BY JEFF PRITCHARD
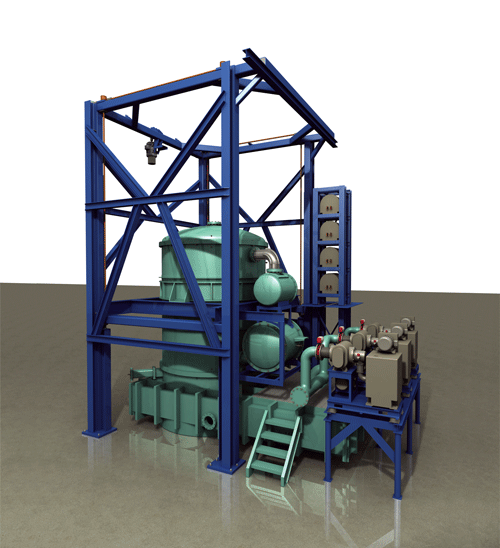
High strength steel alloys, such as 4340M, 300M, and others, are most commonly used in the manufacture of landing gear components. These alloys are hardened and tempered to produce ultimate tensile strengths exceeding 280 ksi (1,930 MPa). Vac Aero International processes landing gear components for most of the major commercial and military aircraft programs.Vacuum heat treatment offers an alternative method to traditional salt-bath and controlled-atmosphere furnace hardening techniques for high strength steels, such as AISI 4340M and 300M. However, heat treaters must be prudent when choosing between oil and gas quenching for vacuum hardening of high strength steels, because each process has its advantages and disadvantages.
Prior to 1980, Vac Aero used salt bath heat treating for hardening landing gear components (Fig. 1). While salt bath heat treating is still widely used today, it has some inherent disadvantages. For example, even though parts are thoroughly washed after processing, there is still a risk that corrosive salt residues can become trapped in narrow recesses or blind holes. In addition, the washing process itself generates large volumes of contaminated waste liquid, which must be properly disposed of. Also, salt baths generate hazardous fumes, create operator safety concerns, and present a high risk of accidental fire.
Oil quenching from controlled atmosphere furnaces can overcome many of the disadvantages associated with processing in salt. However, while both salt bath and controlled-atmosphere heat treating processes provide a high degree of protection to the steel, some partial decarburization and high temperature oxidation still occur. Therefore, for critical surfaces, substantial final machining envelopes must be left in place prior to heat treating. Removing these envelopes after the steel is hardened can be difficult and expensive. These concerns led Vac Aero engineers to develop vacuum oil quenching techniques. Because vacuum furnaces are inherently leak tight, control of surface chemistry is precise, and the decarburization and high-temperature oxidation problems often associated with salt baths and controlled-atmosphere furnaces can be eliminated.
Vacuum Oil Quenching
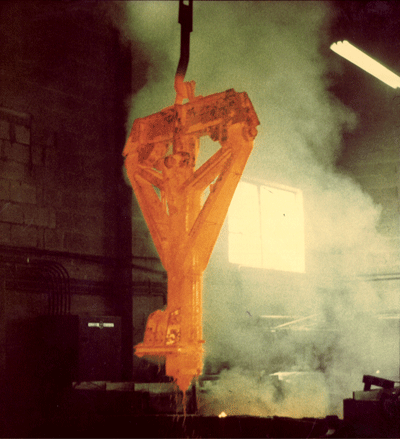
The high interest of aerospace customers with the company’s vacuum oil quenching process led to the need for a second furnace to satisfy the demand. The second unit (Fig. 2) incorporated some new design features to enhance the process based on experience gained over the ten-year operating period of the first vacuum oil quench furnace. For example, the unit incorporates a vacuum tight seal door between the heating chamber and quench tank; isolation of the quench tank from the heating chamber is complete when the seal door is closed. The furnace also has separate mechanical pumping systems to evacuate the heating chamber and quench tank, which results in lower vacuum levels and reduced impurities in the heating chamber creating an even cleaner environment in which to process the load. The furnace can accommodate workloads up to 73 in. diameter and 118 in. high (1,830 and 3,000 mm) and gross load weights up to 3,500 lb (7,700 kg).Vac Aero in 1980 put into operation its first direct oil quenching vacuum furnace designed for heat treating large aircraft landing gear components. The furnace remains in full production use today. The furnace consists of a gantry mounted heating chamber and about a 9,000-gal (34,000 liter) capacity oil quench tank equipped with a load elevator. A set of thermal barrier doors shields the quench tank from the radiant heat of the heating chamber. The entire quenching sequence takes less than 10 seconds.
The system consists of a heating chamber, gas quench system, insulation (thermal barrier) door chamber, and seal door chamber mounted on a moveable gantry. In a pit below are oil quench and reservoir tanks equipped with oil heaters and coolers. A schematic of the furnace is shown in Fig. 3. The oil quench tank has a capacity of 10,770 gal (44,500 liters) and contains a high speed elevator and impellors to agitate the oil.
Automated Cycle
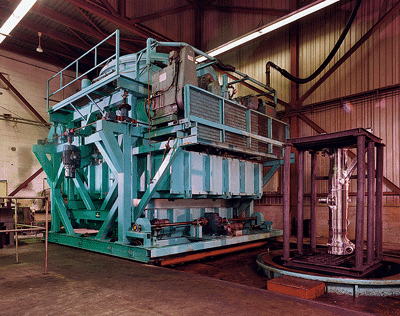
While these processes are underway, the quench oil is pumped from the reservoir tank back into the quench tank. The quench tank is evacuated and backfilled with a partial pressure of nitrogen to slightly below atmospheric pressure. The load is preheated then austenitized according to specification requirements. At the beginning of the quenching sequence, the heating chamber is backfilled with nitrogen to a pressure equal to that in the quench tank. Power to the heating elements remains on during backfill to prevent heat loss in the load. The seal door opens and the elevator ascends to raise the load slightly above the hearth upon which the insulation doors open and the elevator quickly lowers the load into the quench tank. Quench delay in this process for a full 118 in. high load is less than 10 seconds. While the load is cooling in the quench tank, the gas quench system activates to cool the heating chamber in preparation for accepting the next load.A typical hardening cycle is fully automated. For loading, the chamber assemblies are raised several inches from the quench tank flange by motor driven screw jacks, oil is pumped from the quench tank to the reservoir tank, and the gantry is moved away from the quench tank. The quench tank elevator is raised, the load is placed on it, and the elevator and load are lowered into the quench tank. The gantry is moved back into position and lowered until the bottom of the seal door chamber is sealed on the quench tank flange. The seal door and insulation doors open and the elevator raises the load into the heating chamber. As the elevator descends back into the quench tank the insulation doors, which also serve as the furnace hearth, close and receive the load. After the elevator is withdrawn, the seal door closes to isolate the heating chamber from the quench tank, the heating chamber is evacuated, and heating begins.
A third, larger vacuum oil quench furnace, commissioned in December of 2005, was built for hardening very large components such as those being developed for the landing gear in the Airbus A380. The unit operates mostly on the same principles as its predecessor.
Control of Distortion
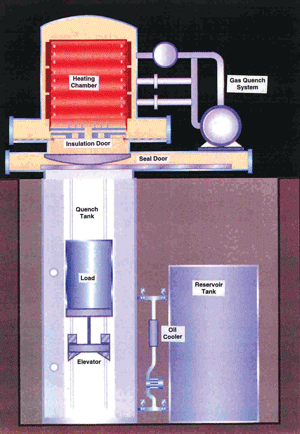
Several techniques can be used to control distortion during heat treating. For components that become highly stressed from operations prior to the hardening treatment, such as forging and/or machining, a separate stress relief cycle may be required. However, in most cases, these residual stresses can be relieved during the hardening cycle by slowing the heating rate.The thermal shock induced by quenching hot steel in oil almost always causes some degree of dimensional distortion in the steel. Distortion can also be compounded by stress-inducing manufacturing processes such as forging or machining that take place prior to heat treating. The primary advantage of Vac Aero’s vacuum oil quenching technology is the precise control of surface chemistry that allows leaving minimal or no machining envelope on the component prior to heat treating. The challenge in vacuum hardening then becomes counteracting distortion in the absence of a final machining envelope to yield a heat treated component within the required dimensional tolerances.
Fixturing techniques are also important for control of distortion. Long components are usually hung from a fixture to take advantage of the force of gravity as a stabilizing influence. Components incorporating major differences in section thicknesses are especially prone to distortion due to different rates of heating and cooling between thin and thick sections. For these components, heat sinks are sometimes attached to the thinner sections to provide a better thermal balance. Oil composition, temperature and agitation can also affect distortion. Some oil compositions are designed to achieve higher quenching speeds than others. High-speed oils are preferred for hardening very thick sections and achieving maximum strength in steels having lower hardenability. However, they can also cause greater levels of distortion in thin sections or in steels having high hardenability. Cooler, more highly agitated oil also creates more thermal shock. Oil temperature and agitation are carefully regulated in specific hardening applications by using controls device built into the quench tank.
Interrupted quenching techniques such as ausbay quenching also offer good potential for reducing distortion in certain grades of high strength steel. Vac Aero designed such a capability into its latest model vacuum oil quench furnace. Ausbay quenching involves rapidly cooling the steel from the austenitizing temperature to an intermediate temperature above that where martensitic transformation begins. The intermediate temperature range corresponds to a wide austenitic “bay” region on the isothermal transformation diagrams for the steel. Cooling from the austenitizing temperature to the ausbay region must be sufficiently fast to avoid the nose of the transformation curve and corresponding formation of undesirable products of austenitic transformation. This is accomplished by activating the gas quench system.
With heating element power off, the gas quenching process continues until the temperature of the load reaches about 1000°F (540°C). The rate of cooling during the gas quenching stage must be carefully controlled so that it is fast enough to avoid any decomposition of austenite but not so fast that the load is cooled below the required ausbay temperature. The flow of gas circulated through the load during the quenching stage is regulated by a damping valve in the inlet of the manifold. Normally open for maximum cooling rate, this valve starts to close as the ausbay temperature is approached. Power to the heating elements is also gradually returned. Both quench gas flow and heating element power are automatically regulated through the use of microprocessors in the furnace control system. Input from thermocouples in the heating chamber provides the microprocessors with real-time data so cooling rate corrections are made instantaneously.
When the gas quench system is deactivated, sufficient power is applied to the heating elements to maintain the load at the ausbay temperature, where it is held at the soaking temperature until a uniform temperature is achieved throughout the workload. Many high strength steels can be held in the ausbay temperature range for several hours without any austenitic transformation. After a sufficient soak, the load is quenched in oil using the same sequence of events as described previously. By interrupting the cooling process, the ausbay quenching technique reduces thermal shock and the stresses it creates. This results in corresponding improvements in dimensional stability of the heat treated component.
Vac Aero uses this technique on several critical landing gear components fabricated of 300M steel. Comprehensive analyses show that ausbay quenching can reduce quench-related distortion in these components by more than 50% compared with direct oil quenching.
High Pressure Gas Quenching
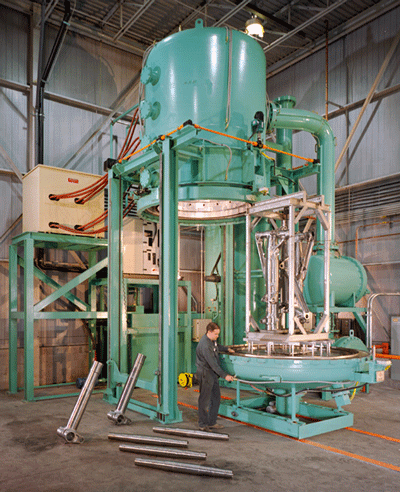
In terms of distortion control, it is widely assumed that because gas quenching creates less thermal shock than oil quenching it should produce less quench-related distortion. In 1998, Vac Aero commissioned a large bottom-loading vacuum gas quench furnace with a 10 bar pressure quenching capability (Fig. 4). A number of trials were performed on different components to compare distortion caused by oil quenching with that caused by high pressure gas quenching. Surprisingly, it was determined that for many components, distortion caused by gas quenching was greater than caused by oil quenching. Further analysis indicated that gas velocity is one of the primary factors determining cooling efficiency during gas quenching. Gas velocity was found to decrease sharply beyond a distance of about 18 in. (460 mm) from the gas quench nozzle. The quench nozzles are located in circumferential rows within the furnace. The distance from a quench nozzle to the component being quenched can vary significantly over the entire surface of the component, particularly on larger components. Hence, the gas velocity and, therefore, the cooling rate can vary significantly at different points on the surface of the component. Differential cooling rates within an individual component can cause stresses that lead to distortion. Oil quenching provides more uniform cooling as all surfaces of the load are quickly enveloped by the quenching medium.Many aerospace heat treating specifications now permit vacuum hardening of limited section thicknesses of certain high strength steels by gas quenching at pressures of 5 bar or higher. The process is becoming increasingly popular because vacuum gas quench furnaces are generally less expensive to operate than vacuum oil quench furnaces and offer some further environmental advantages. The development of high pressure gas quenching was based on the principle that the denser the cooling medium, the more heat will be extracted from the load. By pressurizing, the quench gas becomes more dense and has improved heat transfer properties. In addition to the pressure of the quench gas, the cooling efficiency of the system is influenced by other factors such as the type of quench gas used, the velocity of the gas, and design factors related to the size and shape of the chamber in which the quenching is taking place.
A conclusion derived from this is that cooling during high pressure gas quenching, though still fast enough to produce full mechanical properties in the steel, is less uniform than that achieved in oil quenching, therefore sometimes causes greater distortion.
Another phenomenon evident during the company’s high pressure gas quench studies involved the tensile properties of 300M (essentially a modified AISI 4340 steel with silicon, vanadium, and slightly higher carbon and molybdenum contents than 4340) steel. In controlled experiments, ultimate tensile strengths for gas quenched and tempered specimens of 300M often exceeded 300 ksi (2,068 MPa) versus typical strengths between 285 and 295 ksi (1,965 and 2,034 MPa) for oil quenched and tempered specimens. Similar trends have also been reported by others. Electron microscopy analyses, while not completely conclusive, strongly suggest the presence of bainite in the gas quenched specimens having the highest ultimate tensile strengths. A fully martensitic structure was evident in all of the oil quenched specimens. The presence of bainite in the microstructure could have negative effects on the performance of aircraft structural components.
Summary
Heat treaters must be prudent when choosing between oil and gas quenching for vacuum hardening of high strength steels. Each process has its advantages and disadvantages. Through practical experience, Vac Aero has concluded that high pressure gas quenching is better suited for smaller parts where distortion is not a primary concern. The process should also be performed in smaller vacuum furnaces where high gas velocities can be maintained throughout the working area making cooling more uniform. The restrictions on section thicknesses that can be successfully hardened by high pressure gas quenching also limit its use, so it is likely to replace oil quenching in only a small number of applications.