Background
Since oil sealed mechanical vacuum pumps started to be commercially available in the 1920s there have been many companies making this type of pump. The oil flooded rotary piston vacuum pump runs at a slow rotational speed and is a heavy duty design. It has been manufactured for about 85 years. In the early 1900s, these pumps were relatively small at up to 40 cfm capacity. By the late 20s and early 30s, the industrial revolution was gaining steam and the manufacturers designed larger capacity pumps to suit new applications. By the 1940s oil-sealed rotary piston vacuum pumps were offered in capacities up to 700 cfm. They are known for their ability to keep on running despite ingesting all sorts of contaminants.
Kinney claims to have introduced the world’s first rotary pump in 1904, two years after the company was founded. The Kinney document I have just says rotary pump but I presume it was a rotary vane design as other documents say the rotary piston pump design was introduced in about 1909. In 1926 their popular model was the VSD-8811, later to be the KS-47. Current large models are called the ”KT” series. (See figure 1.)
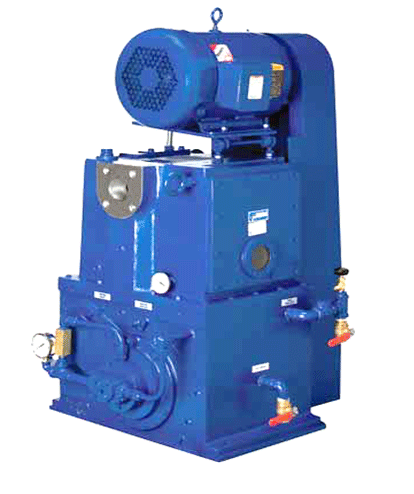
It wasn’t until 1936 that F. J. Stokes Machine Co. introduced its version of the rotary piston pump, which was to have the well-known “Microvac” trade name. Mr. Stokes started his business in 1895 and over the years built many different types of machinery. (See figure 2.)
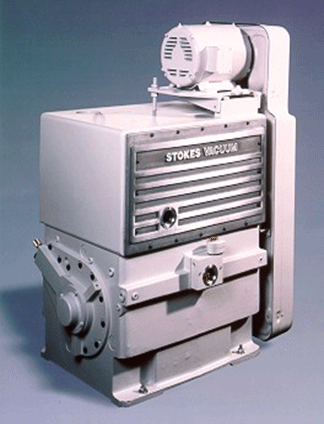
These two manufacturers of vacuum pumps for industrial and scientific applications had tremendous growth through the years into the70s and 80s when vacuum pump technology started to change.
I have found a little bit of history of the Kinney Company but they started in the Boston area, eventually became part of Tuthill Vacuum and Blower Systems and moved to Springfield, Missouri. When I was working at Stokes there was a plan of the Stokes Vacuum Tabor Road facility posted in the lobby. It indicated many expansions over the years from the 30s to the 80s. The Stokes Vacuum Company made tablet presses and injection molding machines in addition to the various vacuum related systems such as vacuum coaters, vacuum freeze dryers, vacuum dryers and probably vacuum furnaces.
Applications
The rotary piston vacuum pump has become the major workhorse for a number of vacuum applications where relatively large chamber volumes have to be evacuated, where there is a large volume of outgassing from chamber walls or the process product or when the process has a high gas throughput due to gas being fed into the process chamber. They are excellent if the process requires a vacuum range between a few mm Hg (also called torr after Mr. Torricelli) down to about 50 microns. The pumps are generally rated to give an ultimate vacuum of 10 microns. (1 micron = 1/1000th of 1 mm Hg) Remember that the vacuum level in the process chamber will always be higher than the ultimate or blank-off vacuum at the pump inlet.
Prior to the 1980s, when “dry” vacuum pumps started to enter the market, the rotary piston pump was a popular option when there was a large industrial or scientific process chamber to be evacuated. They were not used much in the chemical process industry, as the vacuum levels needed there were not as high and large volumes of gas and vapor could be handled better by steam ejectors combined with liquid ring type vacuum pumps. (A “dry” vacuum pump has no lubricant in the pumping volume, but still requires lubrication for gears and bearings.) Oil sealed rotary vane pumps, originally vee-belt driven and later mostly direct drive, were used but were not particularly suited to dirty applications, especially the faster running direct drive designs. In some applications with either a very harsh process or where the process requires a “cleaner” pump with less chance of contamination by oil vapor the newer designs of dry vacuum pumps have been used successfully.
In the heat treating and vacuum furnace industry rotary piston vacuum pumps are still an economical choice for many applications. The basic pumping capacity is often 150 cfm or 300 cfm and either size can be combined with a Roots design blower on the inlet side to give a variety of higher pumping speeds (and higher vacuum) depending on the pumping speed of the Roots blower. Also, the pumps are relatively easy to maintain or service by either in-house maintenance crews, local third-party service shops or by the pump manufacturer depending on the ability or choice of the user. A number of vacuum pump industry companies have the ability to manufacture and sell the basic piston, piston sleeve and hinge bars for this type of pump.
The main differences between Kinney & Stokes
The Kinney rotary piston pump is called a triplex design. It achieves a balanced rotation by having one large piston in the middle and a small opposed piston at each end. (See figure 3.) The pumps are vee-belt driven by an electric motor and in the smaller sizes, the pump and the motor are mounted on a steel baseplate. Larger sizes, such as the “KT” series have the electric motor mounted on the top of the pump to save floor space. The oil circuit in the Kinney design is pressurized, the oil being circulated by a small pump driven by the main pump shaft. Modern Kinney pumps have sealed bearings, but I have no information on how long they have been used. The hinge bars in the Kinney design are “caged”, they are held together by two end plates as an assembly.
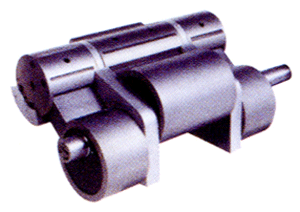
The Stokes rotary piston pump is called a simplex design as it only has one large piston. Balance in this design is achieved by using a weighted pulley on the drive side and a weighted flywheel on the other side. (See figure 4.) The Stokes design obviously has fewer parts mounted on the shaft than the Kinney. The oil circuit in the Stokes Microvac pump is gravity fed. The oil in the main reservoir above the pump drains down and across to each end of the pump where it feeds through the bearings first. It then finds its way into the stator volume where it seals the gap between the piston sleeve and the stator and also lubricates the hinge bar area. The oil is eventually ejected as droplets or mist in the gas stream through the exhaust valves. The Stokes Microvac hinge bars are separate parts and free to float.
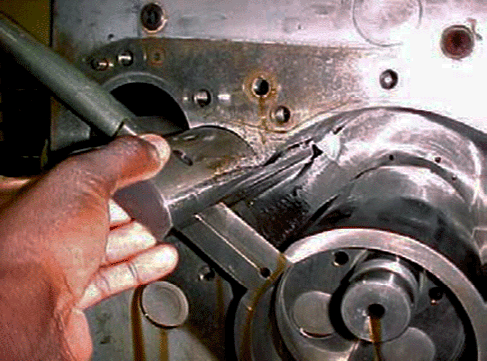
Both makes of pump use a large volume of vacuum pump oil to lubricate and seal the pump interior. Whereas the rotary vane pump has vanes that press onto the stator surface while they rotate and have just a film of oil to lubricate and seal the pump interior, the rotary piston pump is different.
The piston sleeve mounted on the rotary piston does not touch the stator. There is a gap of perhaps 5 to 10 thousandths of an inch. (I’m sure someone can confirm the gap dimensions). It is the design of this gap in the vacuum pump that makes it ideal to operate in dirty applications where lots of dirt and dust are present. The contaminants are held in the oil but are not ground between the piston sleeve and stator surfaces due to the relatively large gap. The one area that is likely to see some wear due to gritty contaminants is in the lower hinge bar area at the pump inlet.
The clearance between the ends of the piston sleeve and piston, where they rotate against the side plates is smaller, to allow the oil film to lubricate as needed and to reduce gas leakage.
Both pumps have large oil separators mounted above the pump stator. The oil separator changes the direction of the gas stream exhausting through the outlet valves. When the gas stream changes direction, most of the oil droplets or mist come in contact with the plates of the separator and stick to them. Once the oil accumulates on the plates it will drain back down into the oil reservoir. These days, due to environmental rules, most installations will also install an oil mist filter to catch the fine oil mist which remains in the gas stream.
There are certainly other minor differences between the two designs, but the ones mentioned are the most striking when reading the pump literature.
Why it remains a popular design
This design of vacuum pump, whether triplex or simplex, has been in the North American marketplace for many years. The performance and longevity are well known and spare parts are readily available. For many relatively clean applications, it is an economical pump and easy to service on-site without having to move it. In dirty applications, the time between oil changes can be extended by using an external oil filtration system. Filter elements can be selected to suit the specific contaminants.
Other options, such as multi-stage or rotary screw dry pump designs run at much higher speeds, usually around 3600 rpm. This may affect bearing life, especially those designs that have overhung rotors. They can be a good option if the process gives off condensable vapors (such as wax) because the pump temperature can be controlled to pass the vapor through the pump and then trap it. In dirty and dusty applications the contaminant can be blown through the dry pump mechanism using an inert gas purge and then trapped. However, most manufacturers do not offer service training on this newer technology – preferring to take the service calls themselves or having you return the pump to their facility for repair. Lastly, there is a premium price to pay, although one company does say their pump will run for 5 years before it needs to be serviced, and for OEMs, it adds to the price of the package being quoted, unless the customer specifies a certain vacuum pump product.
Stokes, Kinney and other similar vacuum pumps
In my years of experience working with the rotary piston type of vacuum pump, I do not know who has the most pumps in the marketplace, Stokes or Kinney. David Webb notes, in his article “History of Mechanical Vacuum Pumps in the USA”, that in the 1960s Stokes overtook Kinney in a number of pumps sold due to their success in the heat treating industry.
Certainly, the number of pumps being manufactured has a direct relationship to the manufacturing cost of each pump. That is why vacuum pump companies are bought by other companies to make the most efficient use of costly machine tools and purchasing power.
As I said above, Kinney became part of Tuthill Vacuum and Blower Systems business some years ago.
Stokes was owned at one time by Pennwalt, and then by Smith’s Industries prior to being bought by the old BOC Edwards which is now Edwards Vacuum Inc. As both the Kinney and Stokes names are well known in the vacuum pump industry, both trade names continue to be used by the respective owners. Perhaps due to lax security on engineering drawings and certainly due to the ability of talented employees to reverse engineer anything from valve springs to complete pumps, there are “clones” of both Stokes and Kinney in the marketplace. Two that I know of are made in the USA and there may be two or more others that come from offshore and marketed under different names once here.
Like anyone buying products in the marketplace, companies buying vacuum pumps of this physical size and cost should assess suitability for the application and value for money. Assess all the variables, including quality, technical support, parts availability and service support when evaluating a purchase.
References:
- Webb, D.B. 2002 History of Mechanical Vacuum Pumps in the United States. Presented at the SVC Annual Technical Conference (2002)
- Stokes Vacuum catalog and technical training material developed by the author
- Tuthill Vacuum & Blower Systems Kinney “KT” Series Single Stage, Triplex Rotary Piston Pumps Manual 1843-1 dated June 2003.
Copyright Howard Tring, Tring Enterprises LLC Vacuum & Low-Pressure Consulting.