BY JEFF PRITCHARD
All furnace equipment used for heat treating should be properly instrumented and periodically tested for uniformity. The temperature uniformity within the furnace must be regularly surveyed. The frequency of surveying is largely dependent on the type of equipment in use and its previous history in accuracy and reliability. Exact survey frequencies should be determined from applicable processing specifications. However, quarterly temperature uniformity surveys are fairly standard.
The purpose of the uniformity survey is to determine the range of temperatures present at different locations in the furnace under normal operating conditions. A furnace is normally qualified through an initial comprehensive survey. This involves determining temperature variations by surveying at the maximum and minimum operating temperatures and at a series of intermediate temperatures not more than 167ºC (300ºF) apart. After initial qualification, periodic surveys can be taken, usually on a quarterly basis. Unless otherwise specified, periodic surveys can be performed at a single temperature that rotates between the minimum, mid-range and maximum operating temperatures of the furnace. Uniformity surveys are also performed after any major repair to the furnace or when the operating integrity of the equipment may be in question.
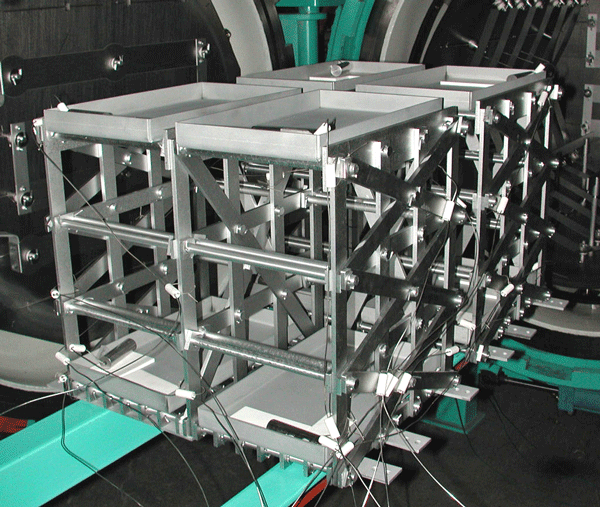
When surveying vacuum furnaces, the furnace must be evacuated to the minimum pressure used during processing. To conduct the survey, the furnace is heated to the required set-point. When the highest reading survey thermocouple reaches the low end of the allowable tolerance from the set-point, a complete set of readings is taken every two minutes until a recurrent temperature pattern is observed. Thereafter, the temperatures of all survey thermocouples are read at five-minute intervals for thirty minutes minimum.
Results should be recorded manually on a special form by the inspector performing the survey. Charts from the recording potentiometer should also be maintained to confirm the manual recordings. When performing a survey, the temperature of the furnace control and overtemperature thermocouples must also be read and recorded at intervals of ten minutes or less. These readings are then compared to the readings of adjacent survey thermocouples. The ability of the furnace thermocouples to represent and control the temperature uniformity can then be determined for each set-point surveyed. For all air-circulating and vacuum furnaces, the survey is performed by locating thermocouples at various locations within the usable working zone of the furnace.
The exact location of the survey thermocouples varies somewhat between specifications. Normally, at least nine thermocouples will be located at points covering the outer extremes and the center of the working zone. To reflect the normal operating characteristics of the furnace, an average or simulated production charge is sometimes loaded into the furnace for the survey. Survey thermocouples must be properly calibrated prior to use. In addition, an instrument calibration should be completed prior to the temperature uniformity survey. Readings from all survey thermocouples are recorded on an automatic multi-point recording potentiometer.
The recording potentiometer should be calibrated monthly and traceable to recognized primary standards. Compensations are made for known deviations. The allowable operating tolerances can vary according to the applicable specification, equipment type, heat treating temperature and the material being processed. In general, at temperatures below 650ºC (1200ºF) furnace temperature uniformity should be within ± 8ºC (± 15ºF) maximum. For temperatures of 815ºC (1500ºF) or higher, uniformity should not exceed ± 14ºC (± 25ºF).
VAC AERO furnaces are designed to meet the temperature uniformity requirements of the most stringent processing specifications. VAC AERO also offers temperature uniformity and instrument calibrations services. Contact us for more details.
For more information on VAC AERO’s Furnace Manufacturing Division please click here.