Lubricants in vacuum applications include wet and dry lubricant types (Table 1), greases and oils. So-called “wet” lubricants tend to stay wet on the surface to which they are applied, while dry lubricants go on wet but dry as they are applied. In general solid particulates do not stick to dry lubricants but they do not tend to last as long as wet lubricants and as such need to be reapplied. By contrast, greases adhere better than oils and tend to last longer. Oil is preferred where the lubricant needs to be circulated.
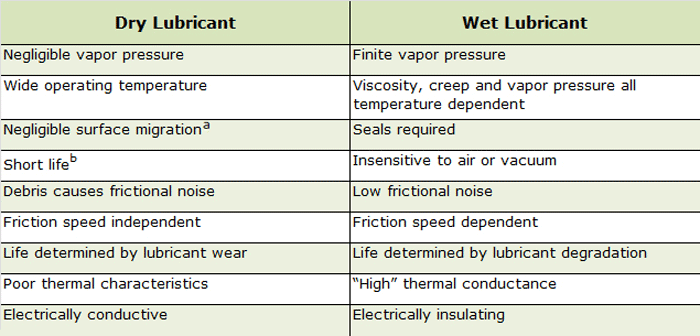
Notes:
[a] Debris can float free.
[b] In air. Depends on type and matrix.
The major disadvantage of conventional liquid lubricants is that they have relatively high vapor pressures (= 1.3 x 10-4 Pa at room temperature) and surface diffusion coefficients (= 1 x 10-8 cm2/s) with low surface tensions (in the order of 18 – 30 dyne/cm) and can volatilize or creep away from areas of mechanical contact resulting in high friction, wear or mechanical seizure. In addition, their volatility can cause issue with achieving proper vacuum levels and/or depositing on component part surfaces. The presence of other gaseous species in a vacuum environment (e.g., water vapor, oxygen, carbonaceous gases) can cause the force of adhesion between metal surfaces joined by liquid lubricants to be so strong that the joined areas can only be separated by fracture.
The major disadvantage of solid lubricants is a (relatively) short life (in relation to liquids or greases). Once a solid lubricant is no longer in the contact zone, failure can be abrupt (compared to wet lubricants) without prior signs of degradation.
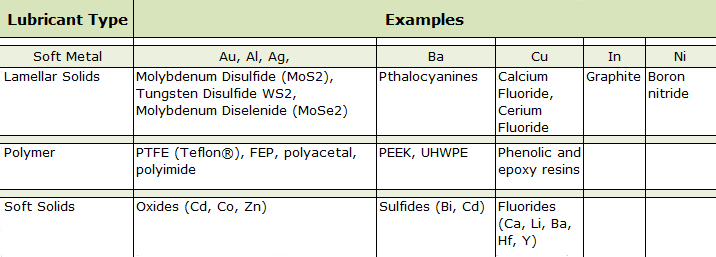
Notes:
[a] FEP is an acronym for fluorinated ethylene propylene.
[b] PEEK is an acronym for polyether ether ketone.
[c] UHWPE is an acronym for ultra high molecular weight polyethylene.
There are four basic types of solid or dry lubricants available for vacuum applications: soft metals (e.g. indium, lead, gold, aluminum, silver, copper, nickel), lamellar solids, polymers or low shear strength soft solids (Table 2).
In simplest terms, dry film lubricants are solids that are intended to provide low frictional resistance between surfaces (due to their layered lamella structures) and can be applied directly to the surface by rubbing. For most vacuum applications, crystalline materials, such as molybdenum disulfide, tungsten disulfide and graphite, are common as stand-alone lubricants. These materials can be used independently or in combination with other lubricants or soft metals to achieve the desired results. We will discuss a few of the more common here.
Graphite
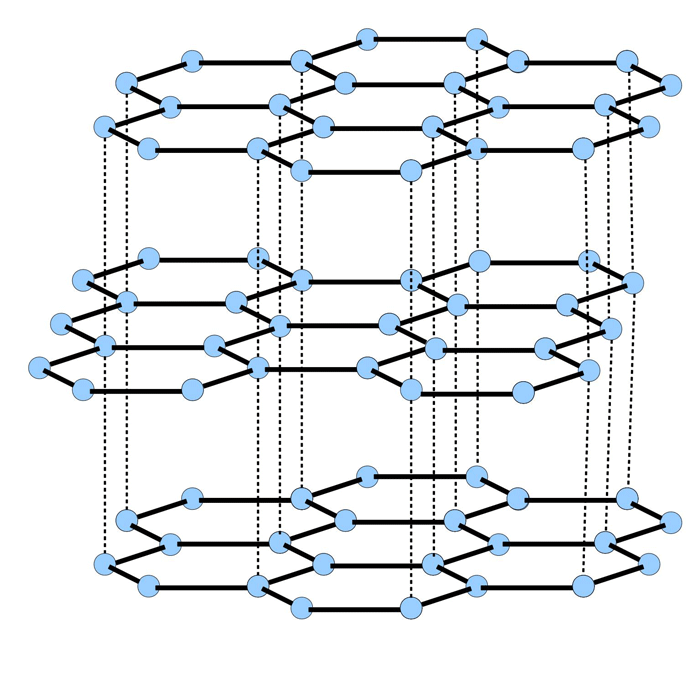
Graphite is one of the oldest and most common types of dry lubricants. It is a soft, crystalline form of carbon and is gray to black in color. Its metallic properties include good thermal and electrical conductivity, while its nonmetallic properties include chemical inertness, high thermal resistance and lubricity.
Graphite is a layer lattice lamella crystal structure (Fig. 1), which allows the surfaces to slide easily relative to one another. The bonds between the carbon atoms in the crystal structure of the layer are stronger than the carbon bonds between layers. Graphite is comprised of carbon and water vapor. Each carbon atom is bonded to three other surrounding carbon atoms. The flat rings of carbon atoms are bonded into a hexagonal structure.
Graphite is considered to have excellent lubricating properties where moisture (water vapor) is available since its shear strength is dependent on absorbed gases and at low (vacuum) levels, these gases desorb and the coefficient of friction dramatically rises. Graphite will function as a lubricant up to approximately 790°C, and as a release and anti-seize up to about 1315°C. The oxidation product is carbon dioxide. Due to the requirement for entrained moisture vapor, graphite does not function well as a lubricant in hard (10-4 Torr and lower) vacuum levels.
Molybdenum Disulfide
Molybdenum disulfide, MoS2, is a blue-gray, crystalline inorganic powder, which is used in many vacuum applications as a dry lubricant. It can also be used as a high temperature protective coating having a melting point of around 2000ºC and a density of 5.31 g/cc. In addition, molybdenum disulfide is an additive in greases, dispersions, friction materials and bonded coatings. Molybdenum-sulfur complexes may be used in suspension but are more commonly dissolved in lubricating oils at concentrations of a few percent.
Molybdenum disulfide is the most common natural form of molybdenum, is extracted from the ore and then purified for direct use in lubrication since it has the durability to withstand heat and pressure. This is particularly so if small amounts of sulfur are available to react with iron and provide a sulfide layer, which is compatible with MoS2 in maintaining the lubricating film.
- A number of unique properties distinguish molybdenum disulfide from other solid lubricants. These include:
- A low coefficient of friction (0.03-0.06) which, unlike graphite, is inherent and not a result of absorbed films or gases;
- A strong affinity for metallic surfaces;
- Film forming structure;
- A yield strength as high as 3450 MPa (500 x 103 psi);
- Stability in the presence of most solvents;
- Effective lubricating properties from cryogenic temperatures to about 350oC in air (1200oC in inert or vacuum conditions);
- Molybdenum disulfide will perform as a lubricant in vacuum where graphite fails.
Molybdenum disulfide can have a variety of formulations (Table 3).
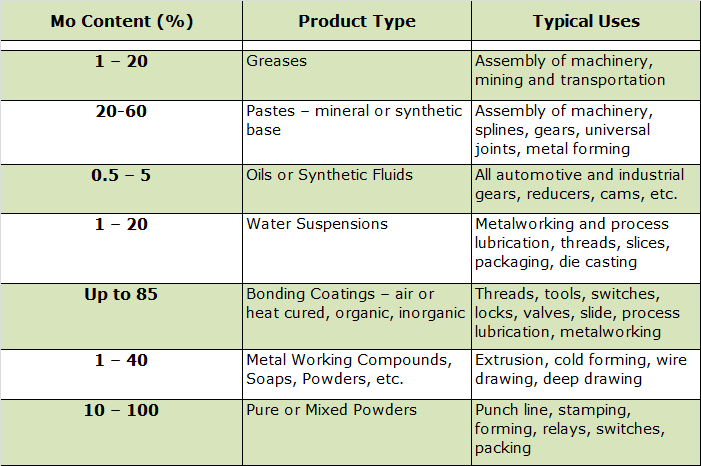
Molybdenum disulfide is very sensitive to water vapor and if stored in a humid environment will oxidize readily (forming MoO3) destroying its lubricity characteristics.
The ability of molybdenum disulfide to function as a lubricant is intimately related to its layer structure (Fig. 2).
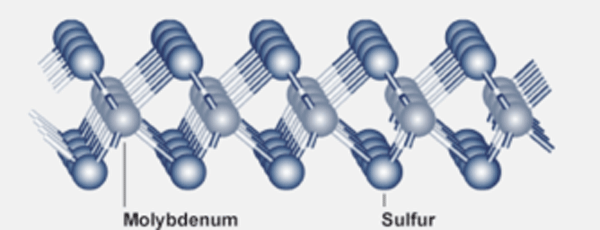
A layer of molybdenum atoms is sandwiched between two layers of sulfur atoms. When molybdenum disulfide is dispersed between two metal surfaces, a layer binds to each metal surface through the sulfur atoms. Then the surface irregularities on the metals are prevented from coming into contact. Sliding contact is between the outer layers of sulfur atoms, which are only weakly interacting. As with graphite, the surfaces are therefore able to slide easily relative to one another.
A combination of molybdate and water-soluble sulfides can provide both lubrication and corrosion inhibition in cutting fluids and metal forming materials. Oil soluble molybdenum-sulfur compounds, such as thiophosphates and thiocarbamates, provide engine protection against wear, oxidation and corrosion. Several commercial manufacturers supply these additives to the lubrication industry.
A dry film coating of molybdenum disulfide is helpful on bolts used with vacuum (so-called CF) flanges to avoid breakage issues as the seal force requirements can be such that high torque is required.
Molybdenum disulfide has recently attracted a lot of interest for semiconductor device applications and has potential use for high-temperature electronics.
Tungsten Disulfide
Tungsten disulfide (WS2) is often considered as an alternative to molybdenum disulfide given its lubricous characteristics. It has a coefficient of friction of 0.03 and offers excellent dry lubricity under conditions of load, vacuum and temperature. It can also be used in high temperature and high-pressure applications.
Tungsten disulfide (Table 4) offers temperature resistance from 188ºC to 1316ºC in vacuum. The load bearing property of coated film is extremely high at 400,000 psi and a coefficient of friction of 0.044 at 20,000 psi and 0.024 between 200,000 to 400,000 psi.
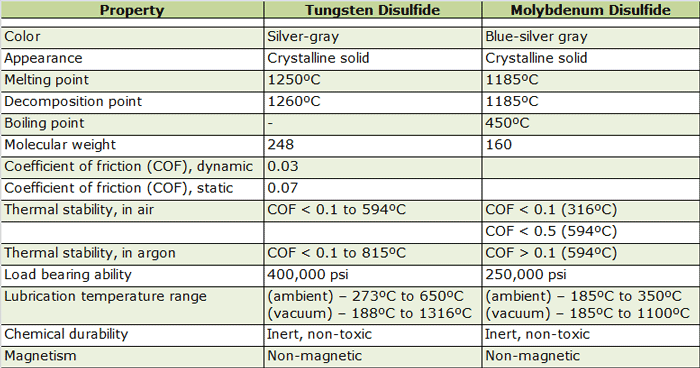
Tungsten disulfide can be used in almost all applications where molybdenum disulfide or graphite are currently employed and is used extensively by NASA, military, aerospace and automotive industries.
In Conclusion
The choice of lubricant in vacuum applications is highly dependent on system requirements. Experience is often the best teacher but knowing the basic characteristics of the lubricant systems can help influence the selection process.
References
1. Hilton, M. R. and P. D. Fleischauer, “Lubricants for High-Vacuum Applications”, Space and Missile Systems Center, Air Force Material Command, Engineering and Technology Group, 1993.
2. “Solid Film Lubricants: A Practical Guide”, Machinery Lubrication,
3. Encyclopedia of Tribology Volume, C Kajdas, W. Wilusz and S. Harvey (Eds.), Elsevier Science Publishers, 1960.
4. International Molybdenum Association (www.imoa.info)
5. Laboratoire de Physique et Modélisation des Milleux Codensés UMR 5493 (www.lpmmc.grenoble.cnrs.fr).