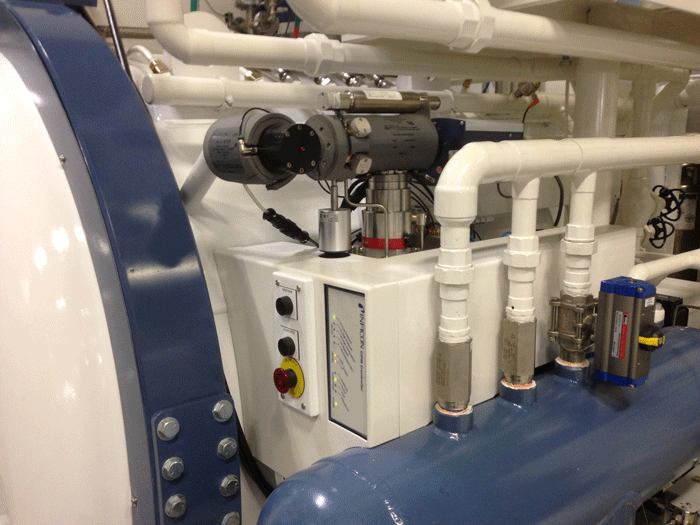
Distinguishing Leaks from Outgassing
A basic RGA scan from mass 2 to 50 atomic mass units can usually identify excessive outgassing (i.e. high peaks for water at mass 17 and 18) from a leak – high peaks at 14 & 28 (nitrogen), and sometimes 32 (oxygen). Other indicators of an air leak are argon (40) and carbon dioxide (44), Often the oxygen peak is missing or very low, even if there is an air leak. Helium, for example, will show up at mass 4.
Fingerprinting
An RGA scan of the vacuum system (see Figure 1) prior to running a process can provide valuable insights into the condition of the vacuum vessel. When problems occur (and they invariably do), having a baseline for comparative purposes is extremely helpful.
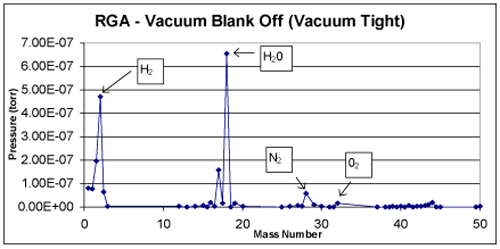
How It Works
The Residual Gas Analyzer consists of an ion source, a mass spectrometer, and a measurement section (Fig. 4). The residual gas is ionized when it collides with the thermoelectrons discharged from the high-temperature filament, and the ions that are thereby created accelerate and converge onto the mass spectrometer. At the mass spectrometer, direct and alternating current voltages are applied to the four cylindrical electrodes (quadropoles), which allow the ions to be separated by mass. The separated ions are detected as electric current by the Faraday cup. The ion current is proportional to the mass (partial pressure) of the residual gas.
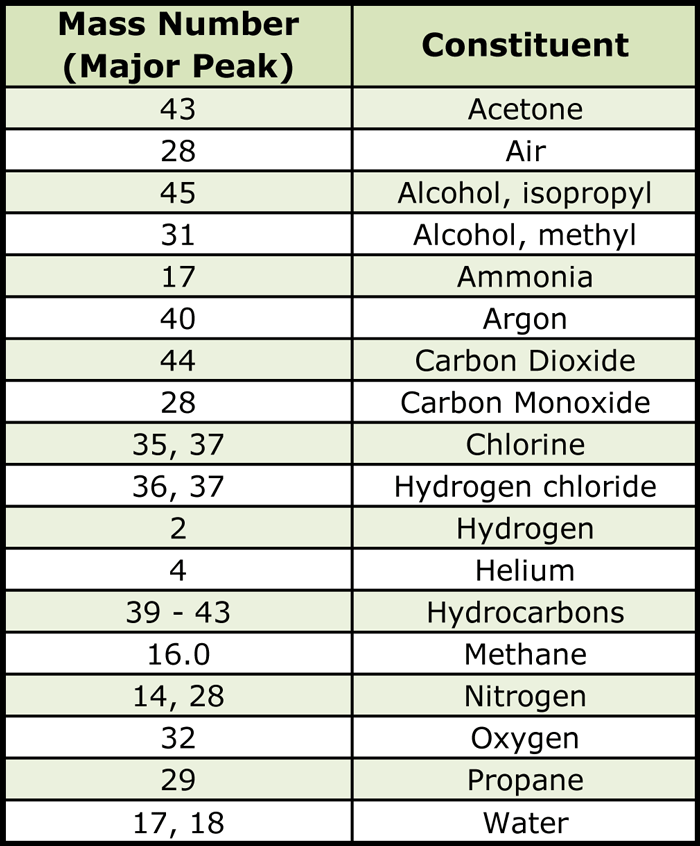
More specifically, the operation of an RGA is conceptually quite simple although the mathematics of the quadrupole mass analyzer section can become too complex for many undergraduates to appreciate. This operation is diagrammed in Figure 1. First, an “ionizer” converts many neutral gas molecules into positive ions in a well-controlled region at a specified electric potential. These ions are next accelerated by a series of electrostatic “lenses” and formed into a beam that has about 20 eV of energy. The ion beam is subsequently passed into the quadrupole mass analyzer region. This region acts as a filter. It will very nicely pass through ions with a user-chosen mass to charge ratio (M/e), but all the other ions get pushed aside into walls where they neutralize and become undetectable. The ions that are passed through this filter are detected as current either at a “Faraday cup” or using a secondary electron multiplier (also known as a “channeltron”). The channeltron gives a large amplification of the signal from ions and consequently is used to enhance the sensitivity of the RGA. By choosing a mass to charge ratio and making a measurement of the signal obtained, one can immediately find out the number of those molecules present in the ionizer region of the RGA. By sweeping through a whole range of M/e ratios, one can find a whole range of molecules that are present and begin to understand the full range of chemical components in the gas.
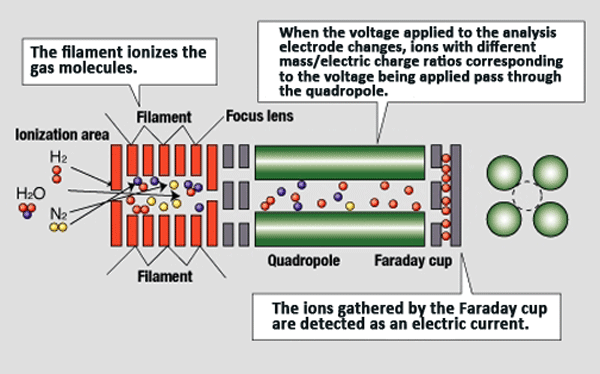
The actual analyzer is located in the vacuum and consists of the following principal components:
- An ion source that ionizes neutral gas particles, which are then sorted in the mass filter on the basis of their mass-to-charge ratio (m/e ratio)
- The ion current is measured using a Faraday detector or a secondary electron multiplier (SEM) after the ions have left the separating system. The measured current is a parameter of the partial pressure of the respective gas molecules or a parameter of fractals that may possibly have been generated in the ion source
- A data analysis system processes the ion currents measured with the aid of the detector and presents these currents in various forms. Today, data analysis software programs are capable of supporting the user in interpreting mass spectra.
Maintenance & Repair
Despite our best efforts, it may occur that the RGA is in need or repair. The harsh environment of heat-treating coupled with inadvertent exposure to atmosphere, pump oils, or other contaminants is a fact of life. Filament replacement, ion source cleaning, and filter cleaning are examples of what can be done. However, disassembly of certain components, such as the mass filter assembly will result in costly and time-consuming factory repairs. Remember, an RGA is a delicate instrument!
In Summary
Residual Gas Analyzers can be a very effective tool to analyze system gas loads resulting from real leaks, virtual leaks or chamber wall outgassing. RGAs have a number of advantages over traditional, dedicated gas leak detectors including the ability to differentiate between different gas species, comparable sensitivity levels, the ability to detect internal or “virtual” leaks and to detect and analyze outgassing problems.
References
2. CPM Compact Process Monitor, Inficon Product Bulletins & Training Information (www.inficon.com).
3. MKS Instruments (www.mks.com).
4. Horiba Semiconductor (www.horiba.com).
5. Pfeiffer Vacuum (www.pfeiffer-vacuum.com).