Tungsten is used in vacuum furnaces (Fig. 1) when there is a need for structural integrity at elevated temperature and/or in situations where other materials may degrade, such as when lower melting point eutectics are a concern. One example of its use is in roller rail assemblies in which graphite wheels are positioned between molybdenum rails using tungsten axles (Fig. 2).
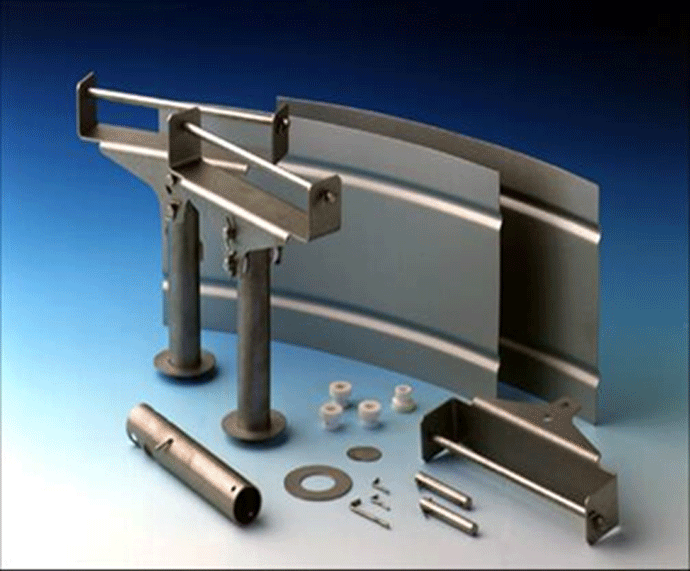
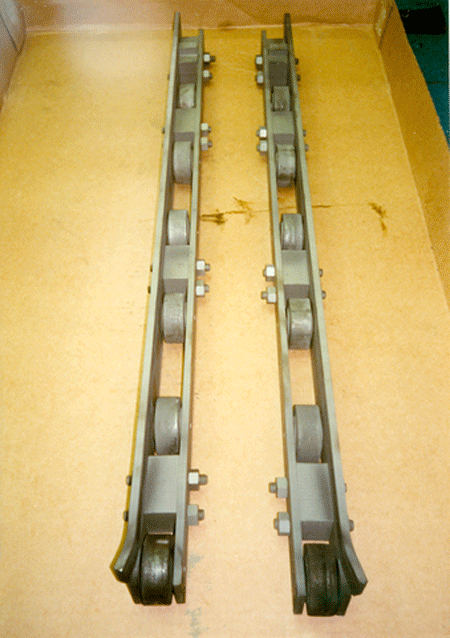
Tungsten Applications in Vacuum Furnaces
Tungsten (chemical symbol W) is a member of the family of refractory metal (Mo, Nb, Re, Ta, W) and has the highest melting point and vapor pressure of this group. Due to this unique property, it is commonly used as a material of construction in specific areas of vacuum furnace hot zones operating above 1315ºC (2400ºF).
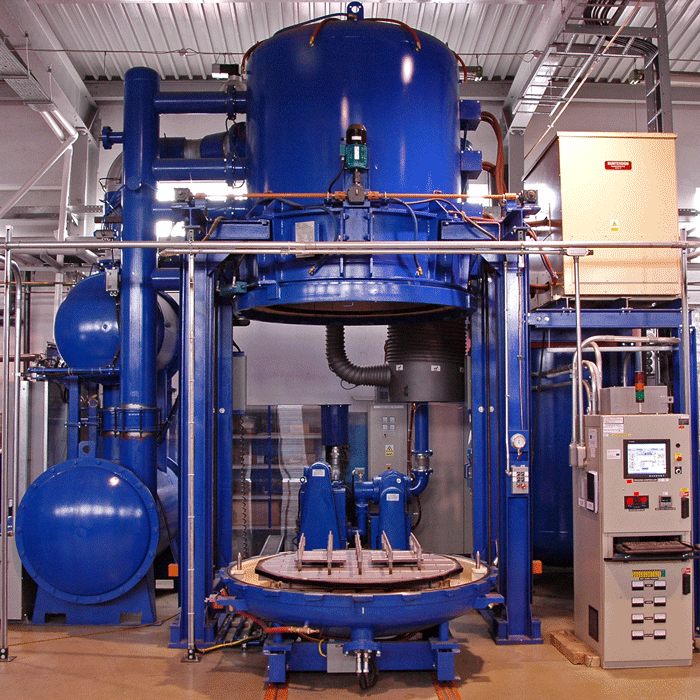
Radiation shields (Table 1) for these high-temperature furnaces are often manufactured from tungsten (or tantalum) where a maximum operating temperature of 2400°C (4350°F) can be achieved.
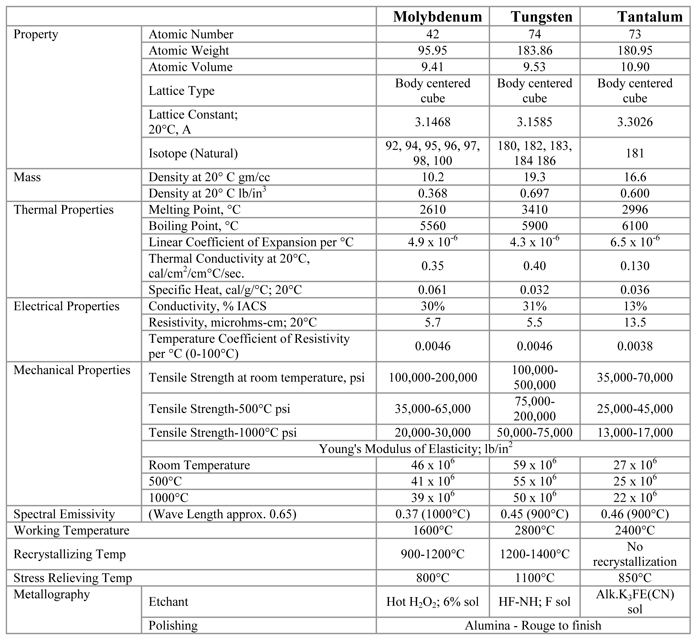
Tungsten can also be used for heating elements given that it has the highest duty temperature, typically 2800°C (5075°F). In practice, this rating is often downgraded (Table 2) as it is for all heating element material choices. Tungsten will become brittle, however, if exposed to oxygen or water vapor and is sensitive to changes in emissivity. In general, tungsten is resistant to corrosion below 60% relative humidity.
Depending on the design of the hot zone (cylindrical or rectangular), heating elements can be placed circumferentially in a 360° pattern, on just the two (2) sidewalls, on the top and bottom as well as the sidewalls or with the use of end elements, on all six (6) sides
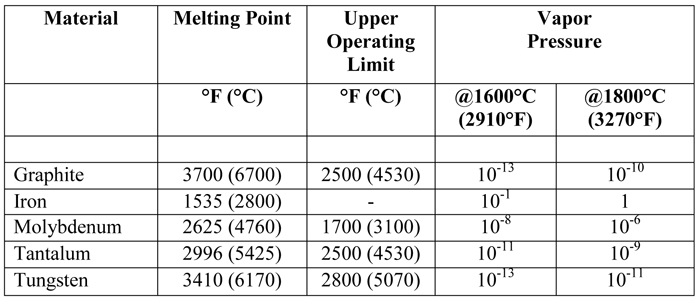
The use of tungsten in hot zone construction for vacuum furnaces is due to the wide range of properties that it exhibits, namely:
- High melting point, 3420ºC (6187ºF)
- Low vapor pressure
- High hot strength
- Low thermal expansion
- High thermal conductivity
- High Young’s modulus
- High corrosion resistance against acids and molten metals
- Recrystallization temperature, between 1100º – 1400ºC (2012º – 2550ºF)
- Good electrical conductivity
- High modulus of elasticity
Tungsten and its alloys are produced primarily using powder metallurgy methods. Powder metallurgy is preferred over other manufacturing methods since it results in extremely fine grain size. This simplifies further processing and conveys better mechanical properties to the final product.
Tungsten powder is pressed into various shapes and dimensions and then sintered at temperatures between 2000 – 2500ºC (3630 – 4530ºF) in furnaces utilizing hydrogen, thereby increasing the density and strength of the finished product.
Tungsten is not only well-suited for use in vacuum furnaces operating at temperatures above 1300ºC (2375ºF) but is also used in a number of other industries such as:
- Lighting (e.g. incandescent light bulbs)
- Electrical (e.g. electrical contacts)
- Medical (e.g. X-ray radiation shielding)
- Construction (e.g. boring bars)
Characteristics of Various Grades
Tungsten is available in several alloy combinations (Table 3). The choice between the different tungsten grades often depends on the operating temperature and product design (Table 4).
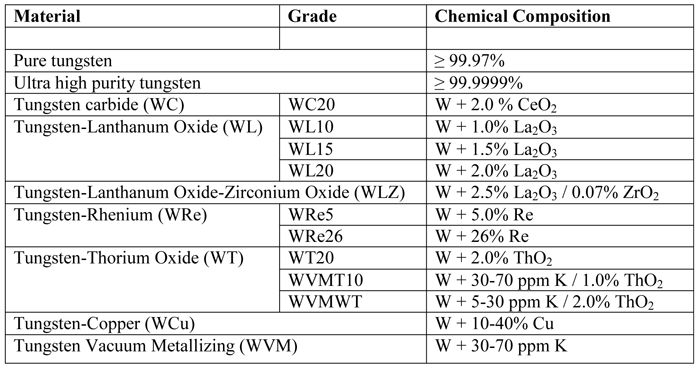
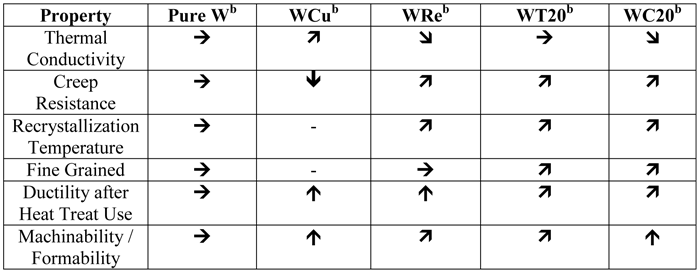
Notes:
[a] Room temperature
[b] Arrows have the following designations
Ú Comparable to pure tungsten
Þ Greater than pure tungsten
à Less thank pure tungsten
Û Significantly greater than pure tungsten
Mechanical properties of tungsten are influenced by purity, type, and composition of any alloying elements, heat treatment (annealed condition) and by microstructure. Tungsten has a body-centered cubic (BCC) lattice structure and exhibits very low ductility at room temperature. Metalworking and alloying can reduce the ductile-to-brittle transition temperature. Increasing the strength of tungsten can be achieved by increasing the degree of deformation, also, unlike other metals, working will also increase its ductility. The mechanical properties, especially creep strength, can be improved significantly by the addition of cerium or lanthanum.
Material Limitations
For applications involving high temperatures, such as hot zone construction in vacuum furnaces, knowledge of the recrystallization temperature and the various gas species present (Table 5) is important. Certain properties, such as ductility and fracture toughness decrease with increased levels of recrystallization.
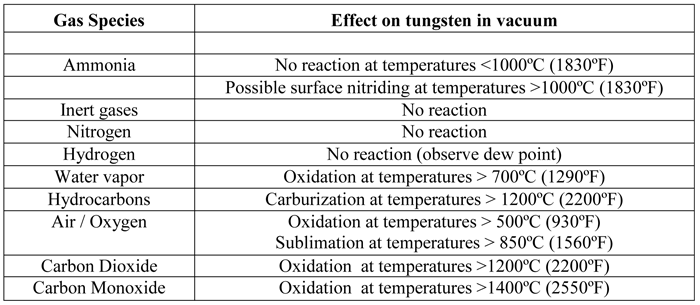
The degree of deformation and the chemical composition are the two factors, which determine the recrystallization temperature. This temperature can be increased significantly by the addition of small, finely dispersed oxide particles or by adding aluminum potassium silicate.
Above the point of recrystallization, the structural transformation begins, leading to grain growth. This alters mechanical properties typically reducing strength and hardness. Grain growth can only be reduced by reprocessing (e.g., rolling, forging or drawing) the material and because of this, a high recrystallization temperature is always desired.
Summary
Tungsten and tungsten alloys, while not as commonly used as molybdenum, find their niche in applications where demands for performance must be achieved at high temperature and in those situations where other materials may form unwanted eutectics, such as molybdenum and carbon at 2200ºC (3990ºF). The selection of the proper tungsten alloy is highly dependent on the component parts being run, equipment construction, operating temperature(s) and conditions to which the product will be used.
References
1. “Tungsten Material Properties and Applications”, Plansee Technical Brochure
2. Herring, Daniel H., Vacuum Heat Treatment, BNP Media, 2012.
3. http://www.plansee.com/en/Materials-Tungsten-403.htm