The correct use of the Gas Ballast valve on a mechanical oil-sealed rotary vacuum pump has always been seen as “black science” or just plain guesswork. It is a very simple device and when used correctly can keep a vacuum pump working well even though it may be used on a very wet process and the oil becomes contaminated with condensed vapors.
One series of vacuum pumps I worked with had a gas ballast valve that had no stop when opened. If you unscrewed it enough the ballast knob would come off in your hand allowing maximum air to enter the pump, the pump to become noisier and a blast of oil mist to come out of the exhaust. I always thought that if a lab technician ever did that they would replace the knob and never ever touch the gas ballast valve again.
Vacuum pump specifications will tell you how much water vapor can be handled by the pump using the gas ballast valve. It is usually shown in ounces or grams of water per hour. If the process generates water vapor above the pump capability the use of a condenser should be considered.
Oil in Vacuum Pumps
Oil sealed rotary vane or piston vacuum pumps rely on the oil to do several jobs:
- Seal the interior pumping mechanism and prevent leakage from the high-pressure side (exhaust) to the low-pressure side (inlet)
- Lubricate all rotating and sliding surfaces where metal to metal contact is made (many vacuum pump vanes are some type of polymer these days).
- Take the heat away from the areas where it is generated and deliver it to the oil reservoir where some of the heat can dissipate, and
- Have a low enough vapor pressure that the required low pressure (vacuum) can be generated; and.
- Reduce the noise level of the pump to some extent.
If the oil becomes contaminated with water, condensed water vapor from the vacuum chamber, it loses its ability to lubricate, seal and cool the pump and will also lose its ability to reach the low pressure required for the process. If the pump is run with contaminated oil it may also overheat to the point that the pump will seize up and it may then require a costly rebuild.
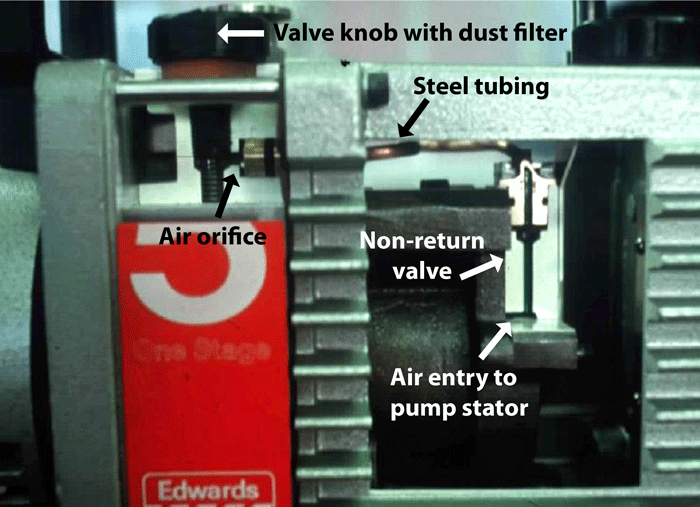
Where does the Water Vapor come from?
When any large vacuum chamber is opened to atmosphere to unload and reload, water vapor from the air will form monolayers of water molecules on every square inch of surface area inside the chamber. When the chamber goes back under vacuum that water vapor will desorb and end up in the vacuum pump.
In vacuum furnaces, chamber components such as the insulation can be porous and absorb lots of water vapor. When water vapor molecules are absorbed onto surfaces inside the small pores of fire brick, for example, it takes extended time under vacuum for these water molecules to release off the surface and be pumped away. Fortunately in the vacuum furnace industry, applying some heat will speed up the desorbing process.
Where is the Gas Ballast Valve installed?
The exterior part of the gas ballast accessory will be a rotating knob, tap or valve mounted somewhere on the top, sides or end of the pump. Usually it is a hand operated valve that is unscrewed two or three turns to allow air into the pump when needed. One manufacturer has a three position gas ballast valve – closed, medium flow and full flow.
On the inside of the pump mechanism, leading from the exterior gas ballast valve, there is a passageway to allow a small flow of air to enter the compression side of the pump close to the exhaust valve location. The hole into the compression volume must be situated in a position where that volume of gas has been isolated from the pump inlet volume. The passageway may be a hole drilled through the pump casting, a metal tube or a combination of both (Fig. 1).
All gas ballast valves will also incorporate a non-return check valve (Fig. 2) somewhere between the exterior valve and the hole into the stator volume. Air needs to enter the pump, but we do not want exhaust gas and vapor mixtures to exhaust through the gas ballast valve. At the point in the cycle where the pressure reaches above atmospheric pressure to open the exhaust valves, the gas ballast line non-return valve (or check valve) will close.
The hand operated valve can be removed and replaced by a solenoid-operated valve connected into the process control system to control it automatically. There may be parts of the vacuum process cycle when the valve should be open and other parts when it should be closed. This is also useful if the process has hazardous gases. Because air contains oxygen (O2) and water vapor (H2O) it could create additional reactions in a hazardous process, so nitrogen is used because it is inert.
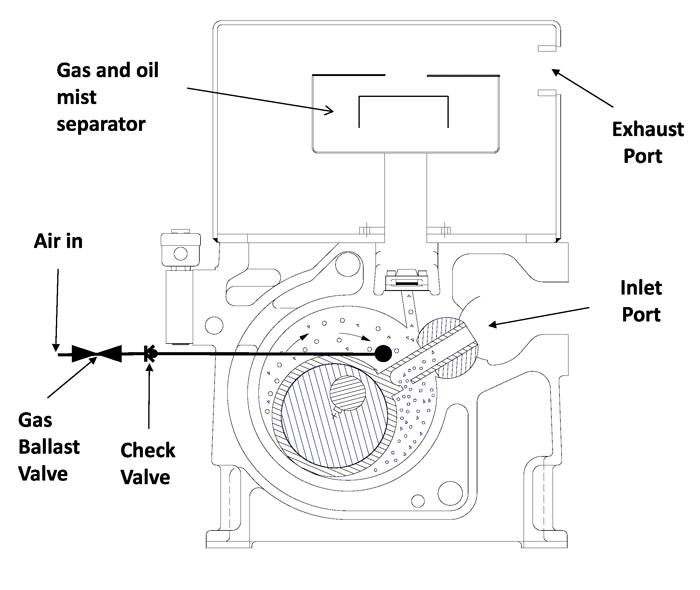
What Happens When the Gas Ballast Valve Is Open?
This is the same for the rotary vane and rotary piston pump. The gas ballast is utilized when medium or large amounts of water or other condensable vapors are in the system.
Opening the gas ballast valve will prevent the vacuum pump from reaching its ultimate vacuum, so if a low pressure is needed towards the end of the cycle, the gas ballast valve can be closed once the water vapor has been pumped away.
At ambient temperature, once the pressure in the vacuum chamber is below about 30 Torr, water vapor will start to desorb from its surface. The vapor pressure of water is about 18 Torr at room temperature so below that pressure will be when the maximum amount of water vapor evolves. That mixture of gas and water vapor will flow to the vacuum pump and enter the low vacuum inlet side. The pump mechanism then sweeps the gas and water vapor mixture to the high-pressure exhaust side of the pump.
The mechanism starts to reduce the volume of dry gases and wet vapor and increase its pressure on the exhaust side of the pump. Each constituent of the gas and water vapor mixture has its own partial pressure to make up the total pressure of the whole volume, at any part of the cycle. With the gas ballast valve open, as soon as the pump vane passes the gas ballast hole, air will enter through the valve and quickly raise the pressure to atmospheric pressure.
Because the air entering is mostly nitrogen and oxygen, the ratio of the water vapor component to the total pressure will be reduced by a large amount and because the exhaust valve will now almost instantly open, the water vapor will not reach its vapor pressure and condense. Instead, it remains as vapor and is exhausted in the gas stream, out into the oil box and to exhaust.
As the gas is compressed to above atmospheric pressure to actuate the exhaust valves and leave the pump, it will also tend to flow back up the gas ballast line. However, the non-return valve will close and not allow that to happen. It is usually a simple spring loaded check valve that opens as gas flows in but closes if gas wants to flow outwards.
Cleaning Oil Contaminated with Water
If the oil is contaminated with water droplets, gas ballasting the pump will clean up the oil. This may take an hour or two, or several hours depending on the amount of contamination. When the gas ballast valve is open the additional air going through the vacuum pump will create more oil mist at the exhaust. That oil can be separated in an oil mist filter and reused if clean. Depending on the size of the pump and the amount of oil in it, gas ballasting could cause the pump to run low on oil. This should be taken into consideration before leaving a vacuum pump gas ballasting overnight.
If the pump oil is contaminated with water droplets they will be spread throughout the oil. The oil is continually being moved around the pump mechanism and all surfaces are wet with oil. When the contaminated oil reaches the inlet side of the vacuum pump where the pressure is low, water droplets in the oil will evaporate to vapor. That vapor is then swept towards the exhaust side of the pump where the vapor will be exhausted as vapor if the gas ballast valve is open. As time passes the water will slowly be evaporated out of the oil until it is clean again. If the oil becomes very contaminated it may turn to a white and green emulsion. At that point the only remedy is to drain, flush and refill the pump with new oil.
The gas ballast device is very simple and when used correctly will increase the life of the vacuum pump oil when lots of water vapor is present in a system.
Copyright Howard Tring, Tring Enterprises LLC Vacuum & Low-Pressure Consulting.